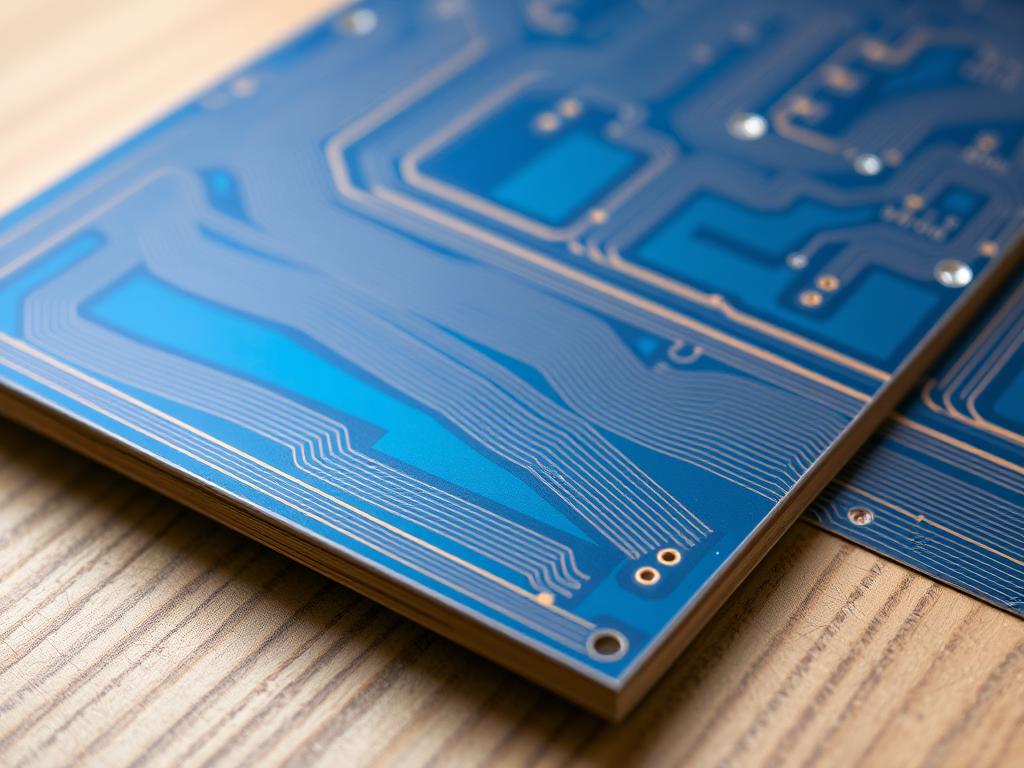
precision inline depaneling for small boards
Mastering PCB Depaneling: The Ultimate Guide to Depaneling Machines and Laser Technology
Printed Circuit Board (PCB) depaneling might sound complex, but it’s a crucial step in electronics manufacturing that can make or break your product’s quality. Whether you’re part of a large electronic product processing factory or an individual PCB enthusiast, understanding depaneling machines—especially the latest in laser technology—can significantly boost your production efficiency and product reliability. This comprehensive guide will walk you through everything you need to know about PCB depaneling, from the basics to advanced techniques, ensuring you’re well-equipped to optimize your depaneling process.
Table of Contents
What Is Depaneling in PCB Manufacturing?
Depaneling is the process of separating individual PCBs from a larger panel or array after manufacturing. Think of it like cutting slices from a loaf of bread. This step is essential because it affects the mechanical stress exerted on the boards, which can impact the performance of sensitive components.
Why Is Depaneling Important?
- Quality Assurance: Proper depaneling ensures that the circuit board functions as intended without defects.
- Efficiency: An optimized depaneling process can greatly improve production efficiency.
- Component Safety: Minimizes mechanical stress to avoid component damage.
Types of Depaneling Machines: Laser vs. Mechanical
Choosing the right depaneling machine is like choosing the right tool for a job—it makes all the difference.
Mechanical Depaneling Machines
These machines use physical tools like mills or routers to cut through the PCB material.
- Example: The GAM 330AT In-Line Automatic PCB Router Machine is designed for high-speed, precise cuts.
Laser Depaneling Machines
Using a focused laser beam, these machines offer a contactless and stress-free process.
- Example: The DirectLaser H5 PCB-FPC Laser Cutting Machine provides high-precision cuts with minimal board stress.
Why Choose Laser Depaneling for Your PCBs?
Laser depaneling is revolutionizing the industry, and here’s why:
- Precision: Achieve cuts with tolerances as low as 0.01Â mm.
- Versatility: Suitable for various materials, including FR4, aluminum PCBs, and flexible circuits.
- Speed: High cutting speed reduces production time.
- Low Stress: Eliminates mechanical contact, thus reducing mechanical stress on PCBs.
How Does Laser Cutting Improve Depaneling Efficiency?
Laser cutting streamlines the depaneling process in several ways:
- Automation: Integrates seamlessly with inline systems for continuous production.
- Customization: Easily adjust settings for different panel sizes and designs.
- Low Maintenance: Fewer moving parts mean less wear and tear.
Real-World Impact
A manufacturer using the DirectLaser H3 Laser Online Machine reported a 30% increase in throughput and a 25% reduction in production costs.
Understanding Depaneling Machine Specifications (mm, Mill)
When evaluating depaneling machines, certain specs are vital:
- Cutting Tolerance (mm): Determines the precision level.
- Mill Type: Affects the quality and speed of mechanical cutting.
- Spindle Speed: Higher speeds allow for smoother cuts.
Quick Tip
Always match the machine’s capabilities with your specific depaneling requirements to ensure optimal performance.
The Impact of Depaneling on PCB Quality
Depaneling isn’t just about separating boards; it’s about maintaining their integrity.
- Stress-Free Processes: Methods like laser depaneling are designed to minimize board stress and avoid component damage.
- Quality Control: High-precision machines reduce the risk of defects.
Laser Depaneling vs. Mill Routing: Pros and Cons
Both methods have their place in PCB manufacturing.
Laser Depaneling
Pros:
- High precision
- Suitable for complex designs
- Minimal mechanical stress
Cons:
- Higher initial cost
- Requires safety precautions due to laser use
Mill Routing
Pros:
- Lower cost
- Good for simple designs
- Familiar technology
Cons:
- Generates mechanical stress
- Tool wear can lead to inconsistencies
How to Select the Right Depaneling Machine for Your Needs
Consider these factors:
- Production Volume: High volumes may benefit from inline depaneling systems.
- Material Type: Different materials like FR4 or flexible circuits require specific machines.
- Budget: Weigh the initial investment against long-term benefits.
Recommended Machines
- For high-volume production, consider the GAM336AT In-Line Automatic PCB Depaneling Machine.
- For versatility, the ZM30-ASV Fully Automatic Saw-Type V-Groove PCB Depaneling is a solid choice.
Advancements in Depaneling Technology
The future is bright, with innovations enhancing efficiency and quality.
- UV Laser Technology: Offers even higher precision with lower power consumption.
- AI Integration: Machines that learn and optimize over time.
- Modular Systems: Easily upgrade components as technology evolves.
Optimizing the Depaneling Process for High-Volume Production
Efficiency is king in large-scale manufacturing.
- Automation Solutions: Implement systems like the SMT In-Line Depaneling Machine Solution for seamless operation.
- Employee Training: Skilled operators can maximize machine capabilities.
- Regular Maintenance: Keeps machines running at peak performance.
How to Minimize Stress and Avoid Component Damage During Depaneling
Protecting your components is crucial.
- Choose the Right Machine: Opt for stress-free methods like laser depaneling.
- Optimize Settings: Adjust parameters to suit your PCB panels and materials.
- Use Quality Tools: High-quality milling cutters reduce the risk of damage.
Frequently Asked Questions About PCB Depaneling Machines
Is laser depaneling suitable for all types of PCBs?
Yes, laser depaneling is versatile and works with various PCB materials, including flexible circuits and aluminum PCBs.
What safety measures are required when operating laser depaneling machines?
Proper shielding, safety goggles, and adherence to safety protocols are essential.
How does depaneling affect production efficiency?
Efficient depaneling methods can greatly improve production efficiency by reducing time and minimizing defects.
Can depaneling machines handle large panel sizes?
Yes, machines like the GAM 380AT PCB Bottom Depaneling Machine are capable of handling large panels.
What is the difference between inline and offline depaneling systems?
Inline depaneling integrates with your production line for continuous operation, while offline depaneling is a stand-alone process done separately.
How often should depaneling equipment be maintained?
Regular maintenance schedules are recommended, typically every 6-12 months, depending on usage.
Conclusion
Depaneling is more than just a step in the manufacturing process; it’s a critical factor that affects the overall quality and reliability of your electronic products. By understanding the different types of depaneling machines and technologies, you can make informed decisions that align with your production goals.
Key Takeaways
- Depaneling impacts both quality and efficiency in PCB manufacturing.
- Laser depaneling offers precision and minimizes mechanical stress.
- Understanding machine specs like mm and mill is crucial.
- Automation and inline depaneling systems are ideal for high-volume production.
- Regular maintenance and operator training are essential for optimal performance.
Ready to take your depaneling process to the next level? Explore our range of cutting-edge depaneling machines designed to meet various production needs. From the high-speed GAM386 Standalone Bottom Cut PCB Router Machine to the versatile ZM30 PCB Round Blade V-CUT Separator, we’ve got you covered.
Our products are trusted by industry leaders like TP-LINK, Canon, BYD, Flex, TCL, Xiaomi, Lenovo, OPPO, HONOR, and Foxconn.
Note: This guide is based on industry expertise and aims to provide reliable information. For personalized solutions, don’t hesitate to contact us.