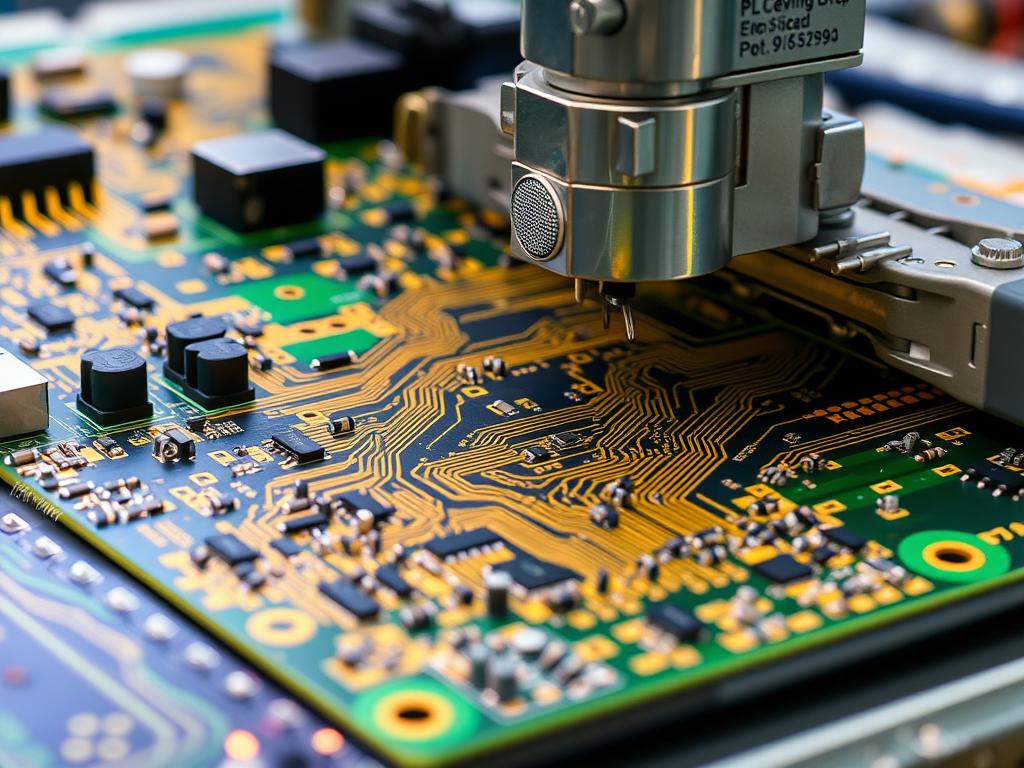
High-speed SMT equipment
Revolutionizing PCB Assembly: The Ultimate Guide to High-Speed SMT Pick and Place Machines
In the fast-paced world of electronics manufacturing, efficiency and precision are paramount. As someone who has spent two decades immersed in the PCB industry, I’ve witnessed firsthand the transformative impact of high-speed SMT pick and place machines. These marvels of engineering are the workhorses of modern PCB assembly, enabling the rapid and accurate placement of components onto circuit boards. This comprehensive guide delves into the intricacies of SMT pick and place machines, exploring their functionality, benefits, and how they are shaping the future of surface mount technology. Whether you’re a seasoned professional working with electronic technology companies, a manager in a large electronic product processing factory, or an individual PCB player, this article will provide you with valuable insights into the world of high-speed SMT and how it can elevate your PCB assembly process to new heights.
What is an SMT Pick and Place Machine and Why is it Essential?
SMT (Surface Mount Technology) has revolutionized electronics manufacturing, and at the heart of this revolution lies the SMT pick and place machine. These machines automate the process of picking up electronic components, such as resistors and integrated circuits, and placing them onto printed circuit boards (PCBs) with incredible speed and accuracy.
In my 20 years in the industry, I’ve seen pick and place machines evolve from bulky, slow machines to the lightning-fast, highly precise systems we have today. They are essential for any PCB assembly operation, from prototypes to high-volume production runs. A reliable SMT pick and place machine is a cornerstone for achieving the efficiency and quality demanded by today’s electronics market. They are the backbone of modern assembly lines, capable of handling a wide range of component types and sizes.
How Do High-Speed SMT Pick and Place Machines Work?
High-speed SMT pick and place machines are marvels of engineering, capable of placing thousands of components per hour. They work by using a combination of advanced technologies:
- Component Feeders: Feeders deliver components to the pick-up point. Common types include tape, tube, and tray feeders.
- Vision System: An advanced vision system, often using multiple cameras, identifies the component, determines its orientation, and guides the placement head.
- Placement Head: The placement head, equipped with a nozzle, picks up the component using vacuum suction.
- Motion System: A high-precision motion system, often using linear motors, moves the placement head to the correct position on the PCB.
- Control System: A sophisticated control system coordinates all these actions, ensuring accurate and rapid component placement.
Our advanced PCB Laser Depaneling machines are designed to work in concert with these pick and place systems, ensuring a streamlined and efficient assembly process. Check out our PCB Laser Depaneling page to learn more about how these machines can benefit your production line.
What are the Key Components of an SMT Pick and Place System?
An SMT pick and place system is more than just the machine itself. It’s a carefully integrated system of components working together. From my experience, these are the key elements:
- Feeders: As mentioned earlier, feeders are crucial for delivering components. Choosing the right feeder for each component type is essential for efficient operation.
- Nozzles: The nozzle on the placement head must be compatible with the component being placed. Different sizes and shapes are available.
- Vision System:Â A high-resolution vision system is essential for accurate component recognition and placement.
- Software: Management software controls the entire process, from programming the machine to monitoring its performance. Some even offer smart factory integration.
- Conveyor System: A conveyor system transports PCBs to and from the pick and place machine, ensuring a smooth workflow.
Component | Function |
---|---|
Feeders | Supply components to the pick-up point in various formats (tape, reel, tube, tray). |
Nozzles | Vacuum nozzles on the placement head pick up and release components. |
Vision System | Uses cameras to identify component type, orientation, and position for accurate placement. |
Software | Controls machine operation, programming, job setup, and often integrates with factory management systems. |
Conveyor | Transports PCBs to and from the pick and place machine, ensuring smooth production flow. |
Ensuring these components work seamlessly together is crucial. Our V-Groove Depaneling machines are designed to complement these systems, providing a complete line solution. Visit our V-Groove Depaneling page for more details.
What are the Different Types of SMT Pick and Place Machines Available?
The world of SMT pick and place machines is diverse, with different types designed for specific needs. Here are some common types I’ve encountered:
- Manual Pick and Place:Â These are basic machines that require manual intervention for component placement. They are suitable for very low-volume or hobbyist use.
- Semi-Automatic Pick and Place: These machines automate some aspects of the process, such as PCB transport, but still require manual assistance for component placement.
- Automatic Pick and Place: These are fully automated machines capable of high-speed component placement. They are ideal for medium to high-volume production. Some of the most renowned brands are Panasonic’s NPM-W2, and Yamaha.
- High-Speed Chip Shooters:Â Optimized for placing small, passive components like resistors and capacitors at extremely high speeds.
- Flexible Placers: Designed to handle a wide range of component types and sizes, from small passives to large integrated circuits. An example of this is the high-speed compact modular mounter RX-8 or the advanced flexible mounter LX-8.
Choosing the right type of machine depends on your production requirements, including volume, product mix, and budget. We offer a range of pick and place solutions, including specialized machines like our PCB/FPC Punching Machines. Our PCB/FPC Punching Machine page has more information.
How Does Feeder Technology Impact the Efficiency of SMT Pick and Place?
Feeder technology is a critical aspect of SMT pick and place efficiency. The right feeder can significantly improve throughput and reduce errors. In my experience, here are some key considerations:
- Feeder Capacity: High-capacity feeders reduce the frequency of component replenishment, minimizing downtime.
- Feeder Accuracy: Precise feeders ensure that components are presented to the placement head in the correct orientation every time.
- Feeder Flexibility: Some feeders can handle multiple component types or sizes, making them ideal for high-mix production environments.
- Intelligent Feeders: Advanced feeders can communicate with the pick and place machine, providing information about component levels and other data.
- Feeder Setup: Proper feeder setup is vital. Using an automatic feeder rack and a good feeder management system can save time and reduce human error, which is crucial for ensuring efficient assembly process.
Investing in high-quality feeder technology can yield significant improvements in overall SMT line efficiency. It’s about ensuring that each component, whether it’s a small resistor or a complex integrated circuit, is delivered to the pick and place machine accurately and reliably. The feeder system utilizes intelligent technology to enhance the performance of the place machines. The right feeder also supports lower labor costs and reduce cost of production.
What Role Does Soldering Play in the SMT Assembly Process?
Soldering is a fundamental part of the SMT assembly process. It’s the process of creating a permanent electrical and mechanical connection between the component and the PCB. After the pick and place machine has placed the components, the PCB moves on to the soldering stage.
There are primarily two soldering methods using SMT:
- Reflow Soldering: This is the most common method for soldering of surface mount devices. The PCB with placed components is passed through a reflow oven, which gradually heats the board to melt the solder paste, creating the solder joints. Convection is the most common heating method in modern ovens.
- Wave Soldering: This method is typically used for through-hole components but can also be used for some SMT components on the bottom side of the PCB. The PCB is passed over a wave of molten solder, which adheres to the exposed metal areas, creating the solder joints. Also, soldering machines are machines designed to solder electronic components onto PCBs.
The choice of soldering method depends on the types of components being used and the design of the PCB. Achieving high-quality solder joints is crucial for the reliability of the final product. Using lead-free solder has become increasingly important in recent years due to environmental concerns.
Why is a Solder Paste Printer Crucial for High-Quality SMT Assembly?
Before components can be placed and soldered, solder paste must be applied to the PCB. This is where the solder paste printer comes in. It’s a critical piece of equipment in the SMT line.
The solder paste printer uses a stencil to apply solder paste precisely to the solder pads on the PCB. The stencil is a thin sheet of metal, usually stainless steel, with apertures that correspond to the locations where solder is needed. The solder paste, a mixture of tiny solder particles and flux, is pushed through the apertures using a squeegee.
The accuracy of the solder paste printer directly impacts the quality of the solder joints. Too much solder can lead to bridging between adjacent pads, while too little can result in weak or incomplete joints. Modern solder paste printers use vision systems for stencil alignment and pressure control to ensure precise and consistent solder paste application. Some offer features such as automatic smt stencil cleaning and solder paste reflow soldering inspection systems. The solder paste printer is the first step of high-speed placement and a good printer enhances the component placement process.
How Do Reflow Ovens Ensure Reliable Solder Joints in SMT?
The reflow oven is where the magic happens in reflow soldering. After the pick and place machine has placed the components and the solder paste printer has applied the solder paste, the PCB enters the reflow oven.
A reflow oven has multiple heating zones, each with a carefully controlled temperature. As the PCB moves through the oven, it goes through a specific temperature profile:
- Preheat Zone: The PCB is gradually heated to activate the flux in the solder paste.
- Soak Zone: The temperature is held constant to allow the flux to clean the solder pads and components.
- Reflow Zone: The temperature is raised above the melting point of the solder, creating the solder joints.
- Cooling Zone: The PCB is gradually cooled to solidify the solder joints.
This controlled heating and cooling process is essential for creating strong, reliable solder joints without damaging the components or the PCB. Modern reflow ovens often use forced convection heating for even temperature distribution. Some also offer nitrogen atmosphere to minimize oxidation during the soldering process. A well-maintained curing oven can also play a vital role in this process.
What are the Benefits of Using Advanced Inspection Systems in SMT?
Inspection systems are the quality control guardians of the SMT process. They ensure that each PCB meets the required quality standards before moving on to the next stage of production or being shipped to the customer. Here’s why they are crucial:
- Defect Detection: AOI (Automated Optical Inspection) systems use high-resolution cameras to inspect PCBs for defects such as missing components, incorrect orientation, solder bridges, and insufficient solder.
- Process Improvement: Data from inspection equipment can be used to identify trends and improve the assembly process, reducing the likelihood of recurring defects, such as using a different nozzle or adjusting the soldering machine.
- Cost Savings: Catching defects early in the assembly process is much cheaper than finding them later or after the product has been shipped. Inspection systems can help avoid costly rework or product recalls.
- Quality Assurance: Inspection systems provide documented evidence that each PCB has been inspected and meets the required quality standards, which can be very important when you melt the solder.
In my experience, investing in advanced inspection systems like AOI is essential for maintaining high quality in SMT assembly. They are a crucial part of any line solution focused on delivering top-notch circuit board assembly. They are also useful for mid-volume and high-volume production runs, depending on the throughput required. With inspection systems, you can maintain a high throughput while maintaining quality.
How Can Our SMT Solutions, Including iTech, Help Optimize Your Production Line?
We are a world-leading manufacturer of PCB depaneling machines, and our expertise extends to providing comprehensive SMT solutions. Our products, including our SMT equipment, are trusted by Fortune 500 companies like TCL, Xiaomi, and Lenovo. We offer innovative solutions for a wide range of PCB assembly needs.
- Cutting-Edge Technology: Our machines, including our high-speed SMT pick and place machine options, incorporate the latest advancements in SMT technology, such as stepper motors and advanced pressure control systems.
- Customization: We understand that every production line is unique. We offer customized line solution options tailored to your specific needs, whether you’re producing prototypes or running high-volume assembly lines.
- Comprehensive Support: From initial consultation to installation and ongoing maintenance, we provide comprehensive support to ensure your SMT line operates at peak efficiency.
- iTech Integration: Our iTech solutions offer advanced automation and control capabilities, helping you move towards a smart factory environment.
Our SMT solutions are designed to integrate seamlessly with other equipment in your production line, such as our SMT In-Line Depaneling Machine Solution. We also offer specialized equipment like our GAM 330AT In-Line Automatic PCB Router Machine and 310AT In-Line Automatic PCB Depanelizer, which can further enhance the efficiency of your PCB assembly process. Whether you need a benchtop solution or machines for high-volume runs, we can help.
By partnering with us, you gain access to decades of experience and a commitment to providing the best possible SMT solutions. Let us help you optimize your PCB assembly process and achieve your production goals with our high-speed pick-and-place machines and other advanced equipment.
Frequently Asked Questions (FAQs)
1. What is the difference between a chip shooter and a flexible placer?
A chip shooter is optimized for high-speed placement of small, passive components like resistors and capacitors. A flexible placer, like a Juki or Panasonic, can handle a wider range of component types, including larger integrated circuits and odd-form components.
2. How often should I replace feeders on my SMT pick and place machine?
Feeder lifespan depends on usage and maintenance. Regular inspection and cleaning are essential. We recommend replacing feeders when they show signs of wear or start to impact placement accuracy. Some machine makes require less maintenance than others.
3. What is the advantage of using a nitrogen atmosphere in reflow soldering?
Using a nitrogen atmosphere during reflow soldering reduces oxidation, resulting in stronger and more reliable solder joints. It’s particularly beneficial when using lead-free solder.
4. Can your pick and place machines handle different PCB sizes?
Yes, our pick-and-place machines can be configured to handle a wide range of PCB sizes. We can customize the conveyor system and software to accommodate your specific production requirements.
5. What kind of training and support do you offer?
We offer comprehensive training on machine operation, programming, and maintenance. Our support team is available to assist with any technical issues and can provide on-site support when needed.
Key Takeaways
- High-speed SMT pick and place machines are essential for modern PCB assembly, enabling rapid and accurate component placement.
- These machines use advanced technologies such as component feeders, vision systems, precision motion systems, and sophisticated control system units.
- Key components of an SMT pick and place system include feeders, nozzles, vision systems, software, and conveyor systems.
- Different types of pick and place machines cater to various production needs, from manual and semi-automatic to high-speed automatic machines like Yamaha and Panasonic.
- Feeder technology significantly impacts SMT pick and place efficiency, with factors like capacity, accuracy, flexibility, and intelligence playing crucial roles.
- Soldering, whether reflow or wave, is a critical step in the SMT assembly process, creating permanent electrical and mechanical connections.
- Solder paste printers ensure precise application of solder paste to PCBs before component placement, which is crucial for high-speed placement.
- Reflow ovens use carefully controlled temperature profiles to create reliable solder joints without damaging components or PCBs.
- Advanced inspection systems, such as AOI, are vital for quality control in SMT, detecting defects and enabling process improvement.
- Our comprehensive SMT solutions, including iTech integration, can help optimize your production line for maximum efficiency and quality.
By embracing high-speed SMT pick and place technology and partnering with a trusted solution provider like us, you can elevate your PCB assembly capabilities and achieve new levels of success in the competitive electronics manufacturing industry. We are committed to providing cutting-edge technology and comprehensive support to help you meet your production goals. Contact us today to learn more about how our high-speed SMT solutions can transform your assembly process and drive your business forward. Our team is ready to assist you in selecting the right smt-juki or other brand-name equipment that will best suit your electronic assembly operations, including specialized surface mount machinery like an advanced flexible mounter or a flip chip bonder. We also offer smd storage solutions and rework stations to complete your surface mount assembly setup.