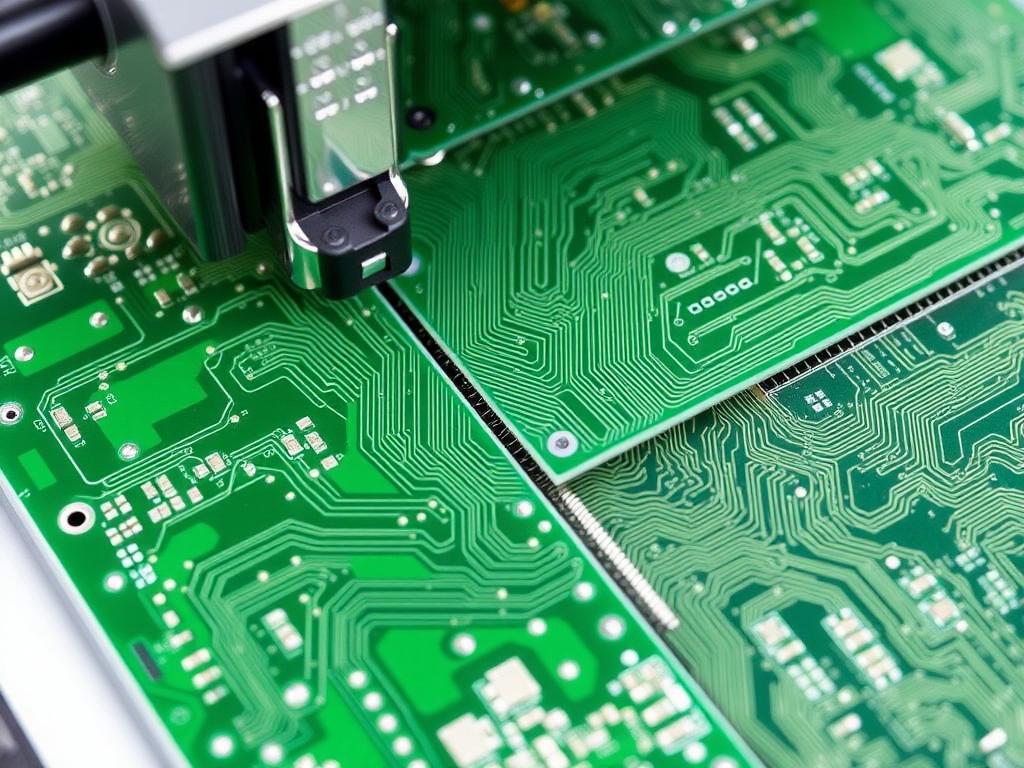
V-groove PCB depaneling
Efficient PCB Depaneling: Revolutionizing Printed Circuit Board Separation 🛠️
In the fast-paced world of electronics manufacturing, efficiency and precision are paramount. PCB depaneling, the process of separating individual printed circuit boards (PCBs) from a larger panel, plays a crucial role in ensuring high-quality production. This article delves into the intricacies of PCB depaneling, exploring advanced depaneling machines, innovative V-cut and V-groove techniques, and how industry leaders like Manncorp Inc. are shaping the future of PCB manufacturing. Whether you’re a seasoned engineer or new to PCB production, understanding these processes is essential for optimizing your manufacturing workflow.
What is PCB Depaneling and Why is it Important?
PCB depaneling is the critical process of separating individual printed circuit boards from a larger manufacturing panel. During the manufacturing process, multiple PCBs are often produced simultaneously on a single panel to maximize efficiency and reduce costs. Once the manufacturing is complete, these PCBs need to be accurately and efficiently separated without causing any damage.
Depaneling is essential because it ensures that each PCB maintains its integrity and functionality. Efficient PCB separation minimizes mechanical stress on the boards, reducing the risk of fractures or defects. This precision is crucial for maintaining high-quality standards and ensuring that the final products perform reliably in their intended applications.
Moreover, effective depaneling contributes to the overall throughput of the manufacturing process. By using advanced depaneling machines and techniques, manufacturers can achieve faster separation times, thereby increasing productivity and meeting tight production schedules.
Types of PCB Depaneling Methods: Which One Suits Your Needs?
There are several depaneling methods available, each with its own set of advantages and limitations. The choice of depaneling method depends on various factors, including the type of PCB, production volume, and desired precision.
Saw Depaneling
Saw depaneling is one of the most common methods, where a saw blade is used to cut through the PCB panel. This method is suitable for high-throughput production and can handle large panel sizes. However, it may introduce mechanical stress, which can affect the integrity of delicate PCBs.
V-Cut Depaneling
V-cut depaneling involves making a V-shaped groove in the PCB panel, allowing the individual boards to be snapped apart with minimal mechanical stress. This method is ideal for thin and flexible PCBs, as it reduces the risk of cracking or breaking during separation.
Punch Depaneling
Punch depaneling uses a punch and die system to create precise holes in the PCB panel, facilitating easy separation. This method is highly accurate and suitable for complex PCB designs. It also minimizes mechanical stress, ensuring high-quality separation.
Laser Depaneling
Laser depaneling employs a laser beam to cut through the PCB panel with high precision. This method offers excellent accuracy and is capable of handling intricate PCB designs. It also reduces mechanical stress, making it ideal for high-density and flexible PCBs.
Each depaneling method has its unique benefits, and the choice depends on the specific requirements of your PCB manufacturing process. Understanding these methods helps in selecting the most appropriate technique to ensure efficient and precise PCB separation.
How Do Depaneling Machines Enhance PCB Manufacturing?
Depaneling machines play a pivotal role in modern PCB manufacturing by automating the separation process, ensuring consistency, and improving overall efficiency. These machines are designed to handle various depaneling methods, including saw, V-cut, and punch depaneling, offering versatility to manufacturers.
Increased Throughput
Depaneling machines significantly increase the throughput of the manufacturing process. By automating the separation, these machines can handle large volumes of PCB panels quickly and accurately, reducing the time required for manual depaneling.
Precision and Consistency
One of the key advantages of using depaneling machines is the precision they offer. These machines are equipped with advanced control systems that ensure each cut is consistent and accurate, minimizing the risk of defects and ensuring high-quality PCBs.
Reduced Mechanical Stress
Advanced depaneling machines are designed to minimize mechanical stress on the PCBs during separation. Techniques like V-groove and punch depaneling ensure that the individual boards are separated cleanly without causing damage, enhancing the reliability of the final products.
Enhanced Safety
Depaneling machines improve workplace safety by automating the separation process. This reduces the need for manual intervention, lowering the risk of accidents and injuries associated with manual depaneling methods.
Overall, depaneling machines streamline the PCB manufacturing process, enhancing productivity, quality, and safety.
V-Cut vs. V-Groove: Understanding the Differences
V-cut and V-groove are two popular depaneling techniques used in PCB manufacturing. While both methods involve creating a V-shaped groove in the PCB panel, there are key differences that affect their suitability for different applications.
V-Cut Depaneling
V-cut depaneling involves making a V-shaped cut along the edges of the individual PCBs within the panel. This allows the boards to be easily snapped apart with minimal mechanical stress. V-cut is ideal for thin and flexible PCBs, as it reduces the risk of cracking or breaking during separation.
V-Groove Depaneling
V-groove depaneling, on the other hand, creates deeper and more precise grooves, enabling clean and accurate separation of the PCBs. This method is particularly suitable for high-density and multi-layer PCBs, where precision is critical to maintain the integrity of the boards.
Key Differences
- Depth of Groove: V-groove depaneling typically involves deeper grooves compared to V-cut depaneling, providing better separation for complex PCB designs.
- Precision: V-groove depaneling offers higher precision, making it suitable for high-density PCBs with intricate patterns.
- Mechanical Stress: Both methods aim to reduce mechanical stress, but V-groove depaneling provides a more controlled separation process, ensuring minimal stress on the boards.
Choosing between V-cut and V-groove depaneling depends on the specific requirements of your PCB design and manufacturing process. V-cut is preferable for simpler, flexible PCBs, while V-groove is better suited for complex, high-density boards.
Choosing the Right PCB Depaneling Machine: Key Considerations
Selecting the appropriate PCB depaneling machine is crucial for optimizing your manufacturing process. Here are the key factors to consider when choosing a depaneling machine:
Depaneling Method Compatibility
Ensure that the depaneling machine supports the depaneling methods suitable for your PCBs, such as V-cut, V-groove, saw, or punch depaneling. Versatility in handling different methods can enhance the flexibility of your manufacturing process.
Throughput and Speed
Consider the production volume and required throughput when selecting a depaneling machine. Machines with higher speed and capacity can handle large volumes efficiently, reducing production time and increasing overall productivity.
Precision and Accuracy
Precision is critical in PCB depaneling to maintain the integrity of the boards. Choose a depaneling machine that offers high accuracy and consistency in cuts, minimizing the risk of defects and ensuring high-quality PCBs.
Ease of Use and Maintenance
Opt for depaneling machines that are user-friendly and easy to maintain. Features like automated settings, easy access for maintenance, and user-friendly interfaces can simplify operations and reduce downtime.
Cost and Return on Investment
Evaluate the cost of the depaneling machine in relation to its features and benefits. Consider the return on investment (ROI) by assessing how the machine will improve efficiency, reduce defects, and enhance overall production quality.
Brand Reputation and Support
Choose depaneling machines from reputable brands like Manncorp Inc., known for their reliability and customer support. Good after-sales service and availability of spare parts are essential for maintaining the machine’s performance and longevity.
By carefully considering these factors, you can select the right PCB depaneling machine that meets your manufacturing needs and enhances your production capabilities.
The Role of Routers in PCB Depaneling
Routers are integral components in PCB depaneling machines, responsible for executing precise cuts along the PCB panel. They play a vital role in ensuring accurate and efficient separation of individual boards.
Types of PCB Routers
There are primarily two types of routers used in PCB depaneling: CNC routers and manual routers.
- CNC Routers: Computer Numerical Control (CNC) routers offer high precision and automation, making them ideal for high-volume and complex PCB depaneling tasks. They are equipped with advanced control systems that ensure consistent and accurate cuts.
- Manual Routers: Manual routers require operator intervention for each cut, offering flexibility for small-scale or custom PCB depaneling. While they are less automated than CNC routers, they are suitable for projects requiring frequent adjustments.
Router Bits and Tools
The choice of router bits is crucial for achieving precise depaneling. High-quality router bits, such as round blade V-cut and saw blade V-groove router bits, ensure clean and accurate cuts, minimizing mechanical stress on the PCBs.
- Round Blade V-Cut: Ideal for creating shallow grooves, suitable for thin and flexible PCBs.
- Saw Blade V-Groove: Suitable for deeper grooves and high-density PCBs, providing enhanced precision.
Enhancing Depaneling Efficiency
Routers contribute to the efficiency of the depaneling process by enabling rapid and accurate cuts. Advanced router systems, such as the V-groove PCB depaneling machine CY-203, incorporate motorized routers that automate the cutting process, increasing throughput and reducing manual labor.
Minimizing Mechanical Stress
Proper routing techniques minimize mechanical stress on the PCBs during separation. V-groove and V-cut routing ensure that the boards are separated cleanly without causing fractures or defects, maintaining the integrity of each PCB.
Incorporating high-quality routers into your PCB depaneling process enhances precision, efficiency, and reliability, contributing to the overall quality of your printed circuit boards.
Common Challenges in PCB Depaneling and How to Overcome Them
PCB depaneling, while essential, presents several challenges that manufacturers must address to ensure efficient and high-quality separation. Understanding these challenges and implementing effective solutions can significantly enhance the depaneling process.
Mechanical Stress and PCB Damage
One of the primary challenges in PCB depaneling is minimizing mechanical stress to prevent damage to the boards. Improper depaneling can lead to cracks, fractures, or delamination, compromising the functionality of the PCBs.
Solution: Utilize advanced depaneling methods like V-groove and V-cut, which reduce mechanical stress by allowing the boards to snap apart cleanly. Investing in high-precision depaneling machines with motorized routers ensures consistent and accurate cuts, further minimizing the risk of damage.
Precision and Accuracy
Achieving high precision and accuracy in depaneling is crucial for maintaining the integrity of the PCBs. Inaccurate cuts can result in misaligned boards, making assembly and testing difficult.
Solution: Implement CNC depaneling machines equipped with advanced control systems and high-quality router bits. Regular calibration and maintenance of depaneling machines ensure that cuts remain precise and consistent, reducing the likelihood of errors.
Throughput and Production Speed
Balancing throughput and production speed with precision can be challenging, especially in high-volume manufacturing environments. Slow depaneling processes can bottleneck production, while overly fast processes may compromise quality.
Solution: Select depaneling machines that offer a balance between speed and precision. Machines like the V-groove PCB depaneling machine CY-203 are designed to handle high-throughput depaneling without sacrificing accuracy. Additionally, optimizing the depaneling workflow and reducing manual interventions can enhance overall production speed.
Handling Complex PCB Designs
Modern PCBs often feature intricate designs with multiple layers and components, making depaneling more complex. Ensuring clean separation without damaging delicate features requires advanced depaneling techniques.
Solution: Use depaneling machines with versatile cutting tools capable of handling complex PCB designs. Laser depaneling, for instance, offers high precision for intricate patterns, while punch depaneling can accurately separate multi-layer PCBs without causing mechanical stress.
Cost Considerations
Investing in advanced depaneling machines and maintaining high precision can be costly, posing budgetary challenges for manufacturers.
Solution: Evaluate the long-term benefits of investing in high-quality depaneling machines, such as reduced defect rates and increased production efficiency. Additionally, consider machines that offer multi-method depaneling capabilities, providing flexibility and maximizing the return on investment.
By addressing these common challenges with effective solutions, manufacturers can optimize their PCB depaneling processes, ensuring high-quality production and operational efficiency.
Innovations in PCB Depaneling: The Future of Depaneling Machines
The PCB depaneling landscape is continuously evolving, driven by advancements in technology and the increasing complexity of PCB designs. Innovations in depaneling machines are enhancing precision, efficiency, and versatility, shaping the future of PCB manufacturing.
Automation and Motorization
Modern depaneling machines are increasingly incorporating automation and motorization to improve throughput and consistency. Motorized PCB depaneling machines, such as the V-groove PCB depaneling machine CY-203, offer automated cutting processes that reduce manual labor and enhance precision.
Advanced Cutting Techniques
Innovative cutting techniques, such as laser depaneling and multi-knife depaneling, are gaining popularity due to their high precision and ability to handle complex PCB designs. Laser depaneling, for instance, provides clean and accurate cuts without introducing mechanical stress, making it ideal for high-density and flexible PCBs.
Smart Depaneling Systems
The integration of smart technologies, including sensors and machine learning algorithms, is enabling depaneling machines to adapt to varying PCB designs and conditions. These intelligent systems can automatically adjust cutting parameters to optimize the depaneling process, ensuring consistent quality and reducing the need for manual intervention.
Enhanced Depaneling Tools
Advancements in depaneling tools, such as high-speed routers and precision saw blades, are enhancing the accuracy and efficiency of depaneling machines. High-quality cutter tools minimize wear and tear, maintaining cutting precision over extended periods and reducing maintenance costs.
Eco-Friendly Depaneling Solutions
Sustainability is becoming a key focus in PCB manufacturing, and depaneling machines are evolving to support eco-friendly practices. Innovations like efficient dust extraction systems and energy-efficient motors are reducing the environmental impact of depaneling processes, aligning with green manufacturing initiatives.
Customizable Depaneling Solutions
Manufacturers are increasingly seeking customizable depaneling solutions that can be tailored to specific PCB designs and production requirements. Depaneling machines with modular designs and adjustable settings offer the flexibility needed to handle a wide range of PCB types and manufacturing scenarios.
These innovations are driving the depaneling industry towards more efficient, precise, and versatile solutions, meeting the growing demands of modern PCB manufacturing.
Case Study: Manncorp Inc.’s Impact on PCB Depaneling Technology
Manncorp Inc., a leading manufacturer in the PCB depaneling industry, has been at the forefront of technological advancements, revolutionizing the depaneling process with their state-of-the-art machines and innovative solutions.
Cutting-Edge Depaneling Machines
Manncorp Inc. offers a range of PCB depaneling machines designed to meet diverse manufacturing needs. Their flagship models, such as the GAM 380AT PCB Bottom Depaneling Machine and the ZM30-ASV Fully Automatic Saw-Type V-Groove PCB Depaneling Machine, showcase their commitment to precision and efficiency. These machines incorporate advanced V-groove and V-cut techniques, ensuring clean and accurate separation of individual PCBs with minimal mechanical stress.
Technological Innovations
Manncorp Inc. continuously invests in research and development to introduce innovative depaneling technologies. Their introduction of laser depaneling machines, like the DirectLaser H5 PCB-FPC Laser Cutting Machine, exemplifies their dedication to providing high-precision and efficient depaneling solutions. These laser machines offer superior accuracy, making them ideal for complex and high-density PCB designs.
Customer-Centric Solutions
Understanding the diverse needs of PCB manufacturers, Manncorp Inc. offers customizable depaneling solutions tailored to specific requirements. Their depaneling systems are designed to integrate seamlessly into existing manufacturing workflows, enhancing productivity and reducing downtime. Additionally, Manncorp Inc. provides comprehensive support and training, ensuring that customers can maximize the benefits of their depaneling machines.
Commitment to Quality and Reliability
Manncorp Inc. prioritizes quality and reliability in their depaneling machines. Each machine undergoes rigorous testing to ensure it meets high standards of performance and durability. Their focus on quality ensures that customers receive dependable machines that deliver consistent and accurate depaneling results, contributing to the overall success of their PCB manufacturing operations.
Industry Leadership and Impact
Manncorp Inc.’s innovations have significantly impacted the PCB depaneling industry, setting new benchmarks for efficiency and precision. Their advanced depaneling machines have enabled manufacturers to achieve higher throughput, reduce defect rates, and enhance the quality of their PCBs. By leading the way in depaneling technology, Manncorp Inc. has established itself as a trusted partner in the PCB manufacturing sector.
Manncorp Inc.’s contributions to PCB depaneling technology highlight the importance of innovation and quality in driving industry progress. Their cutting-edge solutions continue to shape the future of PCB manufacturing, providing manufacturers with the tools they need to achieve excellence.
Request a Quote: How to Select the Best Depaneling Solution for Your Business
Selecting the right depaneling solution is crucial for optimizing your PCB manufacturing process. Whether you’re a small-scale manufacturer or a large enterprise, obtaining a tailored depaneling machine that meets your specific needs can significantly enhance your production efficiency and product quality. Here’s how to request a quote and choose the best depaneling solution for your business.
Assess Your Manufacturing Requirements
Before requesting a quote, it’s essential to assess your manufacturing requirements. Consider factors such as:
- Production Volume: Determine your average and peak production volumes to select a depaneling machine that can handle your throughput needs.
- PCB Complexity: Evaluate the complexity of your PCB designs, including the number of layers and the presence of delicate components, to choose a machine capable of precise and reliable depaneling.
- Depaneling Method: Identify the depaneling methods that best suit your PCBs, whether it’s V-cut, V-groove, saw, or laser depaneling.
Research Depaneling Machine Providers
Research reputable depaneling machine providers like Manncorp Inc., known for their advanced technology and reliable solutions. Look for providers that offer a range of machines catering to different depaneling methods and production scales. Review customer testimonials and case studies to gauge the effectiveness and reliability of their machines.
Contact Providers and Request a Quote
Reach out to selected depaneling machine providers and request a detailed quote. When requesting a quote, provide comprehensive information about your manufacturing needs, including:
- PCB Specifications: Share details about your PCB sizes, types, and designs to help providers recommend the most suitable machines.
- Depaneling Requirements: Specify your preferred depaneling methods and any specific features you require, such as automation, precision, or high throughput.
- Budget Constraints: Outline your budget to ensure the quote aligns with your financial expectations.
Evaluate Quotes and Compare Features
Once you receive quotes, evaluate them based on the following criteria:
- Machine Specifications: Compare the specifications of each machine, including cutting precision, throughput capacity, and supported depaneling methods.
- Total Cost of Ownership: Consider not just the initial cost but also the long-term maintenance, operation, and support expenses.
- After-Sales Support: Assess the level of after-sales support provided, including training, maintenance services, and availability of spare parts.
Make an Informed Decision
Based on your evaluation, select the depaneling machine that best meets your requirements and offers the best value for your investment. Ensure that the provider can deliver the machine within your timeline and offer reliable support to facilitate seamless integration into your manufacturing process.
By following these steps, you can effectively request a quote and choose the best depaneling solution that enhances your PCB manufacturing efficiency and product quality.
Key Takeaways
- PCB Depaneling is essential for separating individual PCBs from a larger panel without causing damage.
- Depaneling Machines enhance manufacturing by increasing throughput, precision, and reducing mechanical stress.
- V-Cut vs. V-Groove: V-cut is ideal for thin, flexible PCBs, while V-groove offers higher precision for complex, high-density boards.
- Choosing the Right Machine involves considering depaneling methods, throughput, precision, ease of use, cost, and brand reputation.
- Routers play a crucial role in achieving precise and efficient PCB separation.
- Common Challenges include mechanical stress, precision, throughput, handling complex designs, and cost considerations.
- Innovations in depaneling machines focus on automation, advanced cutting techniques, smart systems, enhanced tools, eco-friendly solutions, and customization.
- Manncorp Inc. exemplifies industry leadership with their advanced depaneling machines and commitment to quality.
- Requesting a Quote involves assessing your needs, researching providers, contacting them with detailed requirements, evaluating quotes, and making an informed decision.
By understanding the various aspects of PCB depaneling and leveraging advanced