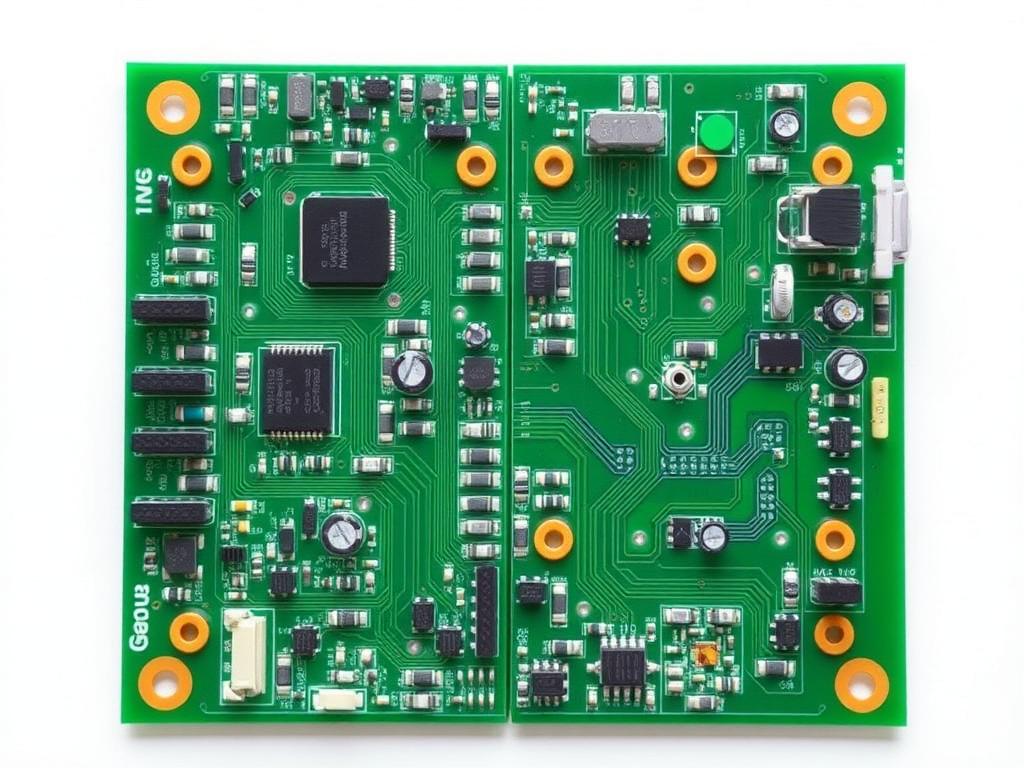
What is pcb panelization depanelization methods
The Ultimate Guide to PCB Panelization and Depaneling: Maximizing Efficiency in Electronics Manufacturing
Are you looking to optimize your PCB manufacturing process and reduce production costs? PCB panelization and depaneling are crucial techniques that can dramatically improve your electronics manufacturing efficiency. In this comprehensive guide, we’ll explore everything from basic concepts to advanced strategies, helping you make informed decisions for your production needs.
What is PCB Panelization and Why is it Essential for Modern Electronics Manufacturing?
PCB panelization is a manufacturing technique where multiple individual PCBs are combined into a larger panel for efficient production. This process is fundamental to modern electronics manufacturing, especially for high-volume production runs. Leading manufacturers like PCB Router Machine specialists have revolutionized this process with advanced equipment and techniques.Key benefits include:
- Increased production efficiency
- Reduced handling time
- Better component placement accuracy
- Lower manufacturing costs
- Enhanced quality control
Understanding Different PCB Depaneling Methods
1. V-Groove Depaneling
The V-groove depaneling process involves:
- Creating V-shaped grooves on both sides of the PCB
- Precise depth control for clean separation
- Minimal stress on components
- Ideal for rigid PCBs
2. Tab Routing
Tab routing is particularly effective for:
- Complex board shapes
- Flexible PCBs
- Boards with sensitive components
- Custom panel layouts
3. Laser Depaneling
Modern laser depaneling systems offer:
- Contact-free separation
- High precision cutting
- Minimal thermal stress
- Perfect for flexible circuits
How to Choose the Right Depaneling Method for Your Project?
Consider these factors:
- Board material and thickness
- Component proximity to edges
- Production volume requirements
- Quality requirements
- Budget constraints
Method | Best For | Limitations |
---|---|---|
V-Groove | High-volume, straight-line cuts | Limited to straight lines |
Tab Routing | Complex shapes, flexible PCBs | Slower than V-groove |
Laser | High-precision, sensitive components | Higher initial investment |
Advanced PCB Panelization Design Considerations
When designing PCB panels, consider:
- Component clearance
- Panel rigidity
- Tooling holes placement
- Break-routing requirements
- Material optimization
The Impact of Proper Panelization on Manufacturing Costs
Effective panelization can reduce costs by:
- Minimizing material waste
- Increasing throughput
- Reducing handling time
- Improving yield rates
Common Challenges in PCB Depaneling and How to Overcome Them
Challenge 1: Component Damage
Solution: Use appropriate automated depaneling equipment with controlled force application
Challenge 2: Edge Quality
Solution: Implement proper tooling and maintenance schedules
Challenge 3: Production Speed
Solution: Choose the right combination of panelization methods and equipment
Frequently Asked Questions
What is the most cost-effective depaneling method? V-groove depaneling is typically most cost-effective for high-volume production with straight-line separations.How close can components be to the depaneling area? Generally, components should be at least 0.5mm away from V-grooves and 1mm from routing paths.What are the advantages of laser depaneling? Laser depaneling offers stress-free separation, high precision, and is ideal for flexible circuits and sensitive components.Which depaneling method is best for flexible PCBs? Laser depaneling and specialized routing systems are most suitable for flexible PCBs.
Future Trends in PCB Panelization and Depaneling
Emerging trends include:
- AI-powered depaneling systems
- Advanced material handling automation
- Integrated quality control systems
- Smart factory integration
Key Takeaways:
• Choose the right depaneling method based on your specific requirements • Consider component placement during panel design • Invest in quality equipment for better results • Maintain proper maintenance schedules • Stay updated with latest technologies
For professional PCB depaneling solutions and expert consultation, contact our team at PCB Depaneling Specialists. We serve industry leaders like TP-LINK, Canon, BYD, and Foxconn with state-of-the-art equipment and unmatched expertise.