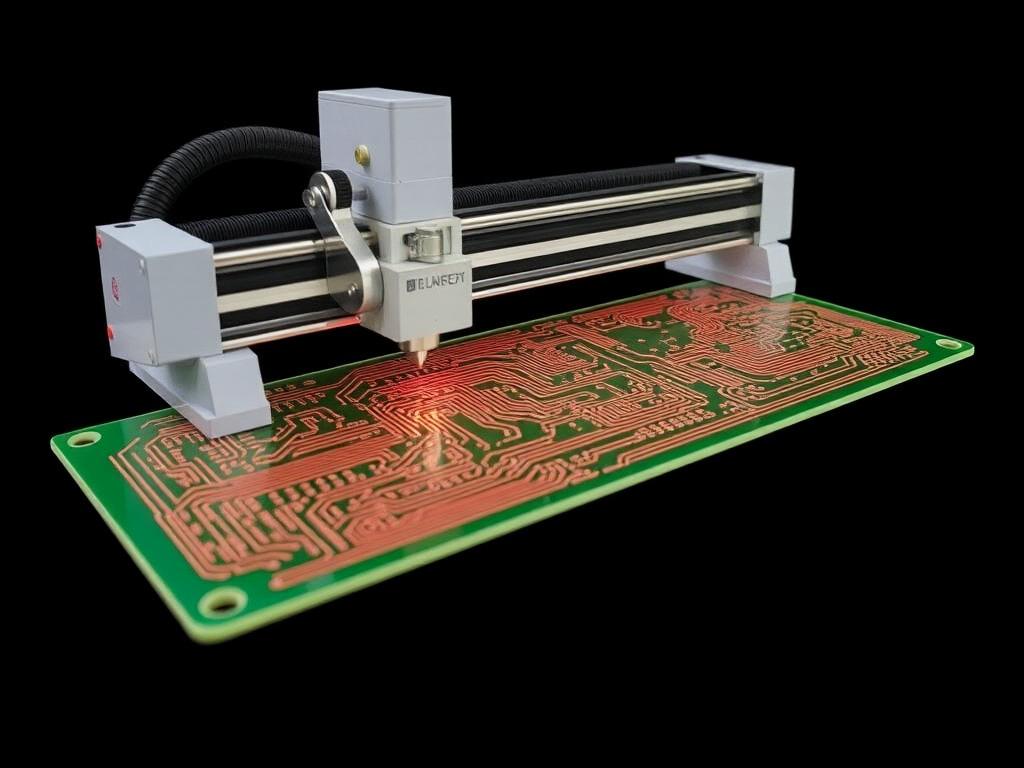
Flexible PCB punching solutions
Unlocking the Future: The Ultimate Guide to Flexible PCB Manufacturing Process
This article delves into the fascinating world of flexible PCB (flex PCB) manufacturing, exploring the intricacies of creating these adaptable circuit boards. As technology advances and the demand for compact, versatile electronic devices surges, understanding the flexible PCB manufacturing process becomes paramount. Whether you’re an engineer, a procurement manager for a tech company, or simply curious about the inner workings of modern electronics, this guide will provide valuable insights into how flexible printed circuit boards (flexible PCBs) are made and why they’re revolutionizing industries. It’s worth reading because it demystifies a complex process, revealing how companies like TP-LINK, Canon, and Foxconn are leveraging flex circuits to push the boundaries of innovation. This article explains the technology that makes our sleek, powerful devices possible.
1. What is a Flexible PCB and Why is it Important?
A flexible PCB, also known as a flex circuit or flexible printed circuit board (FPCB), is a type of circuit board that can bend and flex without breaking. Unlike rigid circuit boards, which are typically made from FR-4, flexible PCBs use a flexible plastic substrate, such as polyimide (PI), to support conductive circuit traces. This flexibility allows flex PCBs to be used in applications where rigid boards cannot, such as in wearable electronics, medical devices, and aerospace systems. The circuit in flex PCB is usually more thin and flexible than the one in the regular PCB.
The importance of flexible PCBs stems from their ability to conform to tight spaces, reduce weight, and improve reliability. In devices like smartphones and laptops, flex circuits enable compact designs by allowing components to be connected in three dimensions. They also eliminate the need for bulky connectors, reducing the overall size and weight of the device. Moreover, flexible PCBs can withstand vibrations and mechanical stress better than rigid boards, making them ideal for applications that require durability. Companies like ours specialize in providing advanced flexible circuit board solutions, including PCB Laser Depaneling, to meet the growing demand for these innovative PCBs. It’s good to know what is the difference between single-sided and double-sided circuit boards.
2. What is the Step-by-Step Flexible PCB Manufacturing Process?
The flexible PCB manufacturing process is a complex, multi-stage procedure that requires precision and expertise. Here’s a simplified overview:
- Design: The process begins with the PCB design phase, where engineers create the circuit layout using specialized software. This design is then transferred to a photomask, which will be used to pattern the circuit onto the flexible substrate.
- Material Preparation: A thin sheet of polyimide (PI) film, coated with a layer of copper, serves as the base material. This flexible laminate is cleaned and prepared for the next steps.
- Circuit Patterning: The copper layer is coated with a photosensitive resist material. The photomask is placed over the resist, and the laminate is exposed to UV light. This process transfers the circuit pattern onto the resist.
- Etching: The laminate is immersed in a chemical bath that etches away the unprotected copper, leaving behind the desired circuit traces.
- Drilling: Tiny holes, or vias, are drilled through the laminate to create connections between different layers of the circuit.
- Plating: The vias and other exposed copper areas are plated with a layer of copper, followed by a layer of tin or gold. This enhances conductivity and protects the circuit from oxidation.
- Coverlay Application: A layer of polyimide film with adhesive is applied over the circuit to protect it from damage and provide insulation.
- Cutting: The flexible PCB is cut from the larger panel using a punch or a laser. We offer specialized machines for this purpose, such as our PCB/FPC Punching Machine.
- Testing: The finished flexible PCB undergoes rigorous testing to ensure it meets the required specifications and functions correctly.
3. How Does Drilling and Plating Impact Flexible PCB Quality?
Drilling and plating are critical steps in the flexible PCB manufacturing process. Drilling creates the vias that enable electrical connections between different layers of the circuit. The precision of the drill holes directly impacts the reliability of these connections. Advanced drilling techniques, such as laser drilling, are used to create precise, high-density vias in flex PCBs.
Plating involves depositing a layer of conductive material, typically copper, onto the walls of the drill holes (plated through holes or PTH) and other exposed copper areas. This process enhances conductivity, provides a solderable surface, and protects the circuit from corrosion. The quality of the plating process is vital for ensuring the long-term reliability of the flexible PCB. A uniform, well-adhered plating layer is essential for preventing signal loss and ensuring the circuit can withstand thermal and mechanical stress. Using the punching method is not good for this part of the process.
4. What Role Does Etching Play in Flexible PCB Fabrication?
Etching is the process of selectively removing unwanted copper from the flexible PCB laminate to create the desired circuit patterns. This is a critical step in flexible PCB fabrication as it defines the electrical pathways on the circuit board. The etching process typically involves the following steps:
- Resist Application: A photosensitive resist material is applied to the copper layer of the laminate.
- Exposure: The laminate is exposed to UV light through a photomask, which contains the circuit pattern. The UV light hardens the resist in the areas that correspond to the circuit traces.
- Development: The laminate is immersed in a developer solution that removes the unhardened resist, exposing the copper underneath.
- Etching: The laminate is placed in a chemical bath, typically ferric chloride or cupric chloride, which etches away the exposed copper. The hardened resist protects the underlying copper, creating the circuit traces.
- Resist Stripping: After etching, the remaining resist is removed, leaving behind the copper circuit pattern.
The precision of the etching process is crucial for ensuring the accuracy and reliability of the circuit. Advanced etching techniques, such as plasma etching, are used to create fine circuit features and achieve tight tolerances in high-density flex PCBs.
5. How is Lamination Critical in Rigid-Flex PCB Production?
Lamination is a key step in the manufacturing process of rigid-flex PCBs, which combine the benefits of both rigid and flexible circuit boards. A rigid-flex PCB is a hybrid circuit board that incorporates both rigid and flexible sections. The rigid sections provide structural support and a mounting surface for components, while the flexible sections allow the board to bend and flex.
The lamination process for rigid-flex PCBs involves bonding together multiple layers of rigid and flexible materials using heat and pressure. The typical rigid-flex PCB stack-up includes:
- Rigid layers: FR-4 or other rigid materials
- Flexible layers: Polyimide (PI) film with copper traces
- Adhesive layers: Used to bond the rigid and flexible layers together
- Coverlays: Protective layers applied over the flexible sections
The lamination process requires precise control of temperature, pressure, and time to ensure proper bonding between the layers. Any defects in the lamination can lead to delamination, warping, or other reliability issues.
6. What Advanced Technologies are Used in Flexible PCB Assembly?
Flexible PCB assembly involves mounting electronic components onto the flexible PCB and creating the electrical interconnections. This process requires specialized equipment and techniques due to the unique properties of flex PCBs.
One of the key challenges in flexible PCB assembly is handling the flexible substrate. Unlike rigid circuit boards, flex PCBs can easily deform during the assembly process, making it difficult to accurately place components. To overcome this challenge, specialized fixtures and tooling are used to hold the flex PCB in place during assembly. Our SMT whole line equipment is designed to address these challenges, providing reliable and efficient solutions for flexible PCB assembly.
Another important aspect of flexible PCB assembly is solder joint reliability. Flex PCBs are often subjected to bending and flexing during use, which can put stress on the solder joints. To ensure solder joint reliability, specialized solder alloys and reflow profiles are used. Additionally, techniques such as strain relief and encapsulation may be employed to protect the solder joints from mechanical stress.
7. How Does Material Selection Affect Flexible PCB Performance?
Material selection is a critical aspect of flexible PCB design and production. The choice of materials directly impacts the performance, reliability, and cost of the flex PCB.
The most common substrate material for flex PCBs is polyimide (PI). PI offers excellent flexibility, high temperature resistance, and good dielectric properties. It also provides great chemical resistance and excellent resistance to radiation and UV exposure. However, other materials, such as polyester (PET) and liquid crystal polymer (LCP), may be used depending on the specific application requirements.
The choice of conductive material is also important. Copper is the most widely used conductive material in flex PCBs due to its excellent conductivity and ductility. However, the type of copper used can vary depending on the application. For example, rolled annealed (RA) copper is often used in flex PCBs that require high flexibility, while electrodeposited (ED) copper is commonly used in flex PCBs that require high density circuit patterns. These circuit patterns are essential in the final product.
8. What are the Key Capabilities of a Leading Flexible PCB Manufacturer?
As a leading flexible PCB manufacturer, we pride ourselves on our comprehensive manufacturing capabilities and commitment to quality. Our state-of-the-art facilities are equipped with the latest technologies for flexible PCB fabrication and assembly, allowing us to deliver high-quality, reliable flex PCBs for a wide range of applications.
Our key PCB capabilities include:
- High-density interconnect (HDI) technology: We specialize in manufacturing high-density flex PCBs with fine lines, small vias, and multiple layers. Our HDI capabilities enable us to create compact, high-performance flex PCBs for demanding applications such as medical devices and aerospace systems.
- Rigid-flex PCB manufacturing: We have extensive experience in manufacturing rigid-flex PCBs that combine the benefits of both rigid and flexible circuit boards. Our advanced lamination processes ensure the reliable bonding of rigid and flexible layers, resulting in durable, high-performance rigid-flex PCBs.
- Advanced assembly services: We offer comprehensive flexible PCB assembly services, including surface mount technology (SMT), through-hole technology (THT), and mixed-technology assembly. Our advanced assembly equipment and experienced technicians ensure the accurate placement and reliable soldering of components on flex PCBs.
- Testing and quality assurance: We have a rigorous testing and quality assurance process in place to ensure that every flexible PCB we produce meets the highest standards of quality and reliability. Our testing capabilities include automated optical inspection (AOI), X-ray inspection, in-circuit testing (ICT), and functional testing.
9. How Do Customized Solutions Benefit PCB Design and Production?
At [Your Company Name], we understand that every customer has unique requirements when it comes to PCB design and production. That’s why we offer customized solutions tailored to meet the specific needs of each project. Whether you need printed circuit boards for product manufacturers or circuit boards for product developers, we can help.
Our team of experienced engineers works closely with customers to understand their requirements and develop customized solutions that optimize performance, reduce costs, and accelerate time-to-market. We offer design assistance, material recommendations, and process optimization to ensure that the final product meets the customer’s exact specifications. The number of layers depends on the project needs.
One of the key benefits of our customized solutions is our ability to provide quick-turn PCB prototyping and low-volume production services. We understand the importance of rapid prototyping in the product development process, and we have streamlined our operations to offer fast PCB delivery times without compromising on quality. We also provide detailed information about the assembly costs.
10. What Are the Future Trends in Flexible PCB Technology?
The field of flexible PCB technology is constantly evolving, driven by the increasing demand for smaller, lighter, and more versatile electronic devices. Several key trends are shaping the future of flex PCB technology:
- Increased Miniaturization: As electronic devices continue to shrink in size, the demand for smaller, high-density flex PCBs will continue to grow. This trend is driving the development of new materials and manufacturing techniques that enable the creation of flex PCBs with finer features, smaller vias, and thinner circuit layers.
- Improved Materials: Advances in materials science are leading to the development of new substrate materials with improved properties, such as higher temperature resistance, better dimensional stability, and enhanced flexibility. These new materials will enable the use of flex PCBs in even more demanding applications.
- Integration with Other Technologies: Flex PCBs are increasingly being integrated with other emerging technologies, such as printed electronics, flexible displays, and industrial sensor technologies. This integration will enable the creation of new types of electronic devices with unprecedented capabilities. The flexibility of the circuit is essential.
- Enhanced Reliability: As flex PCBs are used in more critical applications, such as automotive and medical devices, the need for enhanced reliability will continue to grow. This trend is driving the development of new testing and quality assurance methods specifically designed for flex PCBs.
FAQs
- What is the difference between a rigid PCB and a flexible PCB? A rigid PCB is made from a solid, inflexible substrate material, such as FR-4, while a flexible PCB uses a flexible plastic substrate, such as polyimide (PI). Rigid PCBs are typically used in applications where the circuit board does not need to bend or flex, while flexible PCBs are used in applications that require flexibility, such as wearable electronics and foldable devices.
- What are the advantages of using a flexible PCB? Flexible PCBs offer several advantages over rigid PCBs, including the ability to conform to tight spaces, reduced weight, improved reliability in high-vibration environments, and the ability to create three-dimensional circuit designs. They also eliminate the need for bulky connectors, reducing the overall size and weight of the device. The PI is great material that provides flexibility.
- What is a rigid-flex PCB? A rigid-flex PCB is a hybrid circuit board that combines both rigid and flexible sections. The rigid sections provide structural support and a mounting surface for components, while the flexible sections allow the board to bend and flex. Rigid-flex PCBs are often used in applications that require both rigidity and flexibility, such as in aerospace and medical devices. This type of PCB provides better precision and quality.
- What is the typical lead time for flexible PCB manufacturing? The lead time for flexible PCB manufacturing can vary depending on the complexity of the design, the number of layers, the materials used, and the order quantity. However, as a leading flexible PCB manufacturer, we offer quick-turn prototyping and low-volume production services, with lead times as short as a few days for simple designs.
- How can I get a cost estimate for my flexible PCB project? You can request a cost estimate for your flexible PCB project by contacting us through our website or by sending us your design files and specifications. Our team will review your requirements and provide you with a detailed quote, including the cost of materials, manufacturing, assembly, and testing.
- Do you offer design assistance for flexible PCB projects? Yes, we offer design assistance for flexible PCB projects. Our team of experienced engineers can work with you to optimize your design for manufacturability, performance, and cost. We can also provide recommendations on material selection, circuit layout, and assembly techniques.
Conclusion
In conclusion, flexible PCB technology is revolutionizing the electronics industry by enabling the creation of smaller, lighter, and more versatile devices. The flexible PCB manufacturing process is a complex, multi-stage procedure that requires specialized equipment, materials, and expertise. As a leading flexible PCB manufacturer, we are committed to providing our customers with the highest quality flex PCBs and customized solutions to meet their unique needs. Our PCB company is the best on the market.
- Flex PCBs are transforming electronics with their versatility.
- Manufacturing involves multiple precise steps, from design to testing.
- Advanced technologies like laser drilling and plating enhance quality.
- Material selection is crucial for performance and reliability.
- Leading manufacturers offer comprehensive capabilities and customized solutions.
- Future trends include miniaturization, improved materials, and integration with other technologies.
- Flex PCBs enable innovative applications across various industries.
- The high quality plate is the key in our PCB production.
By staying at the forefront of flexible PCB technology and partnering with a trusted manufacturer like us, companies can leverage the power of flex PCBs to create innovative products that push the boundaries of what’s possible. Whether you’re developing wearable electronics, medical devices, or aerospace systems, our team is ready to help you bring your vision to life with our advanced flexible PCB manufacturing and assembly services. Contact us today to learn more about how we can support your next project and help you achieve success in the rapidly evolving world of electronics. We provide the best manufacturing services on the market.