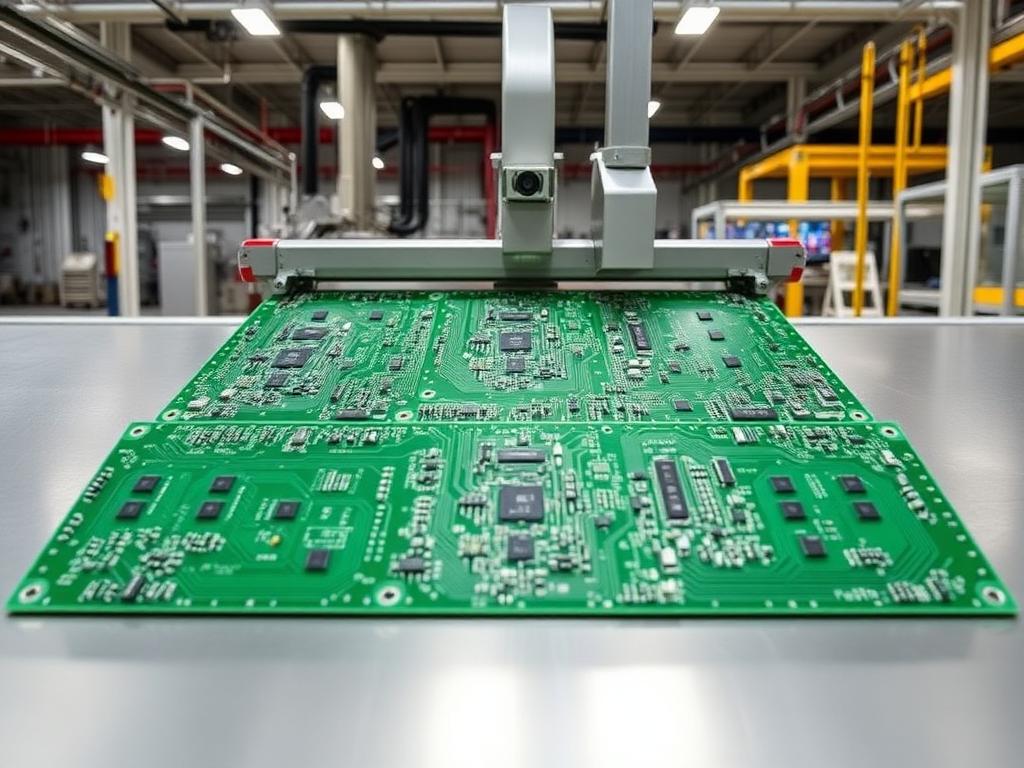
SMT pick and place machine
Top 10 SMT Pick and Place Machines for High-Speed PCB Assembly
This article dives into the world of SMT (Surface Mount Technology) pick and place machines, essential tools for modern electronics manufacturing. I’ll share insights from my 20 years in the PCB (Printed Circuit Board) industry, focusing on how these machines streamline production, enhance efficiency, and ultimately impact the quality of electronic products. As a leading manufacturer of PCB depaneling solutions, including PCB Router Machines, V-Groove Depaneling, and PCB Laser Depaneling, I’ve seen firsthand how crucial the right equipment is for success. We’ll explore the top 10 SMT assembly machines, helping you understand why this article is a must-read for anyone involved in electronics manufacturing.
Understanding the Basics: What is an SMT Pick and Place Machine?
SMT pick and place machines are the workhorses of modern electronics assembly. They automate the process of placing electronic components onto a printed circuit board (PCB) with incredible speed and precision. In the past, this was a painstaking manual task. Today, with the advent of SMT, we can achieve levels of productivity that were once unimaginable.
- How do they work? Essentially, a pick and place machine uses a robotic arm equipped with vacuum nozzles to pick up electronic components from feeders, then precisely place them onto the PCB. These components, also known as surface mount devices (SMDs), are then soldered onto the board to create the final circuit.
- Why are they important? The accuracy and speed of these machines directly influence the quality and production capacity of any electronics manufacturing operation. A high-quality SMT pick and place machine ensures minimal errors, reduced waste, and faster turnaround times, leading to cost savings and a competitive edge. In my experience, investing in a reliable machine is one of the most critical decisions a company can make.
Why is SMT Assembly So Important in Modern Electronics Manufacturing?
Surface mount technology (SMT) has revolutionized the electronics industry. The transition from through-hole technology to SMT marked a major leap forward in miniaturization, automation, and overall efficiency.
- Smaller, Denser Circuits:Â SMT allows for smaller components and denser circuit board designs. This is crucial for the ever-shrinking form factors of modern electronic devices like smartphones and wearables.
- Automated Assembly:Â The SMT assembly process is highly automated, thanks to the pick and place machine. This automation significantly reduces labor costs and the risk of human error. Over the years, I’ve witnessed how automation has transformed factories, enabling them to scale production without sacrificing quality.
- Improved Performance:Â SMT components often offer better electrical performance compared to their through-hole counterparts. This is because the shorter leads in SMDs reduce inductance and capacitance, leading to improved signal integrity.
What Are the Different Types of SMT Pick and Place Machines?
SMT pick and place machines come in various configurations to suit different production needs. Understanding these types is crucial for selecting the right machine for your specific requirements.
- Manual Pick and Place Machines:Â These are the most basic and affordable option, ideal for prototyping or very low-volume production. Operators manually place components onto the PCB using tweezers or vacuum pens. While cost-effective for small runs, they are slow and prone to human error.
- Semi-Automatic Pick and Place Machines:Â These machines offer a balance between automation and manual intervention. They typically use a vision system to assist the operator in aligning the components, but the placement is still done manually.
- Automatic Pick and Place Machines: These are fully automated systems capable of handling high-volume production. They feature multiple feeders, advanced vision systems, and sophisticated software for precise and rapid component placement. In high-volume settings, I’ve seen how automatic machines like the GAM 330AT In-Line Automatic PCB Router Machine are indispensable.
How Do You Choose the Best SMT Pick and Place Machine?
Selecting the best SMT assembly machine is a critical decision that depends on several factors. These include production volume, component types, budget, and available space.
- Production Volume:Â For low-volume or prototype runs, a manual or semi-automatic machine might suffice. However, for high-volume production, a fully automatic machine is essential.
- Component Types:Â Consider the size and variety of components you’ll be placing. Some machines are better suited for handling very small or irregularly shaped components.
- Placement Speed:Â Measured in components per hour (CPH), this determines how quickly the machine can populate a PCB. High-speed machines are crucial for mass production.
- Accuracy:Â The precision with which the machine places components is paramount. Look for machines with advanced vision systems and high repeatability.
- Feeder Capacity:Â The number of feeders determines how many different types of components the machine can handle simultaneously. A higher feeder capacity allows for greater flexibility.
- Budget:Â Machines range in price from a few thousand dollars for manual models to hundreds of thousands for high-end automated systems.
- Support and Service:Â Choose a reputable manufacturer that offers reliable after-sales support and training.
What are the Top 10 SMT Assembly Machines?
The market is filled with various manufacturers claiming to offer the best SMT machine. In my experience, the following are some of the most reputable brands:
Brand | Strengths |
---|---|
Yamaha | Known for high-speed, high-precision machines, excellent reliability. |
Juki | Offers a wide range of machines, from entry-level to high-end, with good software support. |
Fuji | Renowned for their robust and durable machines, often used in high-volume, demanding environments. |
Panasonic | Offers advanced features like 3D vision and on-the-fly component recognition. |
ASM (ASMPT) | A leading provider of high-performance SMT solutions, known for their innovative technologies. |
Hanwha Techwin | Offers a good balance of performance and cost, with user-friendly interfaces. |
Europlacer | Known for their flexible and adaptable machines, suitable for high-mix, low-volume production. |
Mycronic | Specializes in high-mix, high-flexibility production, with advanced software and automation capabilities. |
NEODEN | Offers affordable, entry-level machines for prototyping and low-volume production. |
DDM Novastar | Provides a range of benchtop and standalone machines, known for their ease of use and compact design. |
What is the Role of Feeders in SMT Assembly?
Feeders are a critical part of the SMT assembly process. They are responsible for holding and dispensing the electronic components that the pick and place machine picks up and places onto the PCB.
- Types of Feeders:Â There are several types of feeders, including tape and reel feeders, tray feeders, tube feeders, and stick feeders. The choice of feeder depends on the type and packaging of the components being used.
- Feeder Capacity:Â The number of feeders a machine can accommodate directly impacts its flexibility and the complexity of the boards it can assemble. Machines with high feeder capacity can handle a wider range of components and more complex designs.
- Feeder Intelligence:Â Modern feeders are becoming increasingly intelligent, with features like automatic component recognition and error detection. This helps to improve the accuracy and reliability of the assembly process.
How Does Solder Paste Application Work in SMT?
Before the pick and place machine can do its job, solder paste must be applied to the PCB. This is typically done using a solder paste screen printer. The solder paste acts as a temporary adhesive to hold the components in place until they are permanently soldered to the board.
- Stencil Printing:Â A stencil, a thin sheet of metal with cutouts corresponding to the component pads on the PCB, is placed over the board. Solder paste is then squeegeed across the stencil, filling the cutouts.
- Solder Paste Inspection:Â After printing, the solder paste is often inspected using automated optical inspection (AOI) or solder paste inspection (SPI) equipment to ensure that it has been applied correctly.
What Happens After Component Placement?
After the components have been placed onto the PCB by the pick and place machine, the board moves on to the next stage of the assembly process: reflow soldering.
- Reflow Soldering:Â The PCB is passed through a reflow oven, where it is heated in a controlled manner. This melts the solder paste, forming a permanent bond between the components and the board.
- Cooling and Inspection: After reflow, the board is cooled, and the solder joints are inspected for quality. This can be done manually or using automated inspection equipment like AOI or X-ray inspection. This is a step that cannot be ignored in the electronics assembly process. We have ZM500 Automatic Stencil Inspection Machine to help you improve production efficiency.
What are the Future Trends in SMT Assembly?
The SMT industry is constantly evolving, driven by the demand for smaller, faster, and more powerful electronic devices. Some of the key trends include:
- Increased Automation: We are seeing a move towards even greater levels of automation, with the use of robots and artificial intelligence (AI) to optimize the assembly process. This includes Automatic Equipment to complete the automated process.
- Miniaturization:Â Components continue to shrink, requiring ever-more precise placement and soldering techniques.
- 3D Packaging:Â The use of 3D packaging technologies, where multiple chips are stacked vertically, is becoming more common. This poses new challenges for SMT assembly.
- Industry 4.0 Integration:Â SMT equipment is becoming increasingly integrated into smart factory environments, allowing for real-time data analysis and process optimization.
FAQs
What is the difference between SMT and through-hole technology?
SMT involves mounting components directly onto the surface of the PCB, while through-hole technology requires components to be inserted into holes drilled through the board. SMT allows for smaller components, denser designs, and greater automation.
What is the typical placement speed of an SMT pick and place machine?
Placement speed varies widely depending on the machine. Entry-level machines might place a few thousand components per hour, while high-end machines can place tens or even hundreds of thousands of components per hour.
How accurate are SMT pick and place machines?
Modern SMT pick and place machines are highly accurate, with placement accuracy typically in the range of a few tens of micrometers.
What kind of maintenance do SMT pick and place machines require?
Regular maintenance typically includes cleaning, lubrication, and calibration. The frequency of maintenance depends on the machine and its usage.
Can SMT pick and place machines handle different types of components?
Yes, most SMT pick and place machines are designed to handle a wide range of components, from small passive components like resistors and capacitors to large integrated circuits.
Conclusion
- SMT pick and place machines are essential for modern electronics manufacturing.
- Choosing the right machine depends on factors like production volume, component types, and budget.
- Top manufacturers include Yamaha, Juki, Fuji, Panasonic, and ASM.
- Feeders play a crucial role in dispensing components to the pick and place machine.
- Solder paste application and reflow soldering are critical steps in the SMT assembly process.
- Future trends include increased automation, miniaturization, and Industry 4.0 integration.
As someone who has dedicated their career to advancing PCB manufacturing, I understand the critical role that the right equipment plays in achieving success. Whether you’re an established electronics manufacturer or a newcomer to the field, investing in high-quality SMT pick and place machines, along with other essential tools like our PCB/FPC Punching Machine, is a decision that will pay dividends for years to come. If you want to learn more about the SMT process or explore our range of PCB depaneling solutions, don’t hesitate to contact us. I’m always excited to share my knowledge and help companies achieve their manufacturing goals. Remember, the future of electronics is being built right now, and it’s being built with SMT.