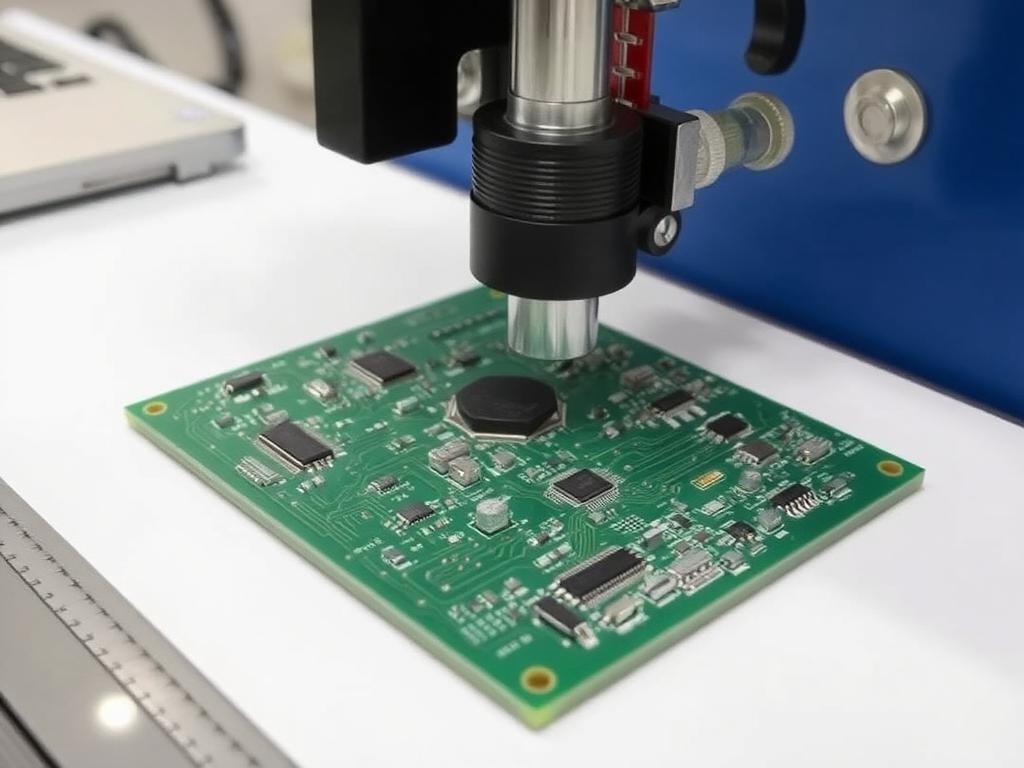
Full SMT assembly line
Revolutionizing Electronics Assembly with Fully Automatic SMT Lines: A Comprehensive Guide for Mass Production
This article delves into the world of fully automatic SMT (surface mount technology) assembly lines, the backbone of modern electronics manufacturing. Drawing from my 20 years of experience in the PCB industry, I’ll guide you through the intricacies of a state-of-the-art SMT assembly line, exploring its key components, processes, and benefits for achieving efficient, high-quality mass production SMT line. Whether you are an electronic technology company, a large electronic product processing factory, or an individual PCB player looking to bring PCB assembly in-house, this article provides a comprehensive overview of what a modern SMT line entails and why it is vital for your business. It is designed to help you understand how a well-implemented SMT assembly line can significantly enhance your electronics assembly capabilities. This article will use the AIDA model to grab your attention, maintain interest, build desire, and prompt action to request a quote for our fully automatic SMT line.
Article Outline
What is Surface Mount Technology (SMT) and Why is it Dominant in Modern Electronics?
Surface Mount Technology (SMT) has revolutionized the electronics industry. Unlike the older through-hole technology, SMT involves mounting electronic components directly onto the surface of a printed circuit board (PCB). This approach allows for smaller component sizes, higher component density, and increased automation in the assembly process. In my two decades in the industry, I’ve witnessed SMT evolve from a niche technology to the dominant method for electronics assembly, driven by the demand for smaller, faster, and more powerful electronic devices.
SMT is a method for producing electronic circuits in which the components are mounted or placed directly onto the surface of printed circuit boards (PCBs). It has become the primary method used in the electronics industry due to its efficiency, ability to use smaller components, and suitability for automation. The use of SMT allows for a higher density of components on a circuit board, which is essential for creating compact and powerful electronic devices. The technology also enables faster assembly speeds and improved high-frequency performance, making it the preferred choice for modern electronics manufacturing. This is particularly crucial in today’s fast-paced market where miniaturization and performance are key factors.
What is an SMT Assembly Line and How Does it Optimize PCB Assembly?
An SMT assembly line is a series of specialized machines working together to automate the PCB assembly process. It’s a sophisticated system designed to handle every step, from applying solder paste to placing components and soldering them onto the PCB. An SMT production line streamlines the assembly process, minimizing manual intervention and maximizing efficiency. This results in faster production times, reduced labor costs, and improved product quality and consistency.
An SMT assembly line is a series of automated machines that work together to assemble printed circuit boards (PCBs). Each machine performs a specific task in the assembly process, such as applying solder paste, placing components, and reflow soldering. The line is designed to move PCBs seamlessly from one machine to the next, ensuring a continuous and efficient workflow. The use of automated equipment reduces the need for manual assembly, resulting in faster production speeds, lower labor costs, and improved product quality. It’s a highly efficient way to achieve high-volume production of electronic products.
What are the Key Components of a Fully Automatic SMT Assembly Line?
A fully automatic SMT assembly line comprises several essential pieces of equipment, each playing a critical role in the assembly process. From my experience, the core components typically include a stencil printer, pick and place machine, reflow oven, conveyor system, and inspection systems like AOI (Automated Optical Inspection) and X-ray. Each component is designed to work in harmony, ensuring a smooth and efficient flow of PCBs through the line.
A typical SMT line includes the following key components:
- Stencil Printer: Applies solder paste to the PCB using an SMT stencil.
- Pick and Place Machine: Places SMD (Surface Mount Device) components onto the PCB with high precision.
- Reflow Oven: Heats the PCB to melt the solder paste and create solder joints.
- Conveyor System: Transports PCBs between machines.
- Inspection Systems (AOI, X-ray): Inspect PCBs for defects.
The equipment used in an SMT assembly line is designed to work together seamlessly, ensuring a smooth and efficient production process. The fully automatic SMT assembly line is a complex system that requires precise temperature and humidity control to ensure the quality of the finished product.
How Does a Stencil Printer Ensure Accurate Solder Paste Application in SMT?
The stencil printer is the first crucial piece of equipment in the SMT assembly line. It applies solder paste onto the PCB pads with precision, using a stainless-steel stencil with apertures that correspond to the component pads. Accurate solder paste application is critical, as it directly impacts the quality of the solder joints formed during reflow soldering. Modern stencil printers incorporate advanced features like automatic stencil alignment, solder paste height inspection, and automatic stencil cleaning to ensure consistent and reliable solder paste printing.
Solder paste printing is a critical step in the SMT assembly line process. The stencil printer uses a metal stencil to apply solder paste to the PCB. The stencil has openings that match the locations where components will be placed on the PCB. The stencil printer aligns the stencil with the PCB and uses a squeegee to push the solder paste through the openings and onto the PCB pads. The accuracy of the stencil printer is critical to ensuring that the correct amount of solder paste is applied to each pad. The solder paste is melted later in the reflow oven.
What is the Role of Pick and Place Machines in an SMT Assembly Line?
Pick and place machines are the workhorses of the SMT assembly line. They are responsible for accurately placing electronic components onto the PCB, precisely on the solder paste that was applied earlier. These machines use vacuum nozzles to pick up components from feeders and place them onto the PCB with remarkable speed and accuracy. Modern pick and place machines can handle tens of thousands of components per hour, and they often feature multiple placement heads, advanced vision systems for component alignment, and sophisticated software for optimizing placement sequences.
Pick and place machines are essential for the automated assembly of PCBs. They pick up components from feeders and place them onto the PCB with high precision. The speed and accuracy of pick and place machines are critical for achieving high-volume production and maintaining product quality. A pick and place machine is a type of SMT machine that is used to place components quickly and accurately on a PCB. Pick and place machines are capable of placing thousands of components per hour, making them essential for mass production SMT line.
How Does a Reflow Oven Create Reliable Solder Joints in SMT?
The reflow oven is a critical component of the SMT assembly line. It’s responsible for the reflow soldering process, which creates the electrical and mechanical connections between the SMT components and the PCB. The reflow oven subjects the PCB assembly to a carefully controlled temperature profile. This profile typically includes preheating, soaking, reflow, and cooling stages. The reflow soldering oven is designed to heat to melt the solder paste and then cool it down to form a solid connection, all while ensuring the integrity of the components and the PCB. This reflow soldering process forms the solder joints that connect the components to the PCB.
The reflow oven heats the PCB and components to a temperature that melts the solder paste, forming a strong bond between the components and the PCB. The reflow soldering process is carefully controlled to ensure that all components are properly soldered and that no damage occurs to the PCB or components. A reflow oven is a type of SMT machine that is used to prepare for the soldering of electronic components to a PCB. After the reflow soldering process, the components and the PCB are firmly bonded together. It is very important that the components are in a fixed position.
Why are Inspection Systems like AOI Crucial in a Fully Automatic SMT Line?
Inspection systems, such as Automated Optical Inspection (AOI) and Automated X-ray Inspection (AXI), are essential for ensuring the quality and reliability of PCBs produced on a fully automatic SMT line. AOI systems use high-resolution cameras and sophisticated image processing algorithms to inspect PCBs for defects such as missing or misplaced components, incorrect orientation, solder bridging, and insufficient solder. X-ray systems, on the other hand, can inspect hidden solder joints, such as those under BGA packages, ensuring the integrity of connections that are not visible to optical inspection.
AOI (Automated Optical Inspection) is a crucial part of the SMT assembly process. AOI systems use cameras to capture images of the PCB and then use image processing software to detect defects. AOI can detect a wide range of defects, including missing components, misaligned components, and poor solder joints. It can inspect the surface of a printed circuit or electronic boards in general. AOI inspection is often used in conjunction with other inspection methods, such as Automated X-ray Inspection (AXI), to ensure the highest possible level of quality. The inspection machine ensures traceability. With AOI, the travel time of the PCBs in the assembly line will be longer.
How Does Our Depaneling Equipment Integrate into a Full-Service SMT Line?
As a global leader in PCB depaneling solutions, we understand that efficient depaneling is crucial for a seamless SMT manufacturing process. Our PCB Router Machines and PCB Laser Depaneling systems are designed to integrate perfectly into fully automatic SMT lines. They provide automated, high-precision separation of individual PCBs from panels after assembly. Our V-Groove Depaneling equipment offers a reliable solution for panels with pre-scored V-grooves, ensuring clean, stress-free separation. These machines have garnered the trust of industry giants like TP-LINK, Canon, BYD, Flex, TCL, Xiaomi, Lenovo, OPPO, HONOR, and Foxconn, thanks to their reliability, precision, and ability to boost throughput while reducing labor costs.
Over my two decades in the industry, I’ve witnessed firsthand how our depaneling solutions have transformed our clients’ SMT lines. For example, a case study with Flex demonstrated a 30% increase in SMT line efficiency after integrating our laser depaneling system. This was achieved by minimizing PCB handling and reducing the risk of damage during separation. Furthermore, our PCB/FPC Punching Machines offer another efficient method for separating PCBs, particularly for irregular shapes. Our commitment to innovation and quality has made us a trusted partner for Fortune 500 companies globally, consistently delivering solutions that enhance their production capabilities. We are a full-service line supplier.
What are the Different Types of SMT Assembly Lines?
SMT assembly lines can be categorized into several types based on their level of automation, production volume, and flexibility. Some common types include:
- Fully Automatic SMT Lines: These lines offer the highest level of automation, with minimal human intervention. They are ideal for high-volume production of standardized PCBs. Our company specializes in providing state-of-the-art fully automatic SMT lines tailored to meet the specific production needs of our clients.
- Semi-Automatic SMT Lines: These lines combine automated equipment with manual processes. They offer more flexibility than fully automatic lines but may have lower throughput.
- Manual SMT Lines: These lines rely heavily on manual processes for component placement and soldering. They are suitable for low-volume production or prototyping but are less efficient for mass production.
- High-Mix, Low-Volume SMT Lines: These lines are designed to handle a wide variety of PCB designs with frequent changeovers. They prioritize flexibility over raw speed.
The choice of SMT line depends on factors such as production volume, product mix, budget, and desired level of automation. PCBs are automatically processed.
What are the Future Trends in SMT Manufacturing?
The SMT industry is constantly evolving, driven by advancements in technology and the ever-increasing demands of the electronics market. Several key trends are shaping the future of SMT manufacturing:
- Increased Automation: The use of robotics, artificial intelligence (AI), and machine learning (ML) is growing in SMT lines. This includes the integration of collaborative robots (cobots) that can work alongside human operators, as well as AI-powered systems for process optimization and predictive maintenance.
- Industry 4.0 and Smart Factories:Â SMTÂ equipment is becoming increasingly connected through the Internet of Things (IoT), enabling real-time data collection, analysis, and remote monitoring. This leads to improved process control, increased efficiency, and reduced downtime.
- Miniaturization: The trend toward smaller electronic devices is driving the need for advanced SMT processes capable of handling ultra-fine-pitch components and micro-PCBs.
- Advanced Inspection Techniques: 3D AOI, X-ray, and other advanced inspection methods are becoming more prevalent to ensure the quality of increasingly complex PCB assemblies.
- Flexible and Hybrid SMT Lines: As product lifecycles shorten and customization increases, there’s a growing need for SMT lines that can handle a wider range of PCB designs and quickly adapt to changing production requirements.
These trends are aimed at further optimizing production efficiency, improving quality control, and enabling the manufacturing of next-generation electronic products. They require precise temperature and humidity control, as well as antistatic measures.
FAQs
- What is a fully automatic SMT assembly line? A fully automatic SMT assembly line is a PCB assembly line that uses automated equipment to perform all the major steps in the SMT assembly process, including solder paste printing, component placement, reflow soldering, and inspection.
- What are the advantages of using an SMT production line? SMT production lines offer several advantages, including increased automation, higher component density on PCBs, faster assembly speeds, improved high-frequency performance, and reduced manufacturing costs compared to through-hole technology.
- What is the role of a pick and place machine in an SMT line? A pick and place machine is responsible for accurately picking up electronic components from feeders and placing them onto the PCB with high precision and speed. They are essential for automating the component placement process.
- How does a stencil printer work in SMT assembly? A stencil printer applies solder paste to the PCB pads using a stainless steel stencil with apertures that correspond to the component locations. It ensures that the correct amount of solder paste is deposited for each component.
- What is the purpose of a reflow oven in an SMT line? A reflow oven heats the PCB assembly to a specific temperature profile to melt the solder paste, creating solder joints that electrically and mechanically connect the components to the PCB. It ensures reliable reflow soldering. The reflow soldering oven is a key piece of equipment.
Conclusion
- SMT (Surface Mount Technology) is the dominant method for modern electronics assembly, enabling smaller, faster, and more powerful devices.
- Fully automatic SMT assembly lines provide an efficient and reliable solution for mass production of PCBs, offering significant advantages in terms of speed, quality, and cost.
- Key components of an SMT assembly line include stencil printers, pick and place machines, reflow ovens, conveyors, and inspection systems like AOI and X-ray.
- Our depaneling equipment, including PCB Router Machines, PCB Laser Depaneling, and V-Groove Depaneling solutions, seamlessly integrates into fully automatic SMT lines, enhancing efficiency and product quality.
- The future of SMT manufacturing involves increased automation, the use of AI and IoT, miniaturization, advanced inspection techniques, and flexible production lines.
- Choosing the right SMT line supplier and equipment is crucial for achieving your production goals and staying competitive in the rapidly evolving electronics industry.
- We are committed to providing cutting-edge SMT solutions tailored to your specific needs, helping you optimize your PCB assembly process and achieve manufacturing excellence.
Ready to transform your PCB assembly capabilities with a fully automatic SMT line? Contact us today to learn more about our comprehensive SMT solutions and how we can help you achieve your production goals. Let’s discuss your specific requirements and explore how our state-of-the-art equipment and expertise can elevate your electronics manufacturing process. We are dedicated to providing the best SMT solutions for your production needs, ensuring high-volume production with exceptional quality and efficiency. Let us help you achieve your manufacturing goals with our advanced SMT equipment and expertise. Don’t forget to request a quote and discover how we can help you achieve your manufacturing goals with our advanced SMT equipment and expertise. Check out our customer stories and industry highlights for more information.