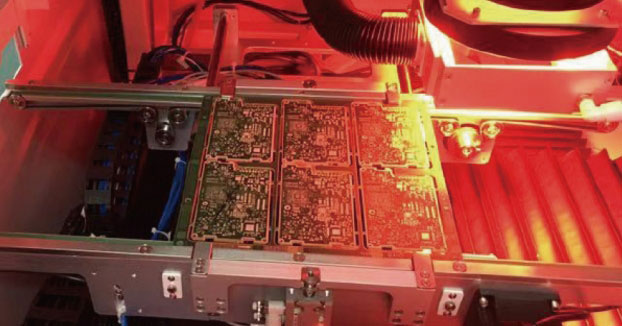
Laser Cutting PCB Board Machine Manufacture Increase Production Capacity By 30%
Introduction
In the ever-evolving world of electronics manufacturing, precision, efficiency, and customization are crucial. One area where these elements converge is in the use of laser cutting PCB boards. As the industry pushes the boundaries of miniaturization and complexity, traditional methods of PCB depaneling have been gradually supplanted by laser technology, which offers unmatched precision and versatility. This article delves into the intricacies of laser cutting PCBs, exploring its applications, advantages, and how it’s revolutionizing the PCB prototyping and production landscape.
Table of Contents
The Rise of Laser Cutting in PCB Manufacturing
Laser cutting has emerged as a game-changer in the PCB manufacturing process. Unlike mechanical methods such as routing or punching, laser cutting employs a focused beam of light to cut or engrave materials. This method allows for extremely precise cuts with minimal thermal stress on the components, ensuring the integrity of delicate circuits.
Laser cutting PCBs are particularly beneficial during the prototyping phase. With the increasing demand for custom PCB prototyping, manufacturers need a method that allows for rapid and accurate production. The ability to quickly iterate designs without the need for costly and time-consuming tooling changes is a significant advantage of laser technology.
For instance, a prototyping laser cutter can seamlessly transition from one design to another, making it ideal for short production runs or when multiple iterations are necessary to perfect a design. This flexibility is a key reason why laser cutting has become the preferred method for custom PCB prototyping.
Advantages of Using Laser Cutting for PCBs
- Precision and Accuracy
Laser cutters can achieve cuts with tolerances as tight as ±0.01 mm, making them ideal for intricate PCB designs. This level of precision is particularly valuable when dealing with high-density interconnect (HDI) PCBs, where space is at a premium, and even the slightest misalignment can cause a malfunction. - Reduced Thermal Stress
Traditional cutting methods often generate heat that can damage sensitive components or cause warping. Laser cutting minimizes this risk by concentrating heat in a small area, reducing the likelihood of thermal deformation. - Versatility
Whether working with rigid, flexible, or rigid-flex PCBs, laser cutting can handle a wide range of materials and thicknesses. This versatility makes it an invaluable tool in the production of modern electronic devices. - Speed and Efficiency
Laser cutting is not only precise but also fast. The ability to cut complex shapes and multiple layers in a single pass significantly reduces production time, making it an efficient choice for both prototyping and large-scale manufacturing. - No Need for Tooling
One of the most significant advantages of laser cutting is that it eliminates the need for physical tooling. This not only reduces costs but also allows for faster transitions between different designs, further enhancing production efficiency.
Applications in PCB Prototyping
In the realm of PCB prototyping, laser cutting is invaluable. The prototyping laser cutter enables rapid production of boards, allowing designers to quickly test and iterate on their designs. This capability is particularly useful in industries such as aerospace, automotive, and consumer electronics, where innovation is driven by rapid development cycles.
Custom PCB prototyping often requires the ability to make quick adjustments to the design. With laser cutting, these changes can be made on the fly, without the need for new tooling or lengthy setup times. This flexibility not only speeds up the development process but also reduces costs, making it a popular choice among engineers and designers.
Laser Cutting vs. Traditional Depaneling Methods
While traditional methods like routing, punching, and V-grooving have their merits, laser cutting offers distinct advantages that are hard to overlook.
- Routing: While effective, routing can cause mechanical stress on the PCB, potentially leading to damage. Laser cutting, on the other hand, is a contactless process, eliminating the risk of physical damage.
- Punching: Punching is fast but lacks the precision needed for complex designs. Laser cutting provides the accuracy required for today’s intricate PCB layouts.
- V-Grooving: This method is limited to straight-line cuts, whereas laser cutting can handle any shape or pattern, making it far more versatile.
The comparison clearly shows that laser cutting is not just an alternative but a superior option for many PCB depaneling needs.
Environmental Impact of Laser Cutting
In addition to its technical benefits, laser cutting is also more environmentally friendly compared to traditional methods. Since it requires no physical contact, there is no generation of waste in the form of worn-out tools or broken drill bits. Moreover, the precision of laser cutting reduces material wastage, contributing to a more sustainable manufacturing process.
Manufacturers committed to reducing their carbon footprint will find laser cutting to be an environmentally responsible choice, aligning with global trends toward greener production practices.
Choosing the Right Laser Cutter for PCB Prototyping
Selecting the right prototyping laser cutter is crucial for achieving the desired outcomes in PCB production. Factors to consider include the type of laser (CO2 or fiber), power output, cutting speed, and compatibility with different PCB materials. For instance, fiber lasers are generally preferred for cutting metals, while CO2 lasers excel in cutting non-metals like the substrates used in PCBs.
Manufacturers must also consider the software that comes with the laser cutter. Advanced software can significantly enhance the precision and efficiency of the cutting process, offering features like auto-nesting to minimize material wastage.
Conclusion
Laser cutting represents the future of PCB manufacturing. Its precision, versatility, and efficiency make it an indispensable tool in both prototyping and production. As the demand for more complex and miniaturized electronics continues to grow, the adoption of laser cutting technology will only increase, solidifying its place as a cornerstone of modern electronics manufacturing.
For more information on PCB depaneling and to explore the latest in laser cutting technology, visit our PCB Depaneling Machine page or learn more about PCB Laser Depaneling on our website.
FAQs
- What is the primary advantage of using a laser cutter for PCBs?
The primary advantage is the high precision and minimal thermal stress on the components, ensuring the integrity of intricate circuits. - Can laser cutting be used for both rigid and flexible PCBs?
Yes, laser cutting is versatile and can be used on various materials, including rigid, flexible, and rigid-flex PCBs. - Is laser cutting more environmentally friendly than traditional methods?
Yes, laser cutting generates less waste and uses less energy compared to traditional methods, making it a more sustainable choice. - What type of laser is best for PCB cutting?
CO2 lasers are typically best for cutting non-metals like PCB substrates, while fiber lasers are better suited for metals. - How does laser cutting compare to other depaneling methods?
Laser cutting offers superior precision, reduced thermal stress, and greater versatility compared to routing, punching, and V-grooving.
Summary
Laser cutting is revolutionizing PCB manufacturing, offering unparalleled precision and efficiency. It is particularly beneficial in the prototyping phase, where rapid iterations and custom designs are essential. As the industry continues to evolve, the role of laser cutting in producing high-quality, complex PCBs is set to grow, making it an indispensable tool for modern electronics manufacturing.