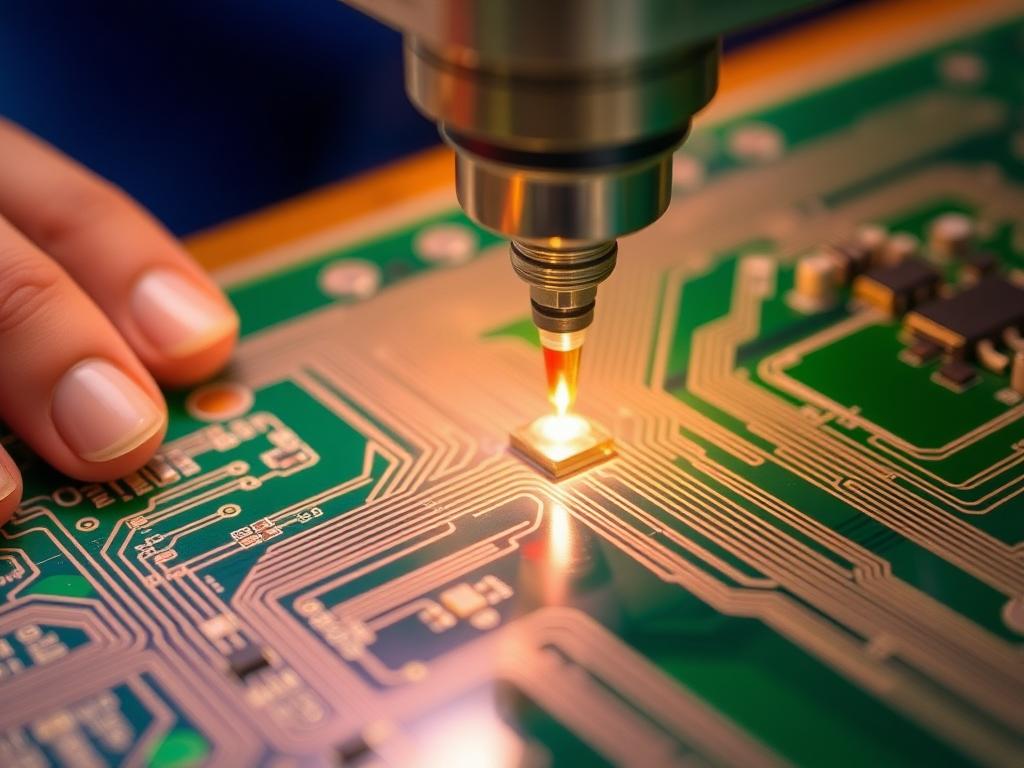
pcb v-groove solutions
Mastering PCB V-Scoring: Revolutionizing PCB Design and Cutting Machine Workflow
The landscape of PCB (printed circuit board) manufacturing is constantly evolving. As technology advances, the demand for smaller, more efficient, and cost-effective electronic devices has never been higher. A critical step in this process is the separation of individual PCBs from a larger panel, and v-scoring (also known as v-grooving) has emerged as a game-changer. This article delves into the intricacies of PCB v-scoring, exploring its advantages, implementation, and the future of PCB separation methods. Whether you’re an engineer at a large electronics company, part of an electronic product processing factory, or an individual PCB enthusiast, understanding the nuances of v-scoring is crucial for optimizing your PCB layout and manufacturing workflow. This read will equip you with the knowledge to make informed decisions about your PCB fabrication process, ultimately leading to improved product quality and reduced production costs.
What is PCB V-Scoring and How Does it Work?
PCB v-scoring is a widely used technique for separating individual PCBs from a larger panel after the assembly process. It involves creating v-shaped grooves on both sides of the PCB panel along predetermined lines. These grooves, or v-grooves, weaken the PCB material, making it easy to break apart the individual circuit boards later.
The v-scoring process is typically performed using a specialized scoring machine equipped with a v-shaped cutting tool. The machine precisely cuts the grooves to a specific depth, usually leaving about one-third of the board thickness intact. The depth of the v-groove is crucial for ensuring a clean break without damaging the PCBs.
The v-scoring process typically involves the following steps:
- Design: Engineers create PCB layout with v-scoring in mind, ensuring proper spacing between individual boards and defining the v-groove paths in the Gerber files.
- Scoring: The PCB panel is fed into the scoring machine, which accurately cuts the v-grooves on both sides of the board along the predetermined lines.
- Assembly: SMD components and other parts are placed onto the PCB panel according to the design.
- Depaneling: After PCB assembly, the individual PCBs are separated from the panel by applying a controlled force along the v-grooves.
Why is V-Scoring the Preferred Choice for High-Volume PCB Production?
V-scoring has become the preferred choice for high-volume PCB production due to its numerous advantages:
- Cost-effectiveness: V-scoring significantly reduces the labor required for separating PCBs, leading to substantial cost savings.
- Increased efficiency: Automated scoring machines can process large panels quickly, maximizing manufacturing efficiency.
- Precision: V-scoring offers high precision cutting, ensuring clean breaks and minimizing damage to the circuit boards.
- Versatility: V-scoring can be used with a wide range of PCB materials, including FR-4 and FR-1 boards.
- Improved structural integrity: V-scoring makes it easier to separate the PCBs without putting stress on the board’s components.
V-scoring is primarily used in mass production because it is a cost-effective manufacturing method to create multiple printed circuit boards on a single panel.
What are the Different Types of PCB Depaneling Machines?
Several types of PCB depaneling machines are available, each with its own strengths and weaknesses. The most common types include:
- PCB Router Machine: These machines use a rotating cutting tool to mill away the material between PCBs. They offer high flexibility and can handle complex shapes but may produce more dust and noise. One of our most popular models is the GAM 380AT PCB Bottom Depaneling Machine.
- V-Groove Depaneling Machine: These machines use v-shaped blades to create the v-grooves and then apply pressure to break apart the PCBs. V-groove depaneling is cost-effective and efficient for simple, straight-line separations. Check out our ZM30-ASV Fully Automatic saw-type V-groove PCB depaneling machine, ideal for straight-line separations.
- PCB/FPC Punching Machine: These machines use a die to punch out individual PCBs from the panel. They are suitable for high-volume production of small, simple-shaped PCBs. The ZM10T & 15T PCB & FPC Punching Cutting Machine is a great example of a powerful punching machine.
- Laser Cutting Machine: PCB laser depaneling machines use a laser beam to cut the PCB material. They offer high precision and can handle complex shapes, but they are typically more expensive than other options. We at PCB Depaneling also offer advanced laser cutting solutions, like the DirectLaser H3 Laser Online Machine.
How Does V-Scoring Impact PCB Design and Layout?
V-scoring has a significant impact on PCB design and layout. Designers must consider the following rules when designing PCB boards with components for v-scoring:
- Component placement: Components need to be placed at a certain distance from the v-groove to prevent damage during the separation process. Typically, a clearance of 0.5mm or more is recommended.
- Trace routing: Traces should also be routed away from the v-groove to avoid damage.
- Board thickness: The thickness of the PCB will determine the depth of the v-groove.
- Panelization: Proper panelization is crucial for maximizing the number of PCBs on a single panel and minimizing material waste.
V-grooves are cut into the top and bottom of the PCB with a 30°, 45°, or 60° angle. You must ensure that copper features like pads, traces, or planes should be at least 0.3mm from the v-groove on outer layers.
What are the Limitations of V-Scoring?
While v-scoring is a highly effective method, it does have some limitations:
- Shape restrictions: V-scoring is best suited for straight-line separations. It is not ideal for boards with complex shapes or curves.
- Material limitations: V-scoring may not be suitable for all PCB materials, especially very thin or brittle ones.
- Stress on components: If not performed correctly, v-scoring can put stress on nearby components during the separation process.
How to Integrate V-Scoring into Your PCB Assembly Process?
Integrating v-scoring into your PCB assembly process requires careful planning and coordination:
- Design for v-scoring: Ensure your PCB design adheres to the guidelines for component placement, trace routing, and panelization.
- Choose the right depaneling machine: Select a machine that meets your production volume, PCB material, and shape requirements.
- Optimize your workflow: Streamline your assembly process to ensure smooth transitions between scoring, assembly, and depaneling.
- Train your staff: Provide proper training to your operators on how to use the depaneling machine safely and effectively.
How Does V-Scoring Compare to Other PCB Separation Methods?
Here’s a comparison table of v-scoring with other common PCB separation methods:
Feature | V-Scoring | Routing | Punching | Laser Cutting |
Cost | Low | Medium | Low | High |
Speed | High | Medium | High | Medium |
Precision | High | High | Medium | Very High |
Shape Flexibility | Low | High | Low | High |
Material | Most PCBs | Most PCBs | Thin, simple PCBs | Most PCBs |
Dust/Noise | Low | High | Medium | Low |
Applications | High-volume, straight-line separations | Complex shapes, prototyping | High-volume, small, simple shapes | High-precision, complex shapes |
Equipment | Scoring machine or a cutting machine using nether straight blade and upper round blade. | CNC or special PCB cutting machine. | Special punching PCB cutting machine. | PCB laser depaneling machine. |
V-scoring is the preferred choice for high-volume production due to its cost-effectiveness, speed, and precision.
What is the Future of PCB Depaneling?
The future of PCB depaneling is likely to see continued advancements in automation, precision, and flexibility. Here are some trends to watch:
- Increased automation: We can expect to see more fully automated depaneling systems that integrate with other stages of the PCB assembly process. You can check our SMT In-Line Depaneling Machine Solution, which represents the future of automated depaneling systems.
- Improved precision: Advances in laser cutting and other technologies will lead to even higher precision in PCB separation.
- Greater flexibility: New depaneling methods may emerge that can handle a wider range of shapes, materials, and thicknesses.
- Integration with Industry 4.0: Depaneling systems will increasingly be connected to the Internet of Things (IoT) and integrated with data analytics platforms.
How Can Advanced PCB Depaneling Solutions Improve Your Workflow?
Investing in advanced PCB depaneling solutions, such as those offered by PCB Depaneling, can significantly improve your workflow in several ways:
- Enhanced productivity: Automated depaneling machines can process PCBs much faster than manual methods, increasing your overall production output.
- Reduced costs: By automating the depaneling process, you can reduce labor costs and material waste, leading to significant cost savings.
- Improved quality: Precision depaneling minimizes the risk of damage to PCBs and components, resulting in higher product quality and reliability.
- Increased flexibility: Advanced depaneling machines can handle a wider range of PCB designs and materials, giving you greater flexibility in your manufacturing process.
What are the Key Considerations for Choosing a PCB Depaneling Machine Manufacturer?
When selecting a PCB depaneling machine manufacturer, it’s essential to consider the following factors:
- Experience and reputation: Choose a manufacturer with a proven track record of producing high-quality, reliable machines.
- Product range: Ensure the manufacturer offers a range of machines that meet your specific needs in terms of production volume, PCB type, and shape requirements.
- Technology and innovation: Look for a manufacturer that invests in research and development to offer cutting-edge depaneling solutions.
- Customer support: Choose a manufacturer that provides excellent customer support, including installation, training, and maintenance services.
- Global presence: If you operate internationally, consider a manufacturer with a global presence and support network.
FAQs
- What is the typical depth of a v-groove?
The typical depth of a v-groove is about one-third of the PCB thickness. - What is the minimum distance between a component and a v-groove?
The minimum distance between a component and a v-groove is typically 0.5mm or more. - Can v-scoring be used for multilayer PCBs?
Yes, v-scoring can be used for multilayer PCBs. - What are the advantages of laser cutting over v-scoring?
Laser cutting offers higher precision and can handle more complex shapes than v-scoring. - What kind of maintenance do depaneling machines require?
Depaneling machines require regular cleaning and occasional blade or cutting tool replacement. - How does v-scoring affect the electrical performance of a PCB?
When done correctly, v-scoring does not negatively affect the electrical performance of a PCB.
Conclusion
PCB v-scoring is a critical process in modern PCB manufacturing. Understanding its principles, advantages, and limitations is essential for optimizing your PCB design, layout, and assembly workflow. By carefully considering the factors discussed in this article and choosing the right depaneling equipment and manufacturer, you can achieve significant improvements in productivity, quality, and cost-effectiveness.
Key takeaways:
- V-scoring is a cost-effective and efficient method for separating PCBs in high-volume production.
- PCB designers must consider v-scoring requirements during the layout phase.
- Different types of depaneling machines are available, each with its own strengths and weaknesses.
- Advanced depaneling solutions can significantly improve your workflow and reduce costs.
- Choosing the right depaneling machine manufacturer is crucial for success.
- Our company is trusted by industry giants like TP-LINK, Canon, BYD, Flex, TCL, Xiaomi, Lenovo, OPPO, HONOR, and Foxconn.
By partnering with a leading manufacturer like PCB Depaneling, you can leverage our expertise and cutting-edge technology to streamline your PCB manufacturing process and achieve your business goals. Our commitment to quality, innovation, and customer satisfaction has made us the preferred choice for Fortune 500 companies and PCB manufacturers worldwide. Contact us today to learn more about how our solutions can benefit your business.