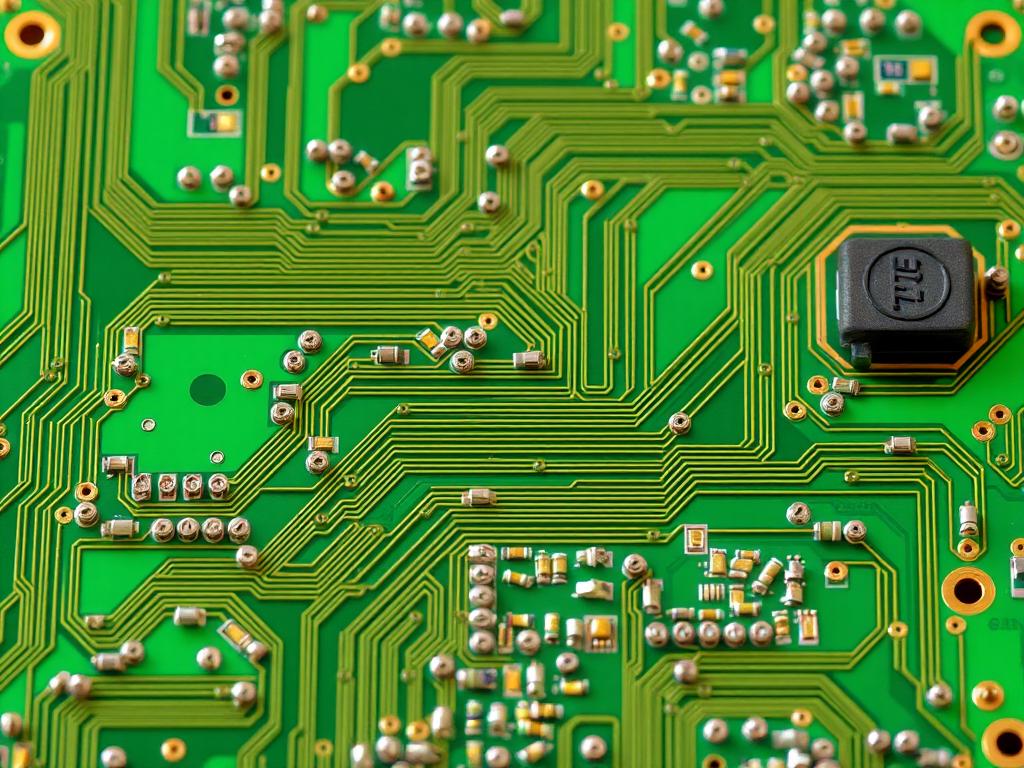
SMT reflow oven
The Ultimate Guide to SMT Reflow Ovens: Revolutionizing Modern Electronics Manufacturing
Electronics manufacturing has evolved dramatically, and at the heart of this evolution lies the SMT reflow oven – a crucial piece of equipment that determines the quality and reliability of electronic assemblies. This comprehensive guide will walk you through everything you need to know about reflow ovens, from basic concepts to advanced applications, helping you make informed decisions for your electronics manufacturing needs.
What Is an SMT Reflow Oven and Why Is It Essential?
A reflow oven is sophisticated equipment designed for soldering surface mount components to printed circuit boards using controlled heat profiles. Modern SMT reflow ovens use convection heating technology to ensure uniform temperature distribution across the PCB surface. This precision heating process is critical for:
- Consistent solder joint quality
- Reduced defect rates
- Higher production throughput
- Compatibility with lead-free soldering requirements
Learn more about our advanced PCB manufacturing solutions
How Does Reflow Soldering Technology Work?
The reflow soldering process involves several critical stages:
- Preheat Zone: Gradually warms the PCB to prevent thermal shock
- Soak Zone: Activates flux and allows for temperature equalization
- Reflow Zone: Reaches peak temperature for proper solder melting
- Cooling Zone: Controlled cooling for optimal joint formation
Temperature control and profile management are crucial for successful reflow soldering operations.
Types of Reflow Ovens: Which One Suits Your Needs?
Convection Reflow Ovens
- Forced hot air circulation
- Excellent temperature uniformity
- Ideal for lead-free applications
Infrared Reflow Ovens
- Direct heating through IR radiation
- Fast heating capability
- Cost-effective for smaller operations
Check out our integrated SMT production line solutions
Key Features to Consider When Choosing a Reflow Oven
- Temperature Control Accuracy
- Multiple heating zones
- Digital temperature monitoring
- Profile programming capabilities
- Production Capacity
- Conveyor width and speed
- Maximum board size
- Throughput requirements
Advanced Technologies in Modern Reflow Ovens
Today’s reflow ovens incorporate sophisticated features:
- Programmable temperature profiles
- Real-time process monitoring
- Hot air convection systems
- Lead-free soldering compatibility
Explore our high-precision manufacturing equipment
Common Challenges and Solutions in Reflow Soldering
Temperature Profile Management
- Challenge: Achieving consistent heating across different board sizes
- Solution: Multiple heating zones with independent control
Lead-Free Soldering Requirements
- Challenge: Higher melting points of lead-free alloys
- Solution: Advanced temperature control systems
Maintenance and Optimization Tips
Regular maintenance ensures optimal performance:
- Clean heating elements monthly
- Check conveyor belt tension
- Calibrate temperature sensors
- Monitor process gas consumption
View our comprehensive maintenance solutions
Industry Standards and Compliance
Modern reflow ovens must meet various standards:
- IPC-7530 Guidelines
- RoHS compliance
- JEDEC specifications
- ISO quality standards
Cost Considerations and ROI Analysis
Investment factors to consider:
- Initial equipment cost
- Operating expenses
- Maintenance requirements
- Production volume needs
Frequently Asked Questions
How long does a typical reflow process take?
The complete reflow process typically takes 3-5 minutes, depending on the profile and board complexity.
What temperature range is needed for lead-free soldering?
Lead-free soldering typically requires peak temperatures between 235-250°C.
Can a reflow oven handle different board sizes?
Most modern ovens can accommodate various board sizes within their specified width range.
What maintenance schedule is recommended?
Daily visual inspections and monthly deep cleaning are recommended for optimal performance.
Key Takeaways
- Choose the right reflow oven based on your production needs
- Maintain proper temperature profiles for optimal results
- Regular maintenance ensures consistent performance
- Consider future production requirements when selecting equipment
- Partner with experienced manufacturers for best results
Contact us for expert guidance on PCB manufacturing equipment
This comprehensive guide demonstrates how modern reflow ovens are revolutionizing electronics manufacturing. For more information about our complete range of PCB manufacturing solutions, including laser depaneling and automatic handling systems, please visit our website or contact our technical team.