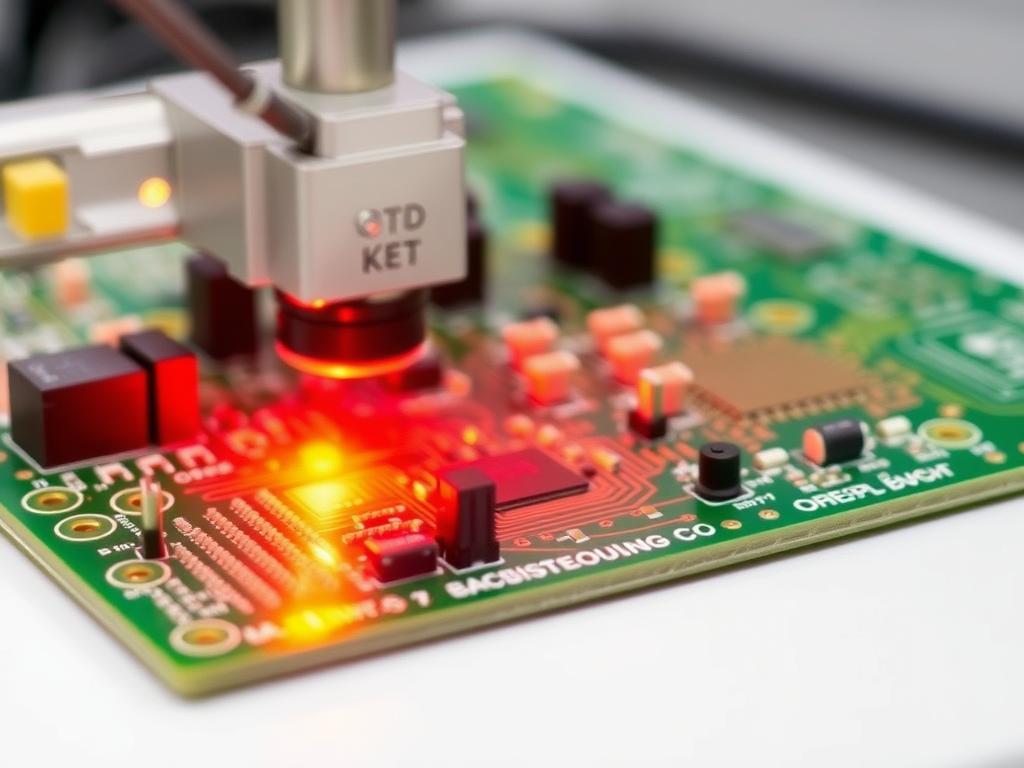
PCB depaneling for small businesses
Precision Cuts, Peak Efficiency: Mastering PCB Depaneling with Laser Technology and Beyond
For anyone involved in electronics manufacturing, the quest for efficiency and precision is never-ending. After two decades in this industry, I can tell you that one critical juncture often overlooked is depaneling. It’s the final separation of individual pcbs from a manufactured array, and the method you choose can drastically impact your production efficiency and the integrity of your circuit boards. This article dives deep into the world of pcb depaneling, focusing on the transformative power of laser depaneling and other key techniques. Understanding these processes is crucial whether you’re overseeing a large production line or crafting individual pcbs.
Decoding Depaneling: Finding the Right Tools to Separate Your PCBs
With my 20 years in the depaneling field, I’ve seen countless approaches to separating pcbs. Let’s explore some of the fundamental questions surrounding this critical stage in electronics manufacturing.
What is PCB Depaneling and Why is it a Critical Step in Manufacturing Circuit Boards?
Depaneling is, in simple terms, the process of separating individual circuit boards from a larger panel, often referred to as an array, after the components have been assembled and soldered. Think of it like separating individual crackers from a connected sheet. Why is this so vital? Because manufacturing printed circuit boards in panel form significantly increases efficiency during the component placement and smt soldering stages. However, to be used in final products, these interconnected pcbs need to become individual pcbs. The depaneling method you select directly impacts the mechanical stress applied to the circuit board, the speed of the separation process, and ultimately, your overall production efficiency. We, as experts in depaneling, understand this implicitly. Our solutions are designed to minimize stress and maximize throughput, a principle that has earned the trust of industry leaders like TP-LINK and Canon.
Considering Different Depaneling Methods: When Should You Choose a Router for PCB Cutting?
While laser depaneling is gaining significant traction, traditional methods like using a router for pcb cutting remain relevant and effective in many scenarios. A router, essentially a high-speed spindle with a specialized mill, physically cuts the pcbs apart along pre-programmed paths. This depaneling method is often preferred for thicker boards or when dealing with materials where laser cutting might not be the most efficient or cost-effective solution. The precision of modern routing machines ensures clean cuts, and they can handle various board shapes. Think of our PCB Router Machine category – it offers a range of robust solutions for precisely this purpose. Companies like BYD and Flex often utilize these routing techniques for their dependable performance.
What are the Key Advantages of Laser Depaneling for PCBs?
Laser depaneling has revolutionized the way we separate pcbs, offering a suite of advantages that are particularly crucial for today’s increasingly complex and sensitive electronics. The primary benefit is the non-contact nature of the process. Thanks to the laser, there is zero mechanical stress on the circuit board, eliminating the risk of damage to delicate components. This is a significant advantage when working with densely populated boards. Furthermore, laser cutting offers unmatched precision, allowing for intricate cutting paths and complex board shapes that are difficult to achieve with traditional methods. The speed and flexibility of laser systems also contribute to increased throughput. Consider our DirectLaser H1 High-Precision Laser Cutting Machine – it embodies these advantages, delivering exceptional cutting accuracy with minimal impact on the pcbs. This is why manufacturers like TCL and Xiaomi are increasingly adopting laser depaneling solutions.
Exploring the Precision of Laser Systems: How Does Laser Depaneling Work?
Laser depaneling systems utilize a focused beam of light to precisely vaporize the material along the desired cutting path. Sophisticated software and control systems ensure accuracy and repeatability. The programme defines the exact path the laser will follow, taking into account the array layout and the geometry of the individual pcbs. High-powered uv laser sources are often used to achieve clean and efficient cuts on a variety of pcb materials, including fr4. Features like advanced vision systems with fiducials recognition further enhance the cutting accuracy. The programme can be easily adjusted for different board designs, offering unparalleled flexibility. Imagine the precision needed for cutting extremely thin or flexible printed circuit boards – laser depaneling excels in these applications.
When is a Pizza Cutter or V-Groove Method Suitable for Depaneling PCBs?
While laser depaneling offers the highest precision and lowest stress, simpler methods like using a pizza cutter or relying on v-groove technology have their place, particularly for high-volume applications with less stringent requirements. A pizza cutter, essentially a sharp rotary blade, is used to manually score a pcb along pre-scored lines. V-groove depaneling involves pre-scoring channels into the pcb along the intended separation lines; the pcbs are then snapped apart. These methods are generally more cost-effective for large arrays of simple, rectangular pcbs. However, they introduce significantly more mechanical stress on the board compared to laser or router methods, potentially damaging sensitive components.
Understanding the Benefits of In-Line Depaneling Systems for High-Volume Production
For high-volume electronics manufacturing, inline depaneling systems are crucial for maximizing production efficiency. These systems integrate seamlessly into the production line, often using a conveyor to move the arrays through the depaneling process. Inline depaneling can incorporate various depaneling methods, including routers or lasers, and often includes automated loading and unloading mechanisms. This reduces manual handling, increases throughput, and ensures consistent depaneling quality. Think of our inline solutions – they are designed for continuous operation and can significantly boost the output of large manufacturing facilities. Companies like Lenovo and OPPO leverage inline depaneling to maintain their high throughput.
What are Depaneling Tools and Which Tools are Best for Different PCB Materials?
The tools used for depaneling vary based on the chosen method. For router systems, specialized mill bits are essential. These bits come in various shapes and sizes, optimized for different materials and cut profiles. Laser depaneling systems utilize precisely controlled laser systems, often uv lasers for optimal performance with materials like fr4. For manual methods, depaneling tools might include pizza cutters or specialized pliers. Choosing the right tools to separate the pcbs from the panel is critical for achieving the best cutting results and minimizing damage. Proper maintenance and timely replacement of these tools are also crucial for consistent performance.
Why is Minimizing Mechanical Stress Important During the Depaneling Process?
Minimizing mechanical stress during the depaneling process is paramount to ensure the reliability and functionality of the finished product. Excessive stress can lead to micro-fractures in the circuitry or damage to sensitive components, potentially causing premature failure. Methods like laser depaneling are particularly advantageous in this regard, offering a stress-free separation process. Even with router systems, careful programmeming and appropriate fixture design can help minimize stress. The goal is to separate the multiple individual pcbs without imparting any undue force that could compromise their integrity.
Exploring the Future of Depaneling: What Innovations are on the Horizon?
The field of pcb depaneling continues to evolve, driven by the ever-increasing demands for miniaturization and efficiency. We see a continued trend towards more sophisticated and faster laser systems, with advancements in laser sources and control software. Inline depaneling systems are becoming even more integrated with smart factory concepts, incorporating data analytics for process optimization and traceability. There’s also ongoing research into new depaneling methods that can handle increasingly complex pcb designs and materials. As electronics become smaller and smaller, the need for precise and low-stress depaneling solutions will continue to rise. We are actively involved in exciting, future-oriented projects to stay at the forefront of these innovations.
Frequently Asked Questions About PCB Depaneling
What is the main difference between router and laser depaneling? Router depaneling uses a physical mill to cut the pcbs, while laser depaneling uses a focused beam of light for a non-contact separation.
Is laser depaneling suitable for all types of PCBs? While highly versatile, very thick circuit boards might be more efficiently processed with a router.
What are the benefits of using an inline depaneling system? Inline systems offer increased throughput, reduced manual handling, and consistent depaneling quality, making them ideal for high-speed production.
What is mechanical stress and why is it a concern in depaneling? Mechanical stress is the physical force applied during depaneling, which can damage components or the circuit board. Laser depaneling offers zero mechanical stress.
What are some common tools to separate PCBs manually? Common manual depaneling tools include pizza cutters and specialized pliers.
Key Considerations for Efficient PCB Depaneling
- Depaneling is a crucial step in the assembly process that impacts product quality and production efficiency.
- Laser depaneling offers high precision and stress-free separation, ideal for sensitive components.
- Router systems are effective for thicker boards and certain material types.
- Inline depaneling is essential for maximizing throughput in high-volume manufacturing.
- Choosing the right depaneling method and tools is critical for optimal results.
With two decades of experience in pcb depaneling, we understand the nuances of this critical process. Whether you would like one of our high-precision laser depaneling systems, a robust depaneling router, or a complete inline depaneling solution, we have the expertise to guide you. Our commitment to quality and innovation ensures that our customers achieve the best cutting results and optimal production efficiency. We encourage you to find more information about our depaneling machines and how they can enhance your operations. Don’t hesitate to have your employees to contact our team to discuss your specific requirements resulting from the increasing miniaturization and complexity of modern electronics. Whether you need a stand alone unit or a fully integrated inline or offline system, we can provide the system that meets your needs optimally. Let us help you navigate the world of depaneling and achieve peak efficiency in your printed circuit manufacturing.