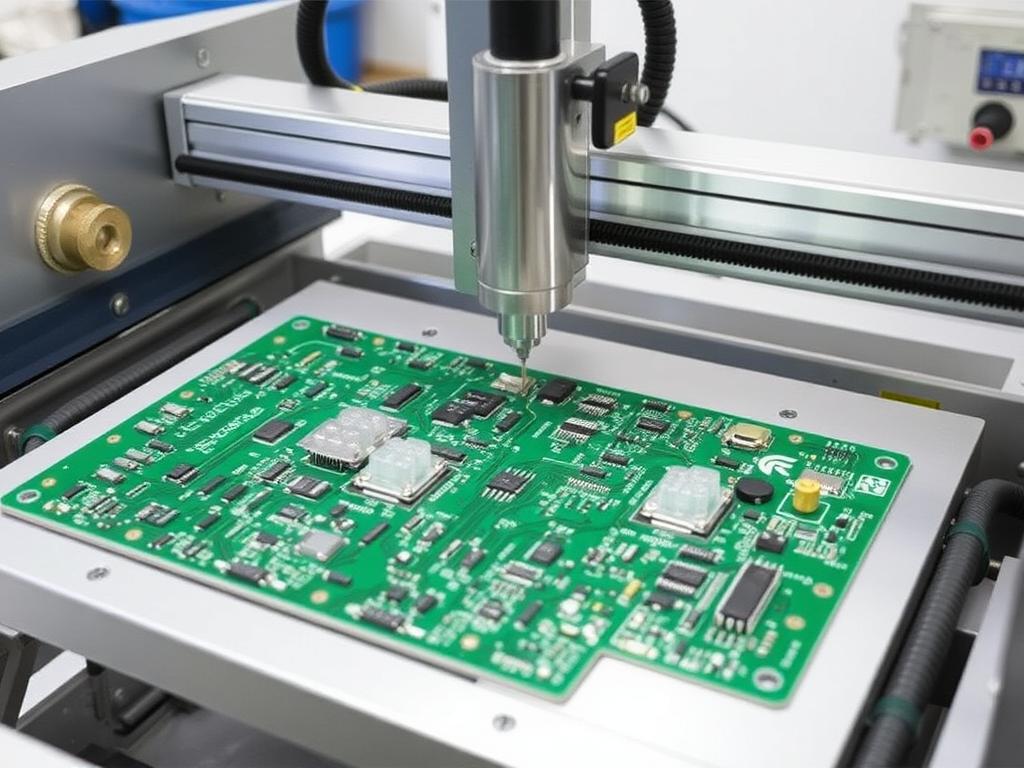
Manual PCB depaneling machines
Precision PCB Depaneling: From Manual to Machine Solutions – Request a Quote Today!
For over two decades, I’ve been immersed in the world of PCB manufacturing. I’ve seen firsthand the evolution of depaneling, from painstaking manual methods to the sophisticated machines we use today. This article is your comprehensive guide, whether you’re a large electronics manufacturer like TP-LINK, Canon, BYD, Flex, TCL, Xiaomi, Lenovo, OPPO, HONOR, or Foxconn (all of whom trust our depaneling equipment), or an individual PCB enthusiast. We’ll explore everything from the basics of manual PCB depaneling to the advantages of using automated solutions, helping you make informed decisions for your production needs. I’ll share some insights from my 20 years in the field, so you can understand the critical aspects of this process.
Navigating the World of PCB Depaneling
Here’s a roadmap of what we’ll cover to help you find the perfect depaneling method for your operation:
1. What is PCB Depaneling and Why Does it Matter?
PCB depaneling is the process of separating individual printed circuit boards from a larger panel after the assembly process. Think of it like breaking apart a sheet of postage stamps – except these stamps are complex electronic circuit boards. This separation process is critical because the assembly of components is usually done on a larger panel to increase efficiency in production. Without effective depaneling, you can’t move these individual pcbs down the line. Proper depaneling also ensures that the final product is free from defects caused by excessive force or mishandling during separation. The method you choose directly impacts the final quality of the circuit boards, and we’ll guide you on how to make the best choice based on my two decades of experience.
2. Manual PCB Depaneling: When is it Suitable?
Manual PCB depaneling might be your go-to for low-volume production or when you’re working with very simple board designs. For example, if you are running a small-scale prototyping business, manual methods can be surprisingly efficient. In these scenarios, a manual approach can be more cost-effective than investing in expensive equipment. I’ve seen many startups effectively use manual tools for their initial phases. Manual depaneling involves using tools like hand-held cutters, blades, or even a simple “break away” method using pre-scored v-cut lines on the pcbs. Remember, the key here is to apply consistent and controlled force to avoid damaging the components or board itself. For more complex boards or higher volumes, however, manual methods can become too slow and inconsistent.
When considering manual depaneling, it’s crucial to account for the potential risk of stress and damage to the circuit boards. While it might seem straightforward, improper techniques can lead to micro-cracks or stress fractures that affect the long-term reliability of the product. That’s why, for more intricate or delicate projects, it’s a good practice to move on from purely manual methods and consider more precise and gentle options like automated machines. Also consider this when you move towards higher production volumes.
3. What Are the Common Tools Used for Manual Depaneling?
When it comes to manual pcb depaneling, the right tool makes all the difference. The most common tools include:
- Hand Cutters/Snips: These are often the first choice for simple break-away depaneling. They are good for easily separating the boards along pre-scored v-cut lines.
- Scoring Tools: These are used to deepen or make v-cut lines more prominent. They are especially helpful when the pre-scored lines aren’t sufficient for a clean break.
- Manual Separators: Some tools are designed with a lever or other mechanism to apply a more controlled breaking force, helping to reduce the chance of damage.
While these tools are practical for small tasks, you’ll notice that they rely heavily on the operator’s skill and consistency. This is where you might see inconsistencies in the separation, and this is why automated equipment often provides more dependable results in volume. Choosing the correct tool should depend on your particular board type, and the material as well as the layout of the panel. For instance, a thicker or harder material might require a sturdier tool.
4. Automated PCB Depaneling Machines: A Game Changer?
The leap from manual to automated depaneling is indeed a game changer for many in the electronics industry. Automated depaneling machines use a range of technologies to precisely and quickly separate individual pcbs from a panel. These machines offer numerous advantages, including:
- Increased Speed: Automated machines can process many boards per hour, significantly increasing your production throughput.
- Precision and Consistency: Unlike manual methods, these machines ensure each pcb is separated with the same precision, reducing errors and damage.
- Reduced Stress on Components: They often use gentler methods like routing or laser cutting that minimize stress on the components.
- Safety: Automated machines generally are safer to operate than manual tools.
Automated machines also integrate easily into production lines. They can be part of a whole smt system, streamlining production from start to finish. For instance, we often see our depaneling machines integrated with pick and place machines and other assembly equipment. The result is a smoother and more efficient production process. This is essential for high-volume manufacturers that need to maintain quality and reduce costs. We’ve seen the shift to automation greatly increase efficiency and improve reliability, and the companies that adopt this technology usually see a big advantage.
5. Which Type of Depaneling Machine is Best for My Needs?
Choosing the right depaneling machine depends on a number of factors. Let’s look at the key types:
- Router Machines: These machines use a high-speed router bit to precisely cut the pcbs out of the panel. They are great for intricate shapes and materials that are difficult to separate using other methods. Our router machines are especially popular for their adaptability to different board thicknesses and designs. For example, the GAM series machines offer incredible precision for complex boards, and we have seen many customers increase quality control with this type of machine.
- V-Cut Depaneling Machines: These machines use a blade or a circular blade to break apart pcbs that have been pre-scored with v-cuts. V-cut machines are best suited for panels with straightforward, linear designs, and it’s a cost-effective approach for high volume production. The ZM series offers great reliability for this method.
- Laser Depaneling Machines: Using laser cutting to separate individual pcbs, these machines are ideal for highly precise cutting with very little stress to the board and components, they are especially useful for fragile material or complex designs. This is an emerging technology, and our DirectLaser series is designed for this type of application.
- Punching Machines: These use a die to punch individual pcbs out of a panel. This is suitable for high-volume and consistent shapes and materials, and is particularly useful for PCB/FPC.
The best choice depends on several factors: your production volume, the complexity of your board design, the sensitivity of your components, and your budget. It also depends on the material type and the board thickness that you normally process, making sure the equipment is compatible.
6. How Does V-Cut Depaneling Compare to Router-Based Depaneling?
When choosing between v-cut and router based depaneling, it’s essential to know the strengths and limitations of each. V-cut depaneling is a more straightforward process that relies on pre-scored lines on the panel. The benefits are simplicity and cost-effectiveness, but it is limited to simple straight line designs. It is good for standard pcbs with a v-cut line, and it works best in high volume production where there is not a need for complex shapes or intricate cutting.
On the other hand, router-based depaneling offers greater flexibility and precision and is very effective in removing the tab and connecting material. This method utilizes a high-speed router bit to accurately cut out individual pcbs. The advantages are that the process is suitable for more complex designs, as well as a wide range of material and board thicknesses, and you can process shapes that would be too difficult for v-cut systems. While the initial investment in router equipment is higher, many find that the added flexibility and reduced damage makes it a more sound investment long term.
7. What About PCB/FPC Punching Machines for Depaneling?
PCB/FPC punching machines are a specialized option for depaneling. These machines use a die to punch individual pcbs or flexible printed circuits (fpc) from the larger panel. This method is most effective for large volumes of pcbs with simple shapes, and is quick and precise.
Our ZM10T and 15T punching machines are designed for this specific purpose and we’ve found them to be popular with factories specializing in FPC or pcb production where they process many boards of the same size and shape, and need this method of separation. The advantages of this system are that they are quick and produce high volumes of the same shape accurately, and the disadvantages are that there is only one shape output and the material needs to be suitable for this method.
8. What are Some Key Factors to Consider When Choosing Depaneling Equipment?
Selecting the correct depaneling equipment for your business is an important decision. Here are some critical factors to consider:
- Production Volume: Are you processing a few prototypes or thousands of pcbs daily? Your volume will determine whether you need a manual, semi-automatic, or fully automatic system.
- Board Complexity: Do you have simple, rectangular boards or intricate, multi-layer designs? The complexity dictates the precision needed, with laser and router options being the best for complex requirements.
- Component Sensitivity: Are your components sensitive to stress? If so, consider a less forceful method like laser or routing.
- Material Type: Are you working with FR4, aluminum, or flexible material? The type of material will influence your machine choice. For instance, a fragile or flexible material may be best suited for laser or router depaneling, and a thicker material or multiple layers would need a more powerful system.
- Budget: How much are you looking to invest? This will have a large impact on your choice. Manual methods are the lowest cost, while fully automated lines are the highest. You need to balance cost with the quality and throughput.
- Integration: Does the machine need to be part of a larger production line, or will it stand alone? This will influence the automation and system requirements.
Taking these factors into account ensures you choose equipment that aligns with your production goals. It’s also important to think about future scale requirements.
9. How Does Automation Improve Quality and Speed in Depaneling?
Automation plays a huge role in modern PCB depaneling. Automated depaneling machines not only increase speed but also significantly improve quality, with the benefits including:
- Consistent Results: Machines produce consistent results every time, unlike manual methods where results can vary based on the operator’s skill.
- Reduced Errors: Automated systems can greatly reduce human error, leading to fewer damaged pcbs.
- Faster Processing: Machines can handle much higher volumes, accelerating your production process. This is vital in industries where time to market is critical.
- Integration with other equipment: Automated systems can integrate directly into other smt process, and other production equipment, allowing for a seamless production flow.
- Improved material Handling: Automated systems will safely handle the pcbs, which reduces the chance of human error.
By automating the depaneling process, electronics manufacturers can achieve a higher degree of precision and efficiency, ultimately reducing costs and improving the quality of their final products. Automation is becoming more common in the industry, and those companies adopting this technology will greatly benefit.
10. What if I Need a Complete SMT Production Line?
We don’t just provide depaneling solutions; we can also provide the entire SMT production line if needed. For our clients needing a complete smt setup, our solutions can integrate various machines and equipment, including:
- Pick and Place Machines: These machines automatically place surface mount components onto the pcbs.
- Reflow Ovens: These ovens are designed to melt the solder paste and complete the soldering process.
- Screen Printers: Apply solder paste to the pcbs prior to component placement.
- Conveyors: Moving pcbs between different processes.
- Inspection equipment: Ensure the solder process is correct, and that all the components are soldered on correctly.
- Automatic Plate Setting Machines: For automatic loading and unloading the panels from various stages.
Having a complete smt line provides a seamless and efficient production environment, where all the stages are integrated, and can help eliminate bottlenecks. We can customize a solution to meet your needs.
Ready to take the next step?
I’ve shared with you some of the insights I have gathered over the past 20 years in the PCB depaneling business. We can provide your business with the right equipment to meet your production requirements. Here are a few key areas we specialize in:
- PCB Router Machines: Our GAM series router machines provide precise and efficient cutting for various board types.
- V-Groove Depaneling: We have a wide selection of v-cut machines including the ZM series which is designed for simple, cost-effective high volume applications.
- PCB/FPC Punching Machines: When punching is required, our ZM10T/15T machines will deliver high volume results.
- PCB Laser Depaneling: For delicate and precise cutting, our DirectLaser Series is the top of the line.
We have the right solution for you. Contact us today, and we will provide you with a quote, and help you select the best system for your needs.
FAQs
- What if I am unsure which machine I need for my process? We’ll help you, with our decades of experience. Send us some information about the pcbs you’ll be processing and we’ll be able to advise you on the best solution.
- Can I request a quote? Yes, we encourage you to request a quote directly from our website.
- What is your returns policy? We have a comprehensive returns policy. Feel free to ask us any questions you may have.
- Do you ship internationally? Yes, we ship our equipment worldwide, and we can arrange shipping to anywhere.
- What does your warranty cover? Our equipment comes with a standard warranty. Ask our sales team for more information.
Key Takeaways
- Depaneling is a critical step in pcb manufacturing, and affects the quality of the end product.
- Manual methods are suitable for low-volume production, and manual depaneling can be a cost-effective approach for smaller runs.
- Automated machines provide greater speed, consistency, and reduced stress on components.
- Router, v-cut, laser, and punching machines each have specific advantages, depending on your needs.
- Choosing the right equipment depends on factors like production volume, board complexity, material, and budget.
- Automation leads to improved speed, precision, and reduced stress.
- We can provide complete smt production lines.
- Contact us today to request a quote and let us help you find the perfect solution for your PCB production line.
Internal Links
You might also be interested in our GAM 380AT PCB Bottom Depaneling Machine, or our GAM330AT In-Line Automatic PCB Router Machine. You can also view our V-Groove Depaneling equipment or maybe you need to see our PCB/FPC Punching Machine. If you are looking to add to your SMT whole line equipment, we can help you find a solution. If you are using laser, then see our PCB Laser Depaneling page.
By choosing us, you are choosing a supplier that has been a lead in the industry for 20 years, and is trusted by the largest companies in the electronics world.