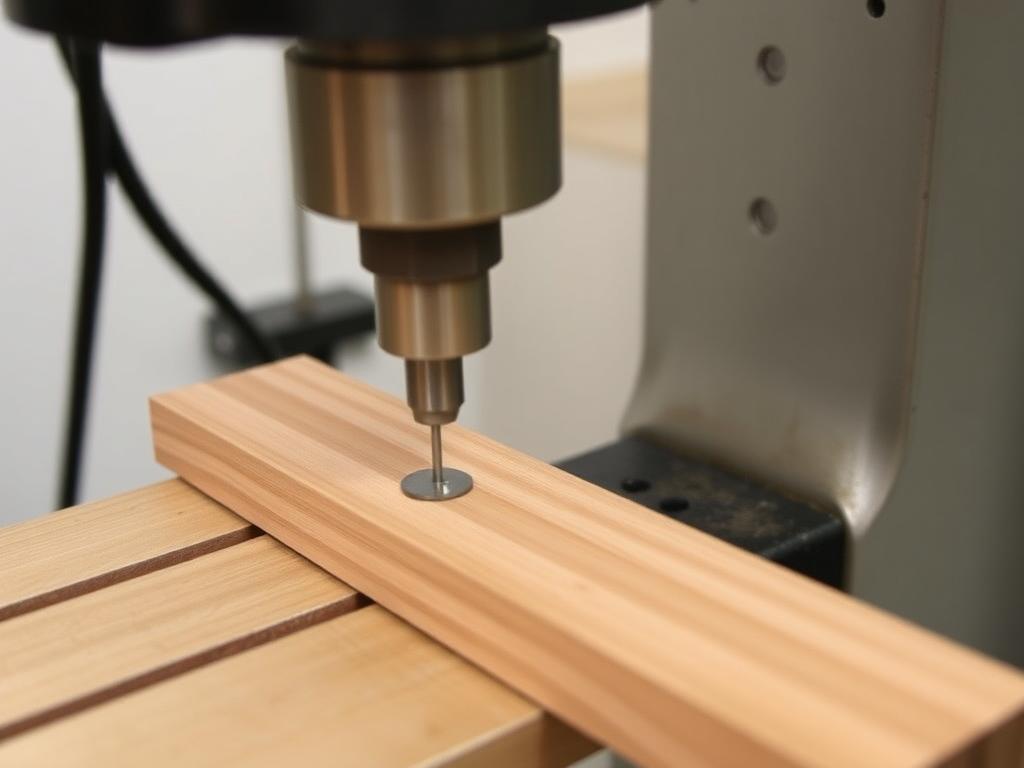
How to use a fly cutter on a mill
The Ultimate Guide to Milling Cutters: Choosing the Right Tool for Your Needs
In the world of precision machining, the mill cutter is an indispensable tool. Whether you’re a large electronic product processing factory or an individual PCB enthusiast, understanding the different types of milling cutters and their applications can significantly enhance your production efficiency and product quality. This article is your comprehensive guide to milling cutters, offering insights into their types, uses, and how to select the right one for your needs. Read on to discover how the right milling cutter can transform your machining processes.
Article Outline
- What is a Mill Cutter?
- Different Types of Milling Cutters: An Overview
- How to Select the Right Milling Cutter for Your Machine?
- Understanding the Geometry of Milling Cutters
- End Mills vs. Face Mills: What’s the Difference?
- The Role of Cutting Speed in Milling Operations
- How Milling Cutters are Used in PCB Manufacturing
- The Importance of High-Speed Steel in Milling Cutters
- FAQs About Milling Cutters
- Conclusion: Key Takeaways for Choosing Milling Cutters
What is a Mill Cutter?
A mill cutter is a cutting tool used in milling machines to remove material from a workpiece. These tools come in various shapes and sizes, each designed for specific milling operations. The cutter rotates while the workpiece remains stationary, allowing for precise material removal.
Different Types of Milling Cutters: An Overview
Milling cutters are available in a variety of shapes and sizes, each suited for different applications. Some common types include:
- End Mills: Used for creating complex shapes and profiles.
- Face Mills: Ideal for cutting large, flat surfaces.
- Ball Cutters: Used for creating rounded edges and surfaces.
- Dovetail Cutters: Perfect for creating dovetail joints.
Understanding the type of milling cutter you need is crucial for achieving the desired results in your machining projects.
How to Select the Right Milling Cutter for Your Machine?
Choosing the right milling cutter involves considering several factors:
- Material of the Workpiece: Different materials require different cutter materials and geometries.
- Type of Milling Operation: Whether you’re performing face milling, peripheral milling, or form milling, the cutter must be suited to the task.
- Machine Compatibility: Ensure the cutter is compatible with your milling machine’s specifications.
For more detailed guidance, visit our Milling Cutter page.
Understanding the Geometry of Milling Cutters
The geometry of a milling cutter, including its cutting edge and cutter axis, plays a significant role in its performance. The angle of the cutter, the number of cutting teeth, and the cutter’s diameter all influence the efficiency and quality of the milling process.
End Mills vs. Face Mills: What’s the Difference?
End mills and face mills serve different purposes in machining:
- End Mills: Used for detailed work, such as cutting slots and profiles.
- Face Mills: Designed for removing large amounts of material quickly and efficiently.
Understanding these differences can help you choose the right tool for your specific needs.
The Role of Cutting Speed in Milling Operations
Cutting speed is a critical factor in milling operations. It affects the quality of the cut, the lifespan of the cutter, and the overall efficiency of the process. Adjusting the cutting speed according to the material and cutter type can optimize your milling operations.
How Milling Cutters are Used in PCB Manufacturing
In PCB manufacturing, milling cutters are used to cut slots, shape edges, and create precise profiles. Our PCB Depaneling Machine is a prime example of how advanced milling technology can enhance PCB production.
The Importance of High-Speed Steel in Milling Cutters
High-speed steel is a popular material for milling cutters due to its durability and ability to withstand high temperatures. This makes it ideal for high-speed milling operations, ensuring long-lasting performance and precision.
FAQs About Milling Cutters
- What is the difference between climb milling and conventional milling? Climb milling involves the cutter rotating in the same direction as the feed, while conventional milling rotates against the feed direction.
- How do I maintain my milling cutters? Regular cleaning, proper storage, and timely sharpening are essential for maintaining the performance of your milling cutters.
- Can milling cutters be used for non-metal materials? Yes, milling cutters can be used for materials like plastic and wood, provided the cutter material and geometry are suitable.
- What is the significance of the cutter’s diameter? The diameter affects the cutter’s ability to remove material and the surface finish of the workpiece.
Conclusion: Key Takeaways for Choosing Milling Cutters
- Understand the specific needs of your project to select the right type of milling cutter.
- Consider the material and geometry of the cutter for optimal performance.
- Regular maintenance is crucial for extending the life of your milling cutters.
For more information on our products and services, visit our PCB Depaneling page or contact us through our Contact Us page.By understanding the intricacies of milling cutters, you can enhance your machining processes, improve product quality, and increase efficiency. Whether you’re a large-scale manufacturer or an individual enthusiast, the right milling cutter can make all the difference.