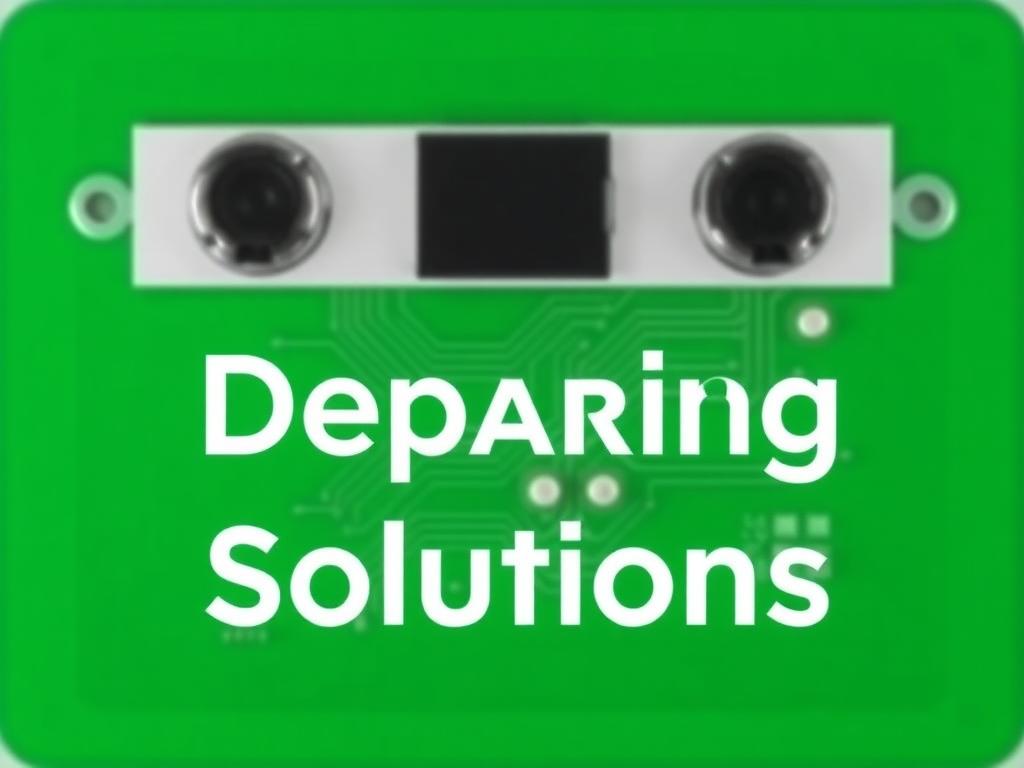
PCB Depaneling Solutions
The Ultimate Guide to PCB Laser Depaneling: Revolutionary Technology for Modern Electronics Manufacturing
Are you looking to optimize your electronics manufacturing process with cutting-edge PCB depaneling solutions? This comprehensive guide explores how laser depaneling technology is transforming the electronics industry, offering unprecedented precision and efficiency for circuit board separation. Whether you’re managing a large-scale electronics facility or running a smaller PCB assembly operation, understanding the latest developments in PCB depaneling is crucial for staying competitive in today’s market.
What is PCB Depaneling and Why Does it Matter?
PCB depaneling, or depanelization, is a critical process in electronics manufacturing where individual printed circuit boards are separated from a larger panel. This step is essential for high-volume electronics production, requiring both precision and reliability to ensure product quality.Modern manufacturing demands have made traditional depaneling methods increasingly challenging, especially with the rise of complex, densely populated circuit boards. The GAM330AD In-Line Automatic PCBA Router Machine represents the latest evolution in depaneling technology, offering superior control and efficiency.
How Does Laser Depaneling Technology Work?
Laser depaneling employs a focused laser beam to precisely separate PCBs, offering several advantages over traditional methods:
- Non-contact processing: Eliminates mechanical stress
- High precision cutting: Accuracy up to ±0.02mm
- Minimal thermal impact: Protects sensitive components
- Clean edges: No debris or burrs
The DirectLaser H1 High-Precision Laser Cutting Machine exemplifies these capabilities, delivering exceptional results for demanding applications.
What Are the Key Benefits of Laser Depaneling?
- Superior Precision
- Consistent cutting quality
- Minimal component clearance requirements
- Perfect for high-density boards
- Increased Productivity
- Higher throughput rates
- Reduced setup time
- Automated operation
- Cost Efficiency
- Lower maintenance costs
- Reduced waste
- Longer tool life
Which Industries Benefit Most from Laser Depaneling?
Laser depaneling technology provides significant advantages across various sectors:
IndustryKey BenefitsConsumer ElectronicsHigh-volume processing capabilityMedical DevicesPrecision for sensitive componentsAutomotiveReliability and consistencyAerospaceHigh-quality standards complianceTelecommunicationsFlexibility for various board types
How to Choose the Right PCB Depaneling Solution?
Consider these crucial factors when selecting a depaneling system:
- Production volume requirements
- Board complexity and component density
- Material types and thicknesses
- Integration with existing production lines
- Budget constraints
The DirectLaser H3 Laser Online Machine offers a versatile solution suitable for various production needs.
What Are the Latest Innovations in Laser Depaneling?
Recent technological advances include:
- Intelligent control systems
- Advanced beam shaping
- Multi-axis positioning
- Integrated quality control
- Industry 4.0 compatibility
How Does Laser Depaneling Compare to Traditional Methods?
When it comes to PCB depaneling, both laser depaneling and traditional methods have their own set of advantages. However, laser depaneling has emerged as a game-changing technology, offering several distinct benefits that traditional methods struggle to match. Let’s break down how laser depaneling compares to traditional methods in key areas:
1. Precision
- Laser Depaneling: Laser depaneling technology offers unparalleled precision, with cutting accuracy up to ±0.02mm. This ensures minimal risk of damaging components, which is particularly crucial for high-density and complex boards.
- Traditional Methods: Conventional depaneling methods, such as mechanical routers or saw blades, can introduce mechanical stress or vibrations that may cause misalignments or even damage to sensitive components, leading to less consistent results.
2. Speed
- Laser Depaneling: Laser systems are designed to operate at higher speeds, processing multiple PCBs in quick succession without sacrificing accuracy. Automated processes further enhance throughput, making them ideal for high-volume production environments.
- Traditional Methods: Traditional methods often involve slower, more labor-intensive processes. Mechanical routers or manual sawing can slow down the overall production rate, especially when dealing with intricate board designs that require more careful handling.
3. Setup Time
- Laser Depaneling: Laser depaneling machines are known for their quick setup times, reducing the time required to transition between different board designs. This is a major advantage for operations that handle a variety of PCB types or need to switch production lines quickly.
- Traditional Methods: Traditional methods often require more manual adjustments, such as setting up saw blades or routers, which can increase downtime and setup complexity. This can be particularly challenging when dealing with varying board sizes or materials.
4. Maintenance
- Laser Depaneling: Laser systems generally require less maintenance compared to traditional methods. Regular maintenance mainly consists of cleaning lenses and periodic calibration, which is less intensive than maintaining saw blades or routers that require frequent replacements or adjustments.
- Traditional Methods: Mechanical routers or saws require regular blade changes and more frequent mechanical maintenance. The wear and tear on these systems can result in downtime and increased operational costs.
5. Initial Cost
Traditional Methods: Traditional depaneling machines, such as routers and saws, generally have a lower upfront cost. However, the long-term operational costs may be higher due to increased maintenance, more frequent tool replacements, and the need for additional labor.
Laser Depaneling: The initial investment in laser depaneling systems tends to be higher than traditional depaneling machines due to the advanced technology involved. However, this cost is often recouped through higher efficiency, lower maintenance costs, and reduced material waste over time.
Additional Considerations:
- Non-contact Processing: One of the most significant advantages of laser depaneling is its non-contact nature, which eliminates mechanical stress and minimizes the risk of damaging sensitive components on the PCB. In contrast, traditional methods involve physical contact, which can lead to unwanted mechanical stress and potential board damage.
- Thermal Impact: Laser depaneling minimizes thermal impact on the PCB and components, ensuring that heat-sensitive parts are not damaged during the cutting process. Traditional methods, depending on the technology used, may have higher thermal effects that could potentially harm delicate components.
- Environmental Impact: Laser depaneling is generally considered more environmentally friendly due to its precision, which reduces waste, and its non-contact process, which eliminates the need for additional cutting fluids or lubricants that traditional methods often require.
Frequently Asked Questions
What is the typical ROI for a laser depaneling system?
Most companies see returns within 12-18 months through increased efficiency and reduced waste.
Can laser depaneling handle flexible PCBs?
Yes, laser systems are particularly well-suited for flexible PCBs due to their non-contact nature.
What maintenance is required for laser depaneling systems?
Regular lens cleaning and occasional calibration are the main maintenance requirements.
Is laser depaneling suitable for high-volume production?
Absolutely, especially with systems like the SMT In-Line Depaneling Machine Solution.
Key Takeaways
• Laser depaneling offers superior precision and reliability • Non-contact processing eliminates mechanical stress • Suitable for both high-volume and specialized production • Reduces operational costs long-term • Supports Industry 4.0 integration • Environmentally friendly operation Contact our experts to discuss your specific PCB depaneling needs and discover how our cutting-edge solutions can optimize your manufacturing process.