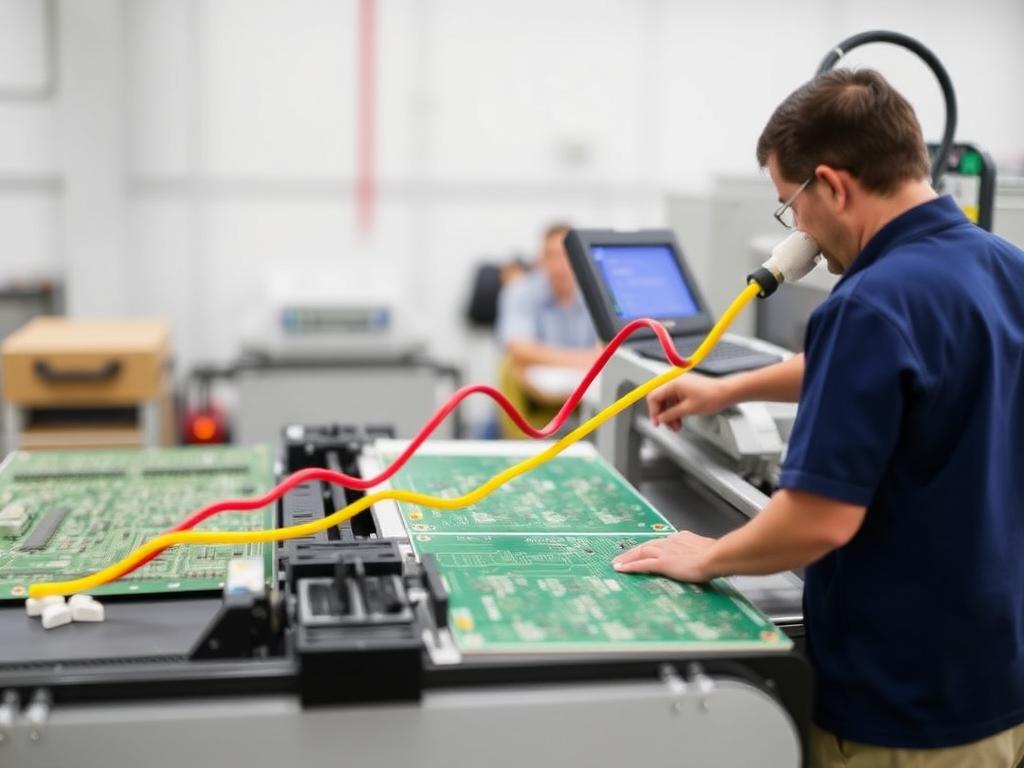
SMT production line
Everything You Need to Know About SMT Assembly Lines: A Comprehensive Guide for Mass Production of Electronics
This article provides a comprehensive overview of SMT (surface mount technology) assembly lines, a critical aspect of modern electronics manufacturing. Drawing from my 20 years of experience in the PCB industry, I’ll share insights into the SMT manufacturing process, the main equipment involved, and the key considerations for setting up and optimizing an SMT production line. Whether you’re an established electronics technology company, part of a large electronic product processing factory, or an individual PCB player, this article is your one-stop resource for understanding SMT and its role in achieving efficient, high-quality mass production of electronics products, such as PCBA. It will help you to understand the complexities of SMT assembly and how it can significantly impact your production efficiency and product quality.
Article Outline
H2: What is SMT (Surface Mount Technology) and Why is it Important?
SMT, or surface mount technology, has revolutionized the electronics industry. It’s a method where electronic components are mounted directly onto the surface of a printed circuit board (PCB). Unlike the older through-hole technology, where component leads are inserted into holes in the PCB, SMT allows for smaller components and higher component density, leading to smaller, more powerful electronic devices. This technology is crucial for mass production as it enables automation, reduces manufacturing time, and improves product reliability.
SMT stands for surface mount technology. It is a method for constructing electronic circuits in which components are mounted directly onto the surface of printed circuit boards (PCBs). SMT has largely replaced through-hole technology due to its efficiency and ability to accommodate smaller components. Surface mount technology allows for a higher density of components on the PCB, leading to smaller and more compact electronic devices. This is particularly important in industries like consumer electronics, where miniaturization is a key trend. The use of surface-mounted devices also improves the high-frequency performance of circuits, making SMT essential for modern electronic devices.
H2: What is an SMT Assembly Line and How Does it Work?
An SMT assembly line is a series of machines used to assemble electronic circuit boards. It’s a highly automated production line where each machine performs a specific step in the assembly process. From applying solder paste to placing components and soldering them to the PCB, the SMT line ensures a streamlined and efficient manufacturing process. The use of automated assembly machines minimizes human error, enhances production speed, and ensures consistent quality across all PCBs produced.
An SMT assembly line is a sequence of automated machines that work together to assemble a printed circuit board assembly (PCBA). The assembly process typically begins with solder paste printing, where a stencil printer applies solder paste to the PCB pads. Next, a pick-and-place machine precisely places SMT components onto the PCB. The board then passes through a reflow oven, where the solder paste melts and creates a strong solder joint between the components and the PCB. Finally, the assembled PCB undergoes inspection to ensure quality. Surface mount assembly lines are designed for high-volume production, and they offer significant advantages in terms of speed, accuracy, and cost-effectiveness.
H2: What is the SMT Manufacturing Process?
The SMT manufacturing process is a multi-step procedure that transforms a bare PCB into a fully functional electronic assembly. It begins with PCB design and fabrication, followed by solder paste application, component placement, reflow soldering, inspection, and testing. Each step plays a vital role in ensuring the quality and reliability of the final product. The process requires precision, automation, and meticulous quality control to achieve optimal results.
The SMT process involves several key steps:
- Solder Paste Printing: A stencil printer applies solder paste to the PCB pads where components will be placed.
- Component Placement: Pick and place machines accurately place SMT components onto the solder paste.
- Reflow Soldering: The PCB passes through a reflow oven, where the solder paste melts and forms a strong bond between the components and the PCB.
- Inspection: Automated Optical Inspection (AOI) systems check for defects such as missing components, misalignments, and poor solder joints.
- Testing: Functional testing ensures that the assembled PCB meets the required specifications.
SMT production process is highly automated, which helps to reduce labor cost and improve production efficiency. Using SMT also allows for the use of smaller components, resulting in smaller and more compact electronic products. PCB assembly process is also faster and more efficient than through-hole assembly technology. Process in the SMT is much more reliable.
H2: What are the Main Equipment in an SMT Line?
An SMT line is composed of several specialized machines, each designed for a specific task in the assembly process. Understanding the function of each machine is essential for optimizing the SMT production line. The main equipment in an SMT line typically includes:
- Stencil Printer: Applies solder paste onto the PCB using an SMT stencil. The stencil ensures that the solder paste is applied only to the areas where components will be placed.
- Pick-and-Place Machine: These machines, often called place machines, precisely place SMT components onto the PCB. They use vacuum nozzles to pick up components from feeders and place them onto the solder paste on the PCB.
- Reflow Oven: This oven heats the PCB to melt the solder paste, creating a strong bond between the components and the PCB pads. The reflow soldering process is carefully controlled to ensure that the components are not damaged by excessive heat.
- Conveyor System: Transports PCBs between machines. They are essential for maintaining a smooth and continuous flow of PCBs through the assembly line.
- Inspection Systems: AOI (Automatic Optical Inspection) systems inspect the assembled PCBs for defects. They use cameras and image processing software to detect issues like missing components, incorrect component placement, and poor solder joints.
The equipment in an SMT line is designed to work together seamlessly, ensuring a smooth and efficient assembly process. Automatic SMT lines can achieve very high-volume production with minimal human intervention. Machines are used to place components like resistors, capacitors, and integrated circuits onto printed circuit boards. PCB production line provides a fast and efficient way to assemble electronic circuit boards. SMT line includes a variety of equipment, such as stencil printer, pick-and-place machines, reflow oven, and inspection systems.
H2: What Role Does a Stencil Printer Play in SMT Assembly?
The stencil printer is the first crucial piece of equipment in the SMT assembly line. It applies solder paste onto the PCB with precision, using a stainless steel stencil that has apertures corresponding to the component pads on the PCB. The accuracy of solder paste deposition is critical for ensuring good solder joints during the reflow soldering process. Modern stencil printers offer advanced features like automatic stencil alignment, solder paste height inspection, and stencil cleaning, ensuring consistent and high-quality solder paste application.
Solder paste printing is a critical step in the SMT process, and the stencil printer plays a vital role in ensuring its accuracy. The stencil printer uses a metal stencil to apply solder paste to the PCB. The stencil has openings that correspond to the locations where components will be placed on the PCB. The stencil printer aligns the stencil with the PCB and then uses a squeegee to push the solder paste through the openings and onto the PCB. The accuracy of the stencil printer is critical for ensuring that the correct amount of solder paste is applied to each pad. If too much solder paste is applied, it can cause bridging between adjacent pads during the reflow soldering process. If too little solder paste is applied, it can result in weak or incomplete solder joints.
H2: How Do Pick and Place Machines Work in an SMT Line?
Pick and place machines are the workhorses of the SMT assembly line. They are responsible for accurately placing SMT components, such as resistors, capacitors, and integrated circuits, onto the PCB. These machines use vacuum nozzles to pick up components from feeders and place them onto the solder paste on the PCB. Modern pick and place machines are incredibly fast and accurate, capable of placing tens of thousands of components per hour with high precision. They often feature multiple placement heads, advanced vision systems for component alignment, and sophisticated software for optimizing placement sequences.
Pick-and-place machines are a critical part of any SMT assembly line. Pick-and-place machines are used to place components onto the PCB with high speed and accuracy. They use a variety of methods to pick up components, including vacuum nozzles and mechanical grippers. Once a component is picked up, the machine uses a vision system to determine its orientation and then places it onto the PCB at the correct location. The speed and accuracy of the pick-and-place machine are critical for achieving high-volume production and minimizing defects.
H2: What is the Importance of the Reflow Oven in SMT?
The reflow oven is a critical component of the SMT assembly line. It’s responsible for the reflow soldering process, which creates the electrical and mechanical connections between the SMT components and the PCB. The reflow oven heats the PCB assembly to a precise temperature profile, melting the solder paste and forming solder joints. The temperature profile is carefully controlled to ensure that the components and the PCB are not damaged by excessive heat while ensuring that all solder joints are properly formed.
The reflow soldering process is a critical step in SMT assembly, and the reflow oven plays a vital role in ensuring its success. The reflow oven heats the PCB to a temperature that melts the solder paste but does not damage the components or the PCB. The soldering process typically involves several stages, including preheating, soaking, reflow, and cooling. Each stage is carefully controlled to ensure that the solder joints are strong and reliable. The reflow oven must be able to maintain a consistent temperature throughout the soldering process to ensure that all of the solder joints are properly formed. Proper reflow soldering is crucial for creating reliable solder joints and ensuring the long-term performance of the electronic product.
H2: Why is Inspection Crucial in SMT Production?
Inspection is a vital part of the SMT production process. It ensures that each PCB meets the required quality standards and that there are no defects that could affect the performance or reliability of the final product. AOI (Automatic Optical Inspection) systems are commonly used to inspect PCBs after reflow soldering. These systems use high-resolution cameras and sophisticated image processing algorithms to detect defects such as missing or misplaced components, incorrect component orientation, solder bridging, and insufficient solder. Early detection of defects allows for rework and prevents faulty PCBs from proceeding to the next stage of production, saving time and resources.
Inspection plays a critical role in ensuring the quality of PCB assembly lines. Inspection is used to detect defects in the assembly process and to ensure that the finished product meets the required specifications. AOI systems are commonly used to inspect PCBs after the reflow soldering process. These systems use cameras to capture images of the PCB and then use image processing software to identify defects such as missing components, misaligned components, and poor solder joints. AOI is an essential tool for ensuring the quality of printed circuit board assembly.
H2: How Does Our Depaneling Equipment Enhance SMT Lines?
As a leading manufacturer of PCB depaneling equipment, we understand the critical role that efficient and precise depaneling plays in the overall SMT manufacturing process. Our PCB Router Machines and PCB Laser Depaneling systems are designed to seamlessly integrate into SMT lines, providing automated, high-precision separation of individual PCBs from panels after assembly. Our V-Groove Depaneling equipment offers a reliable solution for panels with pre-scored V-grooves, ensuring clean and stress-free separation. These machines are loved by industry giants like TP-LINK, Canon, and Foxconn for their reliability, precision, and contribution to increased throughput and reduced labor costs.
In my 20 years in the industry, I’ve seen firsthand how crucial efficient depaneling is to maintaining a smooth SMT workflow. A case study with BYD demonstrated that integrating our laser depaneling system resulted in a 25% increase in their SMT line’s overall efficiency by minimizing PCB handling and reducing the risk of damage during separation. Additionally, our PCB/FPC Punching Machines provide another efficient method for separating PCBs, especially for irregular shapes. Our commitment to innovation and quality has made us a trusted partner for Fortune 500 companies worldwide, consistently delivering solutions that enhance their production capabilities.
H2: What are the Future Trends in SMT Manufacturing?
The SMT industry is continuously evolving, driven by the demand for smaller, faster, and more powerful electronic devices. One major trend is the increasing use of automation and robotics in SMT lines. This includes the integration of collaborative robots (cobots) that can work alongside human operators, increasing flexibility and efficiency. Another trend is the rise of Industry 4.0 and the implementation of smart factories, where SMT equipment is connected through the Internet of Things (IoT), enabling real-time data analysis, predictive maintenance, and remote monitoring. These advancements are aimed at further optimizing production efficiency, improving quality control, and reducing manufacturing costs.
The future of SMT manufacturing is bright, with ongoing advancements in automation, miniaturization, and inspection technologies. The use of artificial intelligence (AI) and machine learning (ML) in SMT equipment is also on the rise. AI and ML algorithms can be used to optimize pick-and-place programs, improve inspection accuracy, and even predict equipment failures before they occur. These technologies will further enhance the efficiency and reliability of SMT assembly lines, enabling manufacturers to meet the growing demand for complex electronic products. The trend toward smaller and more powerful electronic devices is driving the need for more advanced SMT equipment and processes. For example, the increasing use of micro-BGAs and other fine-pitch components requires more precise pick-and-place machines and more sophisticated inspection systems.
FAQs
- What does SMT stand for in electronics manufacturing? SMT stands for Surface Mount Technology. It’s a method of assembling printed circuit boards (PCBs) where components are mounted directly onto the surface of the board, rather than using through-hole technology.
- What are the key advantages of using an SMT assembly line? SMT assembly lines offer several advantages, including increased automation, higher component density, faster assembly speeds, improved high-frequency performance, and reduced manufacturing costs, particularly for high-volume production.
- What is the role of a reflow oven in the SMT process? The reflow oven is responsible for the reflow soldering process, which creates the electrical and mechanical connections between the SMT components and the PCB. It heats the PCB assembly to a precise temperature profile, melting the solder paste and forming solder joints.
- Why is solder paste printing important in SMT assembly? Solder paste printing is a critical step because it ensures that the correct amount of solder paste is applied to the PCB pads where components will be placed. Accurate solder paste deposition is essential for forming strong and reliable solder joints during reflow soldering.
- What types of inspection systems are used in SMT lines? AOI (Automatic Optical Inspection) systems are commonly used in SMT lines. They use cameras and image processing software to inspect assembled PCBs for defects such as missing or misaligned components, solder bridging, and insufficient solder.
Conclusion
- SMT (Surface Mount Technology) is a crucial technology for modern electronics manufacturing, enabling the production of smaller, more powerful devices.
- SMT assembly lines are highly automated production lines that streamline the PCB assembly process, from solder paste application to component placement, reflow soldering, and inspection.
- Key equipment in an SMT line includes stencil printers, pick and place machines, reflow ovens, conveyors, and inspection systems.
- Our depaneling equipment, including router machines, laser depaneling systems, and V-groove depaneling machines, seamlessly integrates into SMT lines, enhancing efficiency and PCB quality.
- The future of SMT manufacturing involves increased automation, the use of AI and ML, and the implementation of smart factory concepts.
- Choosing the right equipment and optimizing the SMT manufacturing process are essential for achieving efficient, high-quality mass production of electronic products.
- Partnering with an experienced PCB equipment manufacturer like us can help you achieve your production goals and stay ahead in the competitive electronics industry.
Ready to optimize your SMT production line with our cutting-edge depaneling solutions? Contact us today to learn more about our Automatic Equipment, and SMT whole line equipment. Let’s discuss how we can help you achieve greater efficiency, quality, and innovation in your electronics manufacturing processes. We are committed to providing the best solutions for your production needs, ensuring less cost and higher production capabilities.