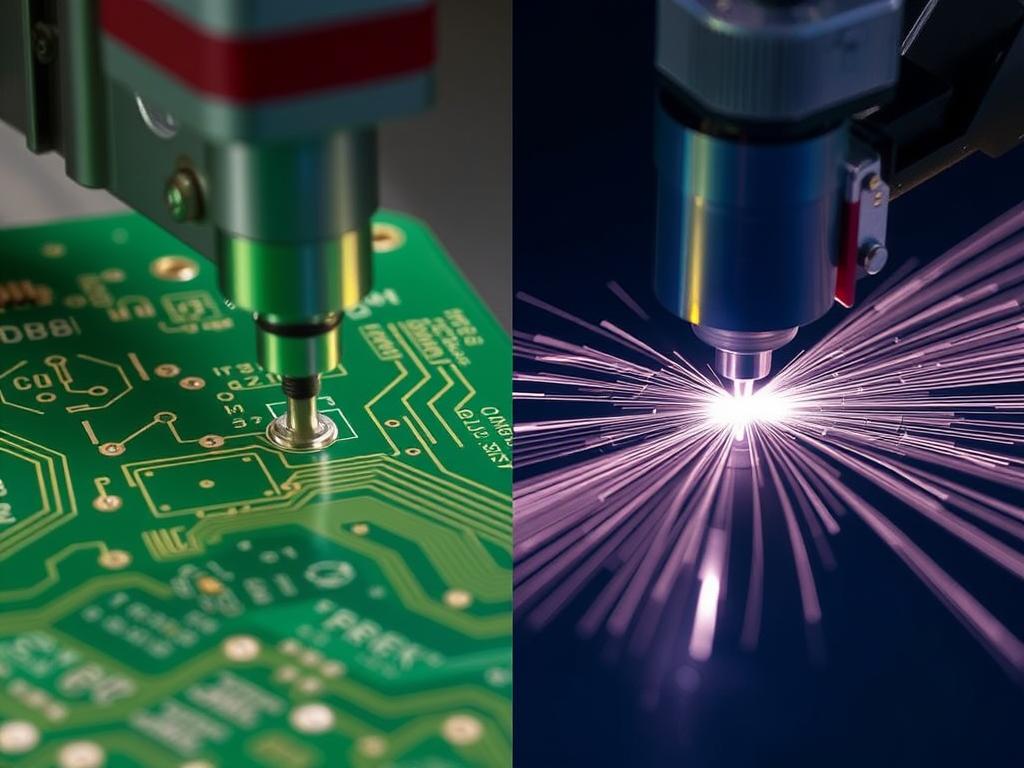
PCB punching vs. laser cutting
Leading PCB V Groove Cutting Machines: Precision, Speed, and Reliability
In the fast-paced world of electronic manufacturing, the efficiency and precision of your PCB depaneling process can make all the difference. This article explores the cutting-edge PCB V Groove Cutting Machines that are transforming the industry. Whether you’re a large electronics factory or an individual PCB enthusiast, discover why our solutions are trusted by Fortune 500 giants like TP-LINK, Canon, and Xiaomi.
What is V-Groove Depaneling and Why It Matters?
V-Groove Depaneling is a specialized process in PCB manufacturing where boards are separated from a larger panel using a V-shaped groove. This method ensures clean and precise cuts, minimizing the risk of damage to delicate circuits.
Why It Matters:
- Precision:Â Achieves accurate cuts, reducing defects.
- Efficiency:Â Speeds up the depaneling process, saving time.
- Cost-Effective:Â Lowers production costs by minimizing material waste.
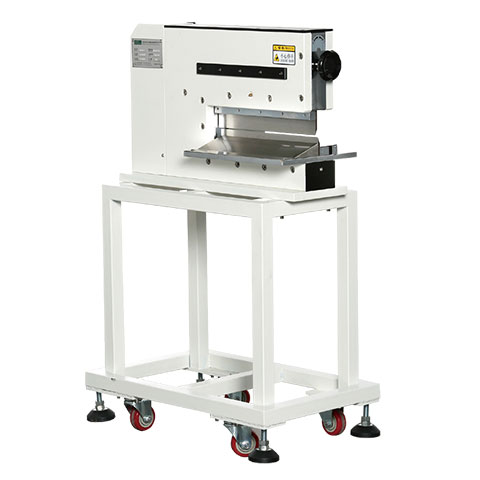
How Does a PCB V Groove Cutting Machine Work?
A PCB V Groove Cutting Machine utilizes a V-shaped blade to create grooves on the PCB panel. These grooves guide the separation process, ensuring each board is cut cleanly and accurately.
Key Components:
- Blade:Â Often made of high-speed steel or carbide for durability.
- Controller:Â Automates the cutting process for consistency.
- Feed System:Â Ensures the PCB panel is accurately positioned during cutting.
Step-by-Step Process:
- Loading:Â The PCB panel is placed on the machine’s bed.
- Grooving:Â The V-shaped blade engraves grooves along the board’s edges.
- Separation:Â The panel is split along the grooves, separating individual boards.
Benefits of Using Automatic PCB Cutting Machines
Automating the PCB cutting process offers numerous advantages over manual methods.
Advantages:
- Increased Speed:Â Automates repetitive tasks, boosting production rates.
- Enhanced Accuracy:Â Reduces human error, ensuring consistent quality.
- Labor Savings:Â Minimizes the need for manual labor, cutting operational costs.
Table: Manual vs. Automatic PCB Cutting
Feature | Manual Cutting | Automatic Cutting |
---|---|---|
Speed | Slow | Fast |
Accuracy | Variable | High |
Labor Cost | High | Low |
Consistency | Inconsistent | Consistent |
Material Waste | Higher | Lower |
Key Features to Look for in a PCB Groove Cutter
When selecting a PCB Groove Cutter, consider the following features to ensure it meets your manufacturing needs.
Essential Features:
- Precision Cutting:Â Ensures clean and accurate grooves.
- Adjustable Settings:Â Allows customization for different PCB sizes.
- Durable Materials:Â High-quality blades and components for longevity.
- User-Friendly Interface:Â Simplifies operation and minimizes training time.
Additional Features:
- Automatic Loading and Unloading:Â Streamlines the production process.
- Integrated Inspection Systems:Â Detects defects in real-time.
- Energy Efficiency:Â Reduces operational costs through efficient power usage.
Comparing V-Groove Cutters with Other PCB Depaneling Methods
Different depaneling methods offer varying levels of precision, speed, and cost. Here’s how V-Groove Cutters stack up against other techniques.
Laser Depaneling
- Precision:Â Higher than V-Groove.
- Speed:Â Comparable.
- Cost:Â More expensive equipment and maintenance.
Punching Depaneling
- Precision:Â Lower than V-Groove.
- Speed:Â Faster for high-volume production.
- Cost:Â Lower initial investment.
V-Groove Depaneling
- Precision:Â High, with minimal board damage.
- Speed:Â Efficient for medium to large batches.
- Cost:Â Balanced investment with lower maintenance.
Chart: Depaneling Methods Comparison
Method | Precision | Speed | Cost |
---|---|---|---|
V-Groove | High | High | Medium |
Laser | Very High | High | High |
Punching | Medium | Very High | Low |
How to Choose the Right PCB Cutting Machine for Your Manufacturing Plant
Selecting the appropriate PCB Cutting Machine depends on various factors tailored to your specific needs.
Considerations:
- Production Volume:Â High-volume factories may benefit from fully automatic machines.
- PCB Complexity:Â Complex boards require precise cutting capabilities.
- Budget:Â Balance between initial investment and long-term operational costs.
- Space Constraints:Â Ensure the machine fits within your manufacturing floor.
Checklist:
- Â Assess production requirements.
- Â Evaluate machine specifications.
- Â Consider after-sales support and maintenance.
- Â Review customer testimonials and case studies.
For a range of options, explore our PCB Router Machine offerings.
Case Studies: Success Stories with Leading Electronics Companies
Our PCB Depaneling Machines have been instrumental in enhancing production efficiency for top-tier companies.
TP-LINK
Challenge: High precision required for complex networking devices.
Solution: Implemented our GAM 380AT Automatic PCB Bottom Depaneling Machine.
Result: Achieved a 30% increase in production speed with zero defects.
Foxconn
Challenge: Large-scale production with diverse PCB designs.
Solution: Deployed our ZM30-ASV Saw-Type V-Groove PCB Depaneling Machine.
Result: Streamlined operations, reducing material waste by 25%.
Quote from TP-LINK:
“The precision and reliability of your depaneling machines have significantly boosted our manufacturing efficiency.”
— Manufacturing Director, TP-LINK
Maintenance and Best Practices for PCB Cutting Machines
Proper maintenance ensures the longevity and optimal performance of your PCB Cutting Machines.
Maintenance Tips:
- Regular Cleaning:Â Remove debris and residues after each use.
- Blade Inspection:Â Check for wear and replace blades as needed.
- Lubrication:Â Ensure moving parts are adequately lubricated to prevent wear.
- Software Updates:Â Keep the machine’s firmware updated for enhanced functionality.
Best Practices:
- Operator Training:Â Ensure staff are trained to handle and maintain the machines.
- Scheduled Maintenance:Â Implement routine checks to identify potential issues early.
- Use Quality Accessories:Â Utilize genuine parts and accessories to maintain machine integrity.
Future Trends in PCB Depaneling Technology
The PCB Depaneling landscape is evolving with advancements in technology, promising even greater efficiency and precision.
Emerging Trends:
- Integration with IoT:Â Machines equipped with IoT capabilities for real-time monitoring and data analytics.
- AI-Driven Automation:Â Enhanced automation with AI for predictive maintenance and quality control.
- Eco-Friendly Solutions:Â Development of sustainable depaneling methods to reduce environmental impact.
- Advanced Materials:Â Use of new materials for blades and components to extend machine life and performance.
Frequently Asked Questions
What is the main advantage of V-Groove depaneling over other methods?
V-Groove depaneling offers high precision and clean cuts, reducing the risk of damaging delicate PCB components compared to methods like punching.
How does an automatic PCB cutting machine improve production efficiency?
Automatic machines streamline the depaneling process, increase cutting speed, reduce human error, and ensure consistent quality, leading to higher overall production efficiency.
Can V-Groove cutters handle different PCB sizes and thicknesses?
Yes, most V-Groove cutters are adjustable and can be configured to handle a variety of PCB sizes and thicknesses, making them versatile for different manufacturing needs.
What maintenance is required for PCB V Groove Cutting Machines?
Regular maintenance includes cleaning the machine, inspecting and replacing blades, lubricating moving parts, and updating software to ensure optimal performance and longevity.
Are your PCB cutting machines compatible with SMT whole line equipment?
Absolutely. Our machines are designed to integrate seamlessly with SMT whole line equipment, providing a cohesive and efficient manufacturing process.
How can I get a quote for a PCB V Groove Cutting Machine?
You can request a quote by contacting us through our PCB Router Machine page or reaching out directly via our contact form.
Key Takeaways
- V-Groove Depaneling ensures precise and efficient PCB separation.
- Automatic Cutting Machines enhance production speed and accuracy.
- Key Features to consider include precision, durability, and user-friendly interfaces.
- Case Studies demonstrate significant improvements in manufacturing efficiency.
- Regular Maintenance is crucial for the longevity and performance of cutting machines.
- Future Trends point towards more integrated, intelligent, and sustainable depaneling solutions.
Embrace the future of PCB manufacturing with our leading PCB V Groove Cutting Machines. Join the ranks of industry leaders like Xiaomi and Foxconn who trust our solutions to deliver excellence every step of the way. Contact us today to upgrade your PCB production line.
For more information on our products and solutions, explore the following: