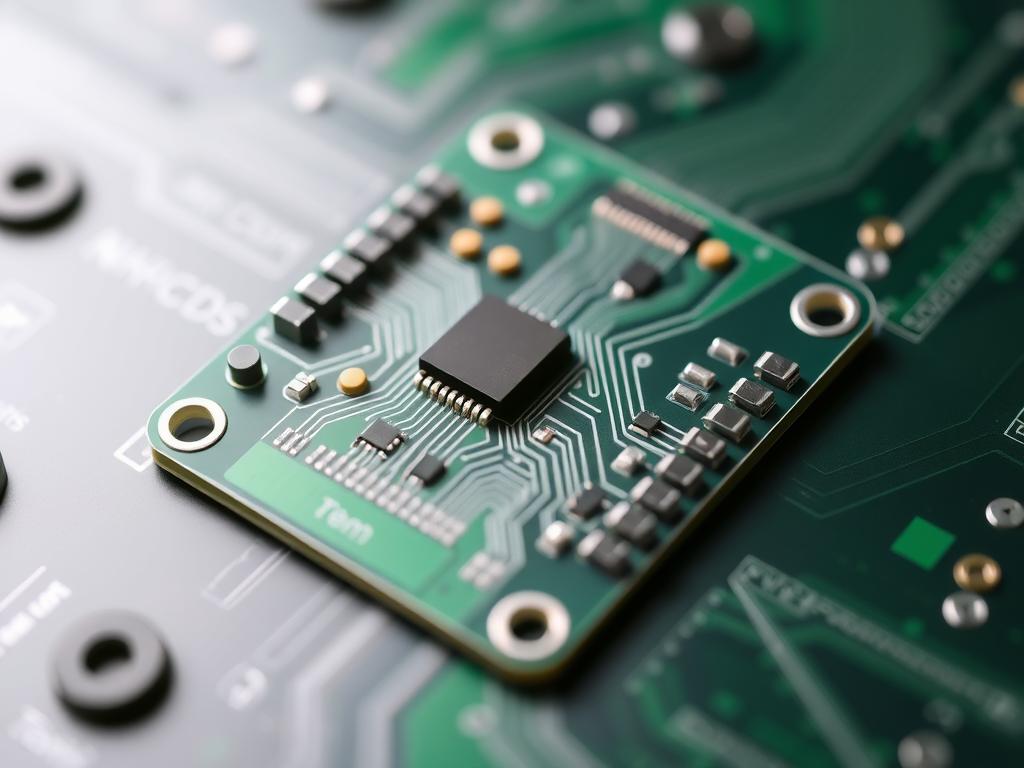
PCB depaneling for wearable technology
PCB Depaneling: Choosing the Right Method for Precision Circuit Separation
Hey there! If you’re in the world of electronics manufacturing, you know that creating a printed circuit board (PCB) is only half the battle. The process of separating those PCBs from a larger panel, known as PCB depaneling, is just as critical. This article dives deep into the various methods of PCB depaneling, particularly focusing on the precision and versatility offered by laser technology, and will help you understand why it’s a game-changer for modern electronics. With my 20 years of experience in the field, you’ll get insights that only come from working with the best, including giants like TP-LINK, Canon, and Foxconn. This is your go-to guide to selecting the perfect depaneling solution for your unique needs.
Detailed Explanation
1. What is PCB Depaneling and Why is It Crucial?
PCB depaneling, also called singulation, is the process of removing individual printed circuit boards from the larger panel in which they are pcbs are typically manufactured. You see, pcbs are typically produced in a larger panel format that contains multiple boards. This makes the pcb assembly process more efficient, but at the end, you have to separate boards into individual circuits. This step is absolutely critical because improper depaneling can lead to cracks, solder joint damage, or even delamination of the substrate, which can have a serious impact on product reliability. The manufacturing process relies heavily on the precision and speed of the depaneling process.
Think of it like this, you’ve spent time and resources designing and manufacturing a complex system. You wouldn’t want to risk damaging your perfectly produced printed circuit board at the last stage of the manufacturing process. That’s why choosing the correct depaneling method is not just about separating individual printed circuit, it’s about ensuring the quality and longevity of your electronic devices.
2. What are the Traditional Depaneling Methods?
Before the advent of advanced laser technology, traditional methods like V-groove cutting, die-cutting, and punching were the standard. Each of these cutting methods has its advantages and disadvantages, often depending on the type of pcbs used and the desired volume. V-groove cutting involves creating grooves in the panel that are then snapped apart. Die-cutting uses a sharp tool to cut through the pcb material and a punch is used to separate the boards. While these methods can be suitable for some pcb applications, they often involve mechanical stress which can be problematic with more delicate components or intricate designs.
For instance, V-groove cutting, while being a relatively lower cost option, is limited to straight-line cuts and can produce a rough cut edge. Die-cutting, another option used for pcb cutting, is better for complex shapes, but it’s typically suited to high volume runs and requires very specific tooling, making it less flexible. These traditional methods can also lead to stress on the board, potentially damaging the solder joints and compromising the integrity of the electronic components. This is why the industry is leaning more towards laser routing and laser cutting.
3. What are the Advantages of Laser Depaneling?
Laser depaneling has revolutionized the pcb industry. Why? Because a laser system offers unparalleled precision, speed, and flexibility. Unlike mechanical methods, a laser uses a non-contact approach, directing a highly focused beam of light to vaporize material along a predefined cut line. This means there is minimal mechanical stress on the pcb, greatly reducing the risk of damage to the circuit or other sensitive components.
Another huge advantage is the ability to cut intricate and complex shapes with a very narrow kerf width, which is impossible with traditional tools. Laser cutting also offers very high cut quality, leaving a clean and smooth edge. This level of accuracy is especially crucial for modern electronics that demand high precision and delicate handling. Furthermore, laser depaneling can be used on a variety of materials, including flex pcbs and rigid flex, making it a very adaptable solution for various production needs. It is quickly becoming the preferred depaneling methods in pcb manufacturing. We have seen a massive shift in the demand for laser solutions.
4. Why Choose Laser Over Other PCB Cutting Techniques?
When we talk about the evolution of pcb depaneling, it’s clear that laser technology is at the forefront. Traditional methods such as mechanical routing and die-cutting can introduce mechanical stress on the board, which is a huge problem for high-density or delicate pcbs. Laser depaneling offers a non-contact solution, eliminating this issue.
Consider the manufacturing of smartphones and other modern electronic devices with compact and highly integrated components. These devices rely on very small and tightly packed electronic components. The precision of a laser allows you to work with these components without worrying about damage or contamination, offering superior cut quality. Additionally, the ability to cut complex shapes and curves with a laser offers much more flexibility in design and pcb layout compared to the constraints of traditional cutting systems. For applications that require intricate cuts, a laser is a must-have. In short, it is the only cutting method that delivers the accuracy, precision, and flexibility needed in modern electronics manufacturing.
5. What Types of PCBs Benefit Most from Laser Routing?
Laser routing shines particularly bright when we talk about flex pcb materials, rigid flex, and multilayer boards. These materials, often made from polyimide or similar flex materials, are sensitive to mechanical stress and can easily delaminate if handled roughly. Laser depaneling is the ideal method here, as it uses a focused laser source to separate individual circuits without making physical contact with the board, which makes it perfect for flex pcbs.
The precise control offered by a laser also makes it an ideal solution for small pcbs that have very tight tolerances. It offers an advantage for high-density pcbs, where even the slightest stress on the board could cause damage. Laser cutting can also handle complex contours and intricate designs with ease. If you’re working with complex or fragile printed circuit, then laser depaneling is probably the best solution for you. Additionally the high speeds that can be achieved, lead to higher throughput of products.
6. How Does Laser PCB Depaneling Reduce Mechanical Stress?
The key advantage of using a laser for pcb depaneling lies in its non-contact nature. Unlike mechanical methods that involve physical force, a laser works by directing a highly focused beam of light that vaporizes the material along the cut line. This means there is minimal mechanical stress applied to the pcb. When you use traditional tools, you run a higher risk of micro-fractures, solder joint damage, and delamination. All these can lead to decreased reliability and longevity of your product.
Another benefit to using a laser is the very precise cut kerf that can be achieved. The focused spot size of the laser results in a very narrow cut kerf, minimizing the area of material affected by the cutting process. This becomes critical when handling closely packed components. The non-contact nature of laser pcb depaneling not only reduces mechanical stress but also minimizes the risk of dust and contamination, ensuring a much cleanliness manufacturing process. With a laser solution there is no wear and tear of the tools, such as cutting blades or similar.
7. What Are the Key Components of a Laser System for PCBs?
A typical laser pcb depaneling system consists of several key components that work together to deliver the precise cutting process. At the heart of the system is the laser source, which can be a CO2 laser, a fiber laser, or a uv laser. The type of laser depends on the specific application and the type of pcbs being processed. UV laser is commonly used in the electronics industry because of its very small wavelength and focused spot size and the very low heat it generates.
Other essential components include the optical system, which guides and focuses the laser beam; a motion control system, which precisely positions the laser over the pcb; and a vision system, which helps align the laser path with the design. Safety features, such as enclosures and interlocks, are also crucial for operating laser cutting equipment safely. The performance of a laser pcb depaneling system heavily relies on the quality and interaction of these key components. In summary, a system is more than just a laser, it’s a carefully engineered machine.
8. What About Lower Cost Alternatives for PCB Depaneling?
While laser depaneling offers superior performance, traditional methods like V-groove cutting and punch are still used because of their lower cost and relative simplicity. These methods are appropriate for simpler designs and large-volume runs where ultimate precision isn’t necessary. V-groove cutting, for example, relies on scoring lines on the printed circuit board and then breaking them apart. This method is ideal for straight lines and is often used for applications that require a basic, fast depaneling process.
Similarly, die-cutting uses a specialized tool to cut the pcb from the larger panel. While these methods are lower cost, they do have limitations. They often generate mechanical stress, are not suitable for intricate designs, and may result in a lower cut quality. Therefore, while traditional methods might initially seem like a lower cost option, you must weigh the long-term impact on product quality and reliability as well as consider the total manufacturing process costs. If your circuit boards require precision and complex shapes, it is always worth considering laser pcb depaneling.
9. What is the Role of Laser in Wearable Technology Manufacturing?
The rise of wearable technologies, such as smartwatches and fitness trackers, has created a new demand for precision manufacturing techniques. These devices are characterized by their small size, complex internal components, and use of flexible circuit boards. Laser depaneling has become an essential process in the production of these devices. The precise control and non-contact nature of laser technology allows for cutting delicate flex pcbs without causing damage, which is essential for their reliable performance.
With the trend towards smaller and more functional wearables, laser routing offers the flexibility and precision necessary to meet this need. For example, the small form factor of these devices requires the ability to cut very tight and complex shapes while avoiding any stress on the board or surrounding electronic components. This is why the demand for high quality laser pcb depaneling systems is growing rapidly with the growth of the internet of things and wearable technologies.
10. How Can Our Depaneling Systems Meet the Demands of Today’s Manufacturing?
As a world-leading manufacturer of depaneling systems, we at PCB Depaneling understand the challenges of modern electronics production. Our product range includes advanced laser pcb depaneling systems such as the DirectLaser series, which are designed to meet the stringent requirements of high-precision applications. We offer solutions for various production needs. Whether it is high volume pcb manufacturing or more intricate design. Our laser systems are known for their reliability, precision, and efficiency, ensuring that our customers can achieve the best possible outcomes.
We also offer V-groove solutions and punching machinery, providing a range of options for every budget. We can help you choose the right depaneling method that matches your production goals. For example, we offer a comprehensive range of products including:
- GAM 380AT PCB Bottom Depaneling Machine for automatic pcb separation.
- ZM30-ASV Fully Automatic saw-type V-groove PCB depaneling for high volume production.
- ZM10T & 15T PCB & FPC Punching Cutting Machine for simpler designs.
- The DirectLaser H5 PCB-FPC Laser Cutting Machine for high precision cuts.
Our laser pcb depaneling systems are used by some of the biggest names in the industry, including TP-LINK, Canon, BYD, Flex, TCL, Xiaomi, Lenovo, OPPO, HONOR, and Foxconn. We take pride in supporting the leading innovators by providing solutions that exceed expectations. Our goal is to help you achieve the perfect balance of precision, speed, and cost efficiency.
FAQs
- What is the main difference between laser and mechanical PCB depaneling? The main difference is the nature of the cutting process. Laser depaneling is a non-contact method that minimizes mechanical stress, while mechanical methods rely on physical force and can cause damage to sensitive solder joints and other components.
- Can laser cutting handle flex pcbs? Yes, laser cutting is especially well-suited for flex pcbs due to its non-contact nature and ability to make precise cuts on delicate flex materials without causing delamination or damage.
- Is laser depaneling more expensive than traditional methods? While the initial investment for a laser system can be higher, the long-term benefits of laser depaneling—including higher precision, minimal damage, and increased flexibility—often make it a more cost-effective option for high-quality, complex pcbs and electronic components.
- What kind of maintenance is required for laser systems? The maintenance of laser systems mainly involves keeping the optics clean and periodically checking the alignment of the laser beam. The frequency of maintenance depends on the usage and the working environment of the machine. We also offer maintenance contracts if you want peace of mind.
- What are the typical applications that require laser pcb depaneling? Laser depaneling is commonly used in the manufacturing of smartphones, wearables, high-density boards, and any other applications that require high precision and delicate material handling.
Conclusion
Choosing the right method for pcb depaneling is crucial for the quality and reliability of your electronic products. While traditional methods may offer lower cost solutions, laser depaneling stands out for its superior precision, flexibility, and minimal mechanical stress, making it the preferred choice for modern electronics manufacturing. With 20 years in the field, I have seen firsthand how laser technology has transformed the pcb industry. Our depaneling systems, used by leading tech companies, demonstrate our commitment to quality and innovation. We have solutions for all, whether you are a large plant or a smaller operation.
Here’s a quick summary of what we’ve discussed:
- Laser depaneling offers non-contact precision cutting, minimizing mechanical stress.
- Laser routing is ideal for complex shapes, flex pcbs, and high-density boards.
- Traditional methods are lower cost but lack the precision of laser cutting.
- Our products have been proven by leading electronic companies and are in use all over the world.
- We provide comprehensive depaneling solutions tailored to your specific needs.
To learn more about how our depaneling systems can benefit your production process, I invite you to explore our range of products. Contact us today and let our expertise and support help you achieve manufacturing excellence. Don’t settle for less when it comes to precision, choose a proven partner for pcb depaneling. We are here to support your goals. If you would like to learn more about our products, please check out our GAM 360AT In-Line PCB Separator Machine, or our GAM 330AT In-Line Automatic PCB Router Machine. For those of you working with flex, be sure to see our ZM10T & 15T PCB & FPC Punching Cutting Machine. Also check out our ZM30-ASV Fully Automatic saw-type V-groove PCB depaneling, or our DirectLaser H5 PCB-FPC Laser Cutting Machine.