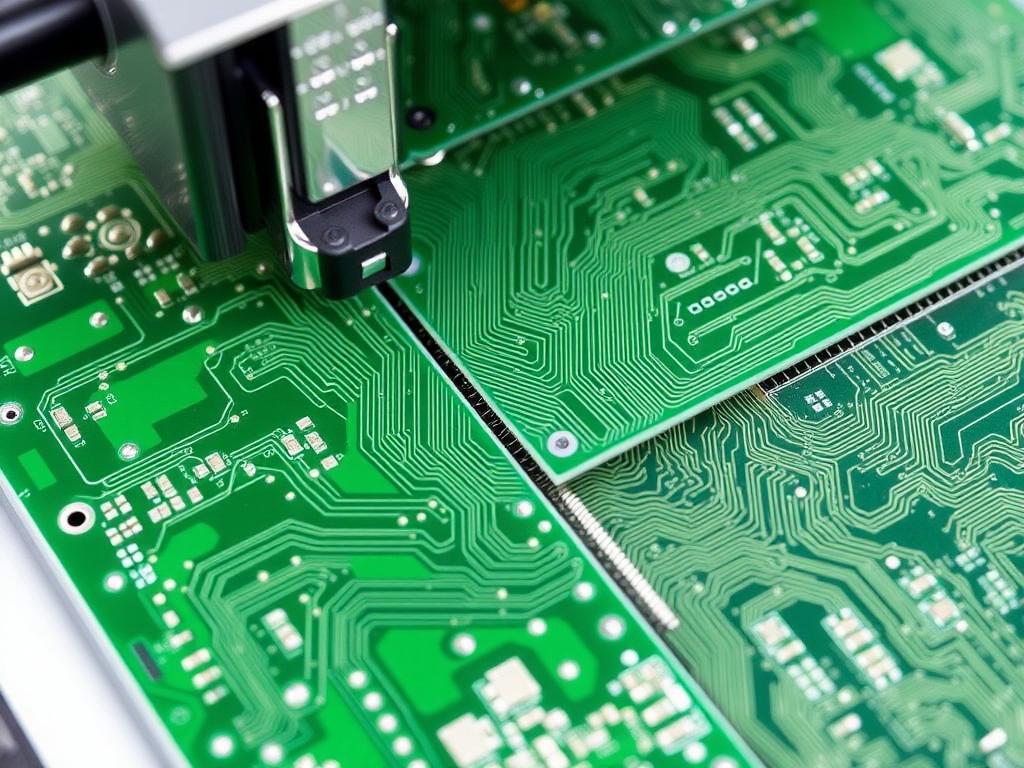
V-Nut-PCB-Nuttrennung
Effizientes PCB-Depaneling: Revolutionäre Leiterplattentrennung 🛠️
In der schnelllebigen Welt der Elektronikfertigung sind Effizienz und Präzision von größter Bedeutung. Das PCB-Depaneling, also das Trennen einzelner Leiterplatten (PCBs) von einem größeren Panel, spielt eine entscheidende Rolle bei der Gewährleistung einer qualitativ hochwertigen Produktion. Dieser Artikel befasst sich mit den Feinheiten des PCB-Depanelings, untersucht fortschrittliche Depaneling-Maschinen, innovative V-Cut- und V-Groove-Techniken und zeigt, wie Branchenführer wie Manncorp Inc. die Zukunft der PCB-Herstellung gestalten. Egal, ob Sie ein erfahrener Ingenieur oder ein Neuling in der PCB-Herstellung sind, das Verständnis dieser Prozesse ist für die Optimierung Ihres Fertigungsablaufs unerlässlich.
Was ist PCB-Depaneling und warum ist es wichtig?
PCB-Depaneling ist der kritische Prozess, bei dem einzelne Leiterplatten von einem größeren Fertigungspanel getrennt werden. Während des Herstellungsprozesses werden häufig mehrere Leiterplatten gleichzeitig auf einem einzigen Panel hergestellt, um die Effizienz zu maximieren und die Kosten zu senken. Nach Abschluss der Herstellung müssen diese Leiterplatten präzise und effizient getrennt werden, ohne Schäden zu verursachen.
Das Depaneling ist unerlässlich, da es sicherstellt, dass jede Leiterplatte ihre Integrität und Funktionalität behält. Eine effiziente Leiterplattentrennung minimiert die mechanische Belastung der Platten und verringert das Risiko von Brüchen oder Defekten. Diese Präzision ist entscheidend, um hohe Qualitätsstandards einzuhalten und sicherzustellen, dass die Endprodukte in ihren vorgesehenen Anwendungen zuverlässig funktionieren.
Darüber hinaus trägt effektives Depaneling zum Gesamtdurchsatz des Herstellungsprozesses bei. Durch den Einsatz moderner Depaneling-Maschinen und -Techniken können Hersteller schnellere Trennzeiten erreichen und so die Produktivität steigern und enge Produktionspläne einhalten.
Arten von PCB-Depaneling-Methoden: Welche ist für Ihre Anforderungen geeignet?
Es stehen mehrere Depaneling-Methoden zur Verfügung, jede mit ihren eigenen Vorteilen und Einschränkungen. Die Wahl der Depaneling-Methode hängt von verschiedenen Faktoren ab, darunter der Art der Leiterplatte, dem Produktionsvolumen und der gewünschten Präzision.
Säge-Nutzentrennung
Eine der gängigsten Methoden ist das Trennen mit einer Säge, bei dem ein Sägeblatt zum Durchtrennen der Leiterplatte verwendet wird. Diese Methode eignet sich für eine Produktion mit hohem Durchsatz und kann große Plattengrößen verarbeiten. Allerdings kann es dabei zu mechanischer Belastung kommen, die die Integrität empfindlicher Leiterplatten beeinträchtigen kann.
V-Cut Nutzentrenner
Beim V-Cut-Depaneling wird eine V-förmige Nut in die Leiterplattenplatte eingebracht, sodass die einzelnen Platten mit minimaler mechanischer Belastung auseinandergerissen werden können. Diese Methode ist ideal für dünne und flexible Leiterplatten, da sie das Risiko von Rissen oder Brüchen während der Trennung verringert.
Stanz-Nutzentrennung
Beim Punch-Depaneling wird ein Stanz- und Matrizensystem verwendet, um präzise Löcher in die Leiterplatte zu bohren und so eine einfache Trennung zu ermöglichen. Diese Methode ist hochpräzise und eignet sich für komplexe Leiterplattendesigns. Sie minimiert außerdem die mechanische Belastung und gewährleistet eine qualitativ hochwertige Trennung.
Laser-Nutzentrennen
Beim Laser-Depaneling wird ein Laserstrahl verwendet, um die Leiterplatte mit hoher Präzision zu durchtrennen. Diese Methode bietet eine hervorragende Genauigkeit und eignet sich für komplizierte Leiterplattendesigns. Sie reduziert außerdem die mechanische Belastung und ist daher ideal für hochdichte und flexible Leiterplatten.
Jede Depaneling-Methode hat ihre eigenen Vorteile und die Wahl hängt von den spezifischen Anforderungen Ihres PCB-Herstellungsprozesses ab. Das Verständnis dieser Methoden hilft bei der Auswahl der am besten geeigneten Technik, um eine effiziente und präzise PCB-Trennung zu gewährleisten.
Wie verbessern Depaneling-Maschinen die Leiterplattenherstellung?
Depaneling-Maschinen spielen eine zentrale Rolle in der modernen Leiterplattenherstellung, da sie den Trennprozess automatisieren, Konsistenz gewährleisten und die Gesamteffizienz verbessern. Diese Maschinen sind für verschiedene Depaneling-Methoden wie Säge-, V-Schnitt- und Stanz-Depaneling ausgelegt und bieten Herstellern Vielseitigkeit.
Erhöhter Durchsatz
Depaneling-Maschinen erhöhen den Durchsatz des Herstellungsprozesses erheblich. Durch die Automatisierung der Trennung können diese Maschinen große Mengen an Leiterplatten schnell und präzise verarbeiten und so den Zeitaufwand für das manuelle Depaneling reduzieren.
Präzision und Konsistenz
Einer der Hauptvorteile von Depaneling-Maschinen ist die Präzision, die sie bieten. Diese Maschinen sind mit fortschrittlichen Steuerungssystemen ausgestattet, die sicherstellen, dass jeder Schnitt gleichmäßig und präzise ist, wodurch das Risiko von Defekten minimiert und hochwertige Leiterplatten sichergestellt werden.
Reduzierte mechanische Belastung
Moderne Depaneling-Maschinen sind so konzipiert, dass die mechanische Belastung der Leiterplatten während der Trennung minimiert wird. Techniken wie V-Nut- und Stanz-Depaneling sorgen dafür, dass die einzelnen Leiterplatten sauber und ohne Beschädigung getrennt werden, was die Zuverlässigkeit der Endprodukte erhöht.
Verbesserte Sicherheit
Nutzentrenner verbessern die Sicherheit am Arbeitsplatz, indem sie den Trennvorgang automatisieren. Dadurch wird der Bedarf an manuellen Eingriffen reduziert und das Risiko von Unfällen und Verletzungen, die mit manuellen Nutzentrennmethoden verbunden sind, verringert.
Insgesamt rationalisieren Depaneling-Maschinen den PCB-Herstellungsprozess und verbessern Produktivität, Qualität und Sicherheit.
V-Schnitt vs. V-Nut: Die Unterschiede verstehen
V-Cut und V-Groove sind zwei beliebte Depaneling-Techniken, die bei der Leiterplattenherstellung verwendet werden. Obwohl bei beiden Methoden eine V-förmige Nut in der Leiterplatte erzeugt wird, gibt es wichtige Unterschiede, die ihre Eignung für unterschiedliche Anwendungen beeinflussen.
V-Cut Nutzentrenner
Beim V-Cut-Depaneling wird ein V-förmiger Schnitt entlang der Kanten der einzelnen Leiterplatten innerhalb des Nutzens vorgenommen. Dadurch können die Platinen mit minimaler mechanischer Belastung leicht auseinandergerissen werden. Der V-Cut ist ideal für dünne und flexible Leiterplatten, da er das Risiko von Rissen oder Brüchen während der Trennung verringert.
V-Nut-Nuttrennung
Beim V-Groove-Depaneling hingegen werden tiefere und präzisere Rillen erzeugt, die eine saubere und genaue Trennung der Leiterplatten ermöglichen. Diese Methode eignet sich besonders für hochdichte und mehrschichtige Leiterplatten, bei denen Präzision entscheidend ist, um die Integrität der Platten zu erhalten.
Wichtige Unterschiede
- Tiefe der Nut: Beim V-Groove-Depaneling werden im Vergleich zum V-Cut-Depaneling typischerweise tiefere Rillen verwendet, was eine bessere Trennung bei komplexen PCB-Designs ermöglicht.
- Präzision: Das V-Groove-Depaneling bietet eine höhere Präzision und eignet sich daher für Leiterplatten mit hoher Dichte und komplizierten Mustern.
- Mechanische Beanspruchung: Beide Methoden zielen darauf ab, die mechanische Belastung zu reduzieren, aber das V-Groove-Depaneling ermöglicht einen kontrollierteren Trennvorgang und sorgt so für eine minimale Belastung der Platten.
Die Wahl zwischen V-Cut- und V-Groove-Depaneling hängt von den spezifischen Anforderungen Ihres PCB-Designs und Herstellungsprozesses ab. V-Cut ist für einfachere, flexible PCBs vorzuziehen, während V-Groove besser für komplexe, hochdichte Platinen geeignet ist.
Auswahl der richtigen PCB-Depaneling-Maschine: Wichtige Überlegungen
Die Auswahl der geeigneten PCB-Nutzentrennmaschine ist entscheidend für die Optimierung Ihres Herstellungsprozesses. Hier sind die wichtigsten Faktoren, die Sie bei der Auswahl einer Nutzentrennmaschine berücksichtigen sollten:
Kompatibilität der Depaneling-Methode
Stellen Sie sicher, dass die Depaneling-Maschine die für Ihre Leiterplatten geeigneten Depaneling-Methoden unterstützt, z. B. V-Schnitt, V-Nut, Säge oder Stanzdepaneling. Die Vielseitigkeit bei der Handhabung verschiedener Methoden kann die Flexibilität Ihres Herstellungsprozesses erhöhen.
Durchsatz und Geschwindigkeit
Berücksichtigen Sie bei der Auswahl einer Depaneling-Maschine das Produktionsvolumen und den erforderlichen Durchsatz. Maschinen mit höherer Geschwindigkeit und Kapazität können große Mengen effizient verarbeiten, wodurch die Produktionszeit verkürzt und die Gesamtproduktivität erhöht wird.
Präzision und Genauigkeit
Beim PCB-Depaneling ist Präzision entscheidend, um die Integrität der Platinen zu erhalten. Wählen Sie eine Depaneling-Maschine, die hohe Genauigkeit und Konsistenz bei Schnitten bietet, das Risiko von Defekten minimiert und hochwertige PCBs gewährleistet.
Benutzerfreundlichkeit und Wartung
Entscheiden Sie sich für benutzerfreundliche und wartungsfreundliche Depaneling-Maschinen. Funktionen wie automatische Einstellungen, einfacher Wartungszugriff und benutzerfreundliche Schnittstellen können den Betrieb vereinfachen und Ausfallzeiten reduzieren.
Kosten und Kapitalrendite
Bewerten Sie die Kosten der Depaneling-Maschine im Verhältnis zu ihren Funktionen und Vorteilen. Berücksichtigen Sie den Return on Investment (ROI), indem Sie beurteilen, wie die Maschine die Effizienz steigert, Mängel reduziert und die allgemeine Produktionsqualität verbessert.
Markenreputation und -unterstützung
Wählen Sie Depaneling-Maschinen von renommierten Marken wie Manncorp Inc., die für ihre Zuverlässigkeit und Kundenbetreuung bekannt sind. Guter Kundendienst und die Verfügbarkeit von Ersatzteilen sind für die Aufrechterhaltung der Leistung und Langlebigkeit der Maschine unerlässlich.
Durch sorgfältige Berücksichtigung dieser Faktoren können Sie die richtige PCB-Depaneling-Maschine auswählen, die Ihren Fertigungsanforderungen entspricht und Ihre Produktionskapazitäten verbessert.
Die Rolle von Routern beim PCB-Depaneling
Fräser sind integrale Komponenten von PCB-Nutzentrennungsmaschinen und sind für die Ausführung präziser Schnitte entlang der Leiterplatte verantwortlich. Sie spielen eine entscheidende Rolle bei der genauen und effizienten Trennung einzelner Platinen.
Arten von PCB-Routern
Beim PCB-Depaneling werden hauptsächlich zwei Arten von Fräsern verwendet: CNC-Fräser und manuelle Fräser.
- CNC-Fräser: CNC-Fräser (Computer Numerical Control) bieten hohe Präzision und Automatisierung und sind daher ideal für umfangreiche und komplexe PCB-Depaneling-Aufgaben. Sie sind mit fortschrittlichen Steuerungssystemen ausgestattet, die gleichmäßige und präzise Schnitte gewährleisten.
- Manuelle Router: Manuelle Fräser erfordern bei jedem Schnitt ein Eingreifen des Bedieners und bieten Flexibilität für das Depaneling kleiner oder kundenspezifischer Leiterplatten. Obwohl sie weniger automatisiert sind als CNC-Fräser, eignen sie sich für Projekte, die häufige Anpassungen erfordern.
Fräser und Werkzeuge
Die Wahl der Fräser ist entscheidend für ein präzises Depaneling. Hochwertige Fräser, wie Rundfräser mit V-Schnitt und Sägeblatt-Fräser mit V-Nut, sorgen für saubere und präzise Schnitte und minimieren die mechanische Belastung der Leiterplatten.
- Rundklinge V-Schnitt: Ideal zum Erstellen flacher Rillen, geeignet für dünne und flexible Leiterplatten.
- Sägeblatt V-Nut: Geeignet für tiefere Rillen und Leiterplatten mit hoher Dichte und bietet verbesserte Präzision.
Steigerung der Effizienz beim Nutzentrennen
Fräser tragen zur Effizienz des Depaneling-Prozesses bei, indem sie schnelle und präzise Schnitte ermöglichen. Moderne Frässysteme wie die V-Groove-PCB-Depaneling-Maschine CY-203 enthalten motorisierte Fräser, die den Schneideprozess automatisieren, den Durchsatz erhöhen und die manuelle Arbeit reduzieren.
Minimierung mechanischer Belastungen
Richtige Frästechniken minimieren die mechanische Belastung der Leiterplatten während der Trennung. V-Nut- und V-Cut-Fräsen stellen sicher, dass die Platten sauber getrennt werden, ohne dass Brüche oder Defekte entstehen, und dass die Integrität jeder Leiterplatte erhalten bleibt.
Durch die Integration hochwertiger Router in Ihren PCB-Depaneling-Prozess verbessern Sie Präzision, Effizienz und Zuverlässigkeit und tragen so zur Gesamtqualität Ihrer Leiterplatten bei.
Häufige Herausforderungen beim PCB-Depaneling und wie man sie bewältigt
Das Depaneling von Leiterplatten ist zwar unerlässlich, bringt aber mehrere Herausforderungen mit sich, die Hersteller bewältigen müssen, um eine effiziente und qualitativ hochwertige Trennung zu gewährleisten. Das Verstehen dieser Herausforderungen und die Implementierung effektiver Lösungen kann den Depaneling-Prozess erheblich verbessern.
Mechanische Belastung und PCB-Schäden
Eine der größten Herausforderungen beim Depaneling von Leiterplatten besteht darin, die mechanische Belastung zu minimieren, um Schäden an den Leiterplatten zu vermeiden. Unsachgemäßes Depaneling kann zu Rissen, Brüchen oder Delamination führen und so die Funktionalität der Leiterplatten beeinträchtigen.
Lösung: Nutzen Sie moderne Depaneling-Methoden wie V-Groove und V-Cut, die die mechanische Belastung reduzieren, indem sie ein sauberes Auseinanderbrechen der Platten ermöglichen. Die Investition in hochpräzise Depaneling-Maschinen mit motorisierten Fräsern gewährleistet gleichmäßige und präzise Schnitte und minimiert das Risiko von Beschädigungen weiter.
Präzision und Genauigkeit
Um die Integrität der Leiterplatten zu erhalten, ist es entscheidend, beim Depaneling eine hohe Präzision und Genauigkeit zu erreichen. Ungenaue Schnitte können zu falsch ausgerichteten Leiterplatten führen, was die Montage und Prüfung erschwert.
Lösung: Implementieren Sie CNC-Nutzentrennungsmaschinen, die mit fortschrittlichen Steuerungssystemen und hochwertigen Fräsern ausgestattet sind. Regelmäßige Kalibrierung und Wartung der Nutzentrennungsmaschinen stellen sicher, dass die Schnitte präzise und konsistent bleiben, wodurch die Wahrscheinlichkeit von Fehlern verringert wird.
Durchsatz und Produktionsgeschwindigkeit
Das genaue Ausbalancieren von Durchsatz und Produktionsgeschwindigkeit kann eine Herausforderung sein, insbesondere in Produktionsumgebungen mit hohem Volumen. Langsame Depaneling-Prozesse können die Produktion verlangsamen, während zu schnelle Prozesse die Qualität beeinträchtigen können.
Lösung: Wählen Sie Depaneling-Maschinen, die ein Gleichgewicht zwischen Geschwindigkeit und Präzision bieten. Maschinen wie die V-Groove PCB-Depaneling-Maschine CY-203 sind für das Depaneling mit hohem Durchsatz ohne Einbußen bei der Genauigkeit ausgelegt. Darüber hinaus kann die Optimierung des Depaneling-Workflows und die Reduzierung manueller Eingriffe die Gesamtproduktionsgeschwindigkeit verbessern.
Handhabung komplexer PCB-Designs
Moderne Leiterplatten weisen häufig komplizierte Designs mit mehreren Schichten und Komponenten auf, was das Depaneling komplexer macht. Um eine saubere Trennung zu gewährleisten, ohne empfindliche Elemente zu beschädigen, sind fortschrittliche Depaneling-Techniken erforderlich.
Lösung: Verwenden Sie Depaneling-Maschinen mit vielseitigen Schneidwerkzeugen, die komplexe PCB-Designs verarbeiten können. Laser-Depaneling beispielsweise bietet hohe Präzision für komplizierte Muster, während Stanz-Depaneling mehrschichtige PCBs präzise trennen kann, ohne mechanische Belastung zu verursachen.
Kostenüberlegungen
Die Investition in moderne Nutzentrennmaschinen und die Aufrechterhaltung einer hohen Präzision können kostspielig sein und die Hersteller vor große Budgetprobleme stellen.
Lösung: Bewerten Sie die langfristigen Vorteile einer Investition in hochwertige Depaneling-Maschinen, wie z. B. geringere Fehlerraten und höhere Produktionseffizienz. Ziehen Sie außerdem Maschinen in Betracht, die Depaneling-Funktionen für mehrere Methoden bieten, um Flexibilität zu bieten und die Kapitalrendite zu maximieren.
Indem sie diese häufigen Herausforderungen mit effektiven Lösungen angehen, können Hersteller ihre PCB-Depaneling-Prozesse optimieren und so eine qualitativ hochwertige Produktion und Betriebseffizienz sicherstellen.
Innovationen im PCB-Nutzentrennen: Die Zukunft der Nutzentrennmaschinen
Der Bereich des PCB-Nutzentrennens entwickelt sich ständig weiter, angetrieben durch technologische Fortschritte und die zunehmende Komplexität von PCB-Designs. Innovationen bei Nutzentrennern verbessern Präzision, Effizienz und Vielseitigkeit und prägen die Zukunft der PCB-Herstellung.
Automatisierung und Motorisierung
Moderne Depaneling-Maschinen integrieren zunehmend Automatisierung und Motorisierung, um Durchsatz und Konsistenz zu verbessern. Motorisierte PCB-Depaneling-Maschinen, wie die V-Groove-PCB-Depaneling-Maschine CY-203, bieten automatisierte Schneidprozesse, die manuelle Arbeit reduzieren und die Präzision verbessern.
Fortgeschrittene Schneidetechniken
Innovative Schneidetechniken wie Laser-Depaneling und Mehrmesser-Depaneling erfreuen sich aufgrund ihrer hohen Präzision und Fähigkeit, komplexe Leiterplattendesigns zu verarbeiten, zunehmender Beliebtheit. Das Laser-Depaneling beispielsweise ermöglicht saubere und präzise Schnitte ohne mechanische Belastung und ist daher ideal für hochdichte und flexible Leiterplatten.
Intelligente Nutzentrennsysteme
Durch die Integration intelligenter Technologien, darunter Sensoren und Algorithmen für maschinelles Lernen, können sich Depaneling-Maschinen an unterschiedliche PCB-Designs und -Bedingungen anpassen. Diese intelligenten Systeme können die Schneidparameter automatisch anpassen, um den Depaneling-Prozess zu optimieren, eine gleichbleibende Qualität sicherzustellen und den Bedarf an manuellen Eingriffen zu reduzieren.
Verbesserte Depaneling-Tools
Fortschritte bei Depaneling-Werkzeugen wie Hochgeschwindigkeitsfräsen und Präzisionssägeblättern verbessern die Genauigkeit und Effizienz von Depaneling-Maschinen. Hochwertige Schneidwerkzeuge minimieren Verschleiß und sorgen für eine lange Schnittpräzision und senken die Wartungskosten.
Umweltfreundliche Depaneling-Lösungen
Nachhaltigkeit wird zu einem zentralen Thema in der Leiterplattenherstellung, und Depaneling-Maschinen werden weiterentwickelt, um umweltfreundliche Verfahren zu unterstützen. Innovationen wie effiziente Staubabsaugsysteme und energieeffiziente Motoren reduzieren die Umweltauswirkungen von Depaneling-Prozessen und stehen im Einklang mit Initiativen für umweltfreundliche Fertigung.
Anpassbare Depaneling-Lösungen
Hersteller suchen zunehmend nach anpassbaren Depaneling-Lösungen, die auf spezifische PCB-Designs und Produktionsanforderungen zugeschnitten werden können. Depaneling-Maschinen mit modularem Design und anpassbaren Einstellungen bieten die nötige Flexibilität, um eine breite Palette von PCB-Typen und Fertigungsszenarien zu verarbeiten.
Diese Innovationen führen dazu, dass die Depaneling-Branche immer effizientere, präzisere und vielseitigere Lösungen entwickelt, die den wachsenden Anforderungen der modernen Leiterplattenherstellung gerecht werden.
Fallstudie: Der Einfluss von Manncorp Inc. auf die PCB-Depaneling-Technologie
Manncorp Inc., ein führender Hersteller in der PCB-Depaneling-Branche, ist an der Spitze des technologischen Fortschritts und revolutioniert den Depaneling-Prozess mit seinen hochmodernen Maschinen und innovativen Lösungen.
Hochmoderne Nutzentrennmaschinen
Manncorp Inc. bietet eine Reihe von PCB-Depaneling-Maschinen an, die auf die unterschiedlichsten Fertigungsanforderungen zugeschnitten sind. Ihre Flaggschiffmodelle, wie die GAM 380AT PCB Bottom Depaneling Machine und die ZM30-ASV Fully Automatic Saw-Type V-Groove PCB Depaneling Machine, zeigen ihr Engagement für Präzision und Effizienz. Diese Maschinen verfügen über fortschrittliche V-Groove- und V-Cut-Techniken, die eine saubere und genaue Trennung einzelner PCBs bei minimaler mechanischer Belastung gewährleisten.
Technologische Innovationen
Manncorp Inc. investiert kontinuierlich in Forschung und Entwicklung, um innovative Depaneling-Technologien einzuführen. Die Einführung von Laser-Depaneling-Maschinen wie der DirectLaser H5 PCB-FPC-Laserschneidmaschine ist ein Beispiel für ihr Engagement, hochpräzise und effiziente Depaneling-Lösungen anzubieten. Diese Lasermaschinen bieten höchste Genauigkeit und sind daher ideal für komplexe und hochdichte PCB-Designs.
Kundenorientierte Lösungen
Manncorp Inc. kennt die vielfältigen Bedürfnisse von Leiterplattenherstellern und bietet anpassbare Depaneling-Lösungen, die auf spezifische Anforderungen zugeschnitten sind. Die Depaneling-Systeme sind so konzipiert, dass sie sich nahtlos in bestehende Fertigungsabläufe integrieren lassen, die Produktivität steigern und Ausfallzeiten reduzieren. Darüber hinaus bietet Manncorp Inc. umfassenden Support und Schulungen an, damit die Kunden den Nutzen ihrer Depaneling-Maschinen maximieren können.
Engagement für Qualität und Zuverlässigkeit
Manncorp Inc. legt bei seinen Depaneling-Maschinen Wert auf Qualität und Zuverlässigkeit. Jede Maschine wird strengen Tests unterzogen, um sicherzustellen, dass sie hohe Leistungs- und Haltbarkeitsstandards erfüllt. Der Fokus auf Qualität stellt sicher, dass die Kunden zuverlässige Maschinen erhalten, die konsistente und genaue Depaneling-Ergebnisse liefern und so zum Gesamterfolg ihrer PCB-Herstellungsvorgänge beitragen.
Branchenführerschaft und Einfluss
Die Innovationen von Manncorp Inc. haben die PCB-Depaneling-Branche erheblich beeinflusst und neue Maßstäbe in puncto Effizienz und Präzision gesetzt. Dank ihrer fortschrittlichen Depaneling-Maschinen konnten Hersteller einen höheren Durchsatz erzielen, die Fehlerquote senken und die Qualität ihrer PCBs verbessern. Als Vorreiter in der Depaneling-Technologie hat sich Manncorp Inc. als zuverlässiger Partner im PCB-Herstellungssektor etabliert.
Die Beiträge von Manncorp Inc. zur PCB-Depaneling-Technologie unterstreichen die Bedeutung von Innovation und Qualität für den Fortschritt in der Branche. Ihre innovativen Lösungen prägen weiterhin die Zukunft der PCB-Herstellung und bieten Herstellern die Werkzeuge, die sie für Spitzenleistungen benötigen.
Angebot anfordern: So wählen Sie die beste Depaneling-Lösung für Ihr Unternehmen aus
Die Auswahl der richtigen Depaneling-Lösung ist entscheidend für die Optimierung Ihres PCB-Herstellungsprozesses. Egal, ob Sie ein Kleinhersteller oder ein Großunternehmen sind, der Erwerb einer maßgeschneiderten Depaneling-Maschine, die Ihren spezifischen Anforderungen entspricht, kann Ihre Produktionseffizienz und Produktqualität erheblich steigern. Hier erfahren Sie, wie Sie ein Angebot anfordern und die beste Depaneling-Lösung für Ihr Unternehmen auswählen können.
Bewerten Sie Ihre Fertigungsanforderungen
Bevor Sie ein Angebot anfordern, müssen Sie unbedingt Ihre Fertigungsanforderungen ermitteln. Berücksichtigen Sie Faktoren wie:
- Produktionsvolumen: Bestimmen Sie Ihre durchschnittlichen und Spitzenproduktionsmengen, um eine Nutzentrennmaschine auszuwählen, die Ihren Durchsatzanforderungen gerecht wird.
- PCB-Komplexität: Bewerten Sie die Komplexität Ihrer PCB-Designs, einschließlich der Anzahl der Schichten und des Vorhandenseins empfindlicher Komponenten, um eine Maschine auszuwählen, die präzises und zuverlässiges Depaneling ermöglicht.
- Depaneling-Methode: Identifizieren Sie die Depaneling-Methoden, die am besten zu Ihren Leiterplatten passen, sei es V-Schnitt, V-Nut, Säge oder Laser-Depaneling.
Anbieter von Nutzentrennmaschinen recherchieren
Recherchieren Sie nach seriösen Anbietern von Depaneling-Maschinen wie Manncorp Inc., die für ihre fortschrittliche Technologie und zuverlässigen Lösungen bekannt sind. Suchen Sie nach Anbietern, die eine Reihe von Maschinen für unterschiedliche Depaneling-Methoden und Produktionsgrößen anbieten. Lesen Sie Kundenberichte und Fallstudien, um die Wirksamkeit und Zuverlässigkeit ihrer Maschinen einzuschätzen.
Kontaktieren Sie Anbieter und fordern Sie ein Angebot an
Kontaktieren Sie ausgewählte Anbieter von Depaneling-Maschinen und fordern Sie ein detailliertes Angebot an. Geben Sie bei der Angebotsanfrage umfassende Informationen zu Ihren Fertigungsanforderungen an, darunter:
- PCB-Spezifikationen: Geben Sie Details zu den Größen, Typen und Designs Ihrer Leiterplatten weiter, damit die Anbieter die am besten geeigneten Maschinen empfehlen können.
- Anforderungen an das Nutzentrennen: Geben Sie Ihre bevorzugten Depaneling-Methoden und alle spezifischen Funktionen an, die Sie benötigen, wie z. B. Automatisierung, Präzision oder hoher Durchsatz.
- Budgetbeschränkungen: Skizzieren Sie Ihr Budget, um sicherzustellen, dass das Angebot Ihren finanziellen Erwartungen entspricht.
Angebote auswerten und Funktionen vergleichen
Sobald Sie Angebote erhalten haben, bewerten Sie diese anhand der folgenden Kriterien:
- Maschinenspezifikationen: Vergleichen Sie die Spezifikationen der einzelnen Maschinen, einschließlich Schnittpräzision, Durchsatzkapazität und unterstützte Depaneling-Methoden.
- Gesamtbetriebskosten: Berücksichtigen Sie nicht nur die Anschaffungskosten, sondern auch die langfristigen Kosten für Wartung, Betrieb und Support.
- Kundendienst: Bewerten Sie den Umfang des bereitgestellten After-Sales-Supports, einschließlich Schulungen, Wartungsdienste und Verfügbarkeit von Ersatzteilen.
Treffen Sie eine fundierte Entscheidung
Wählen Sie auf Grundlage Ihrer Bewertung die Depaneling-Maschine aus, die Ihren Anforderungen am besten entspricht und das beste Preis-Leistungs-Verhältnis bietet. Stellen Sie sicher, dass der Anbieter die Maschine innerhalb Ihres Zeitrahmens liefern kann und zuverlässigen Support bietet, um eine nahtlose Integration in Ihren Herstellungsprozess zu ermöglichen.
Wenn Sie diese Schritte befolgen, können Sie effektiv ein Angebot anfordern und die beste Depaneling-Lösung auswählen, die die Effizienz Ihrer PCB-Herstellung und die Produktqualität verbessert.
Die wichtigsten Erkenntnisse
- PCB-Nutzentrennung ist wichtig, um einzelne Leiterplatten beschädigungsfrei von einem größeren Panel zu trennen.
- Nutzentrenner Verbessern Sie die Fertigung, indem Sie Durchsatz und Präzision steigern und die mechanische Belastung reduzieren.
- V-Schnitt vs. V-Nut: Der V-Schnitt ist ideal für dünne, flexible Leiterplatten, während die V-Nut eine höhere Präzision für komplexe Platten mit hoher Dichte bietet.
- Auswahl der richtigen Maschine Dabei werden Depaneling-Methoden, Durchsatz, Präzision, Benutzerfreundlichkeit, Kosten und der Ruf der Marke berücksichtigt.
- Router spielen eine entscheidende Rolle bei der präzisen und effizienten Leiterplattentrennung.
- Häufige Herausforderungen Dazu gehören mechanische Belastung, Präzision, Durchsatz, Handhabung komplexer Designs und Kostenüberlegungen.
- Innovationen Bei Nutzentrennmaschinen liegt der Schwerpunkt auf Automatisierung, fortschrittlichen Schneidetechniken, intelligenten Systemen, verbesserten Werkzeugen, umweltfreundlichen Lösungen und individueller Anpassung.
- Manncorp Inc. ist mit seinen hochmodernen Nutzentrennmaschinen und seinem Qualitätsbewusstsein ein Musterbeispiel für Branchenführerschaft.
- Angebot anfordern Dazu gehört die Ermittlung Ihres Bedarfs, die Recherche nach Anbietern, die Kontaktaufnahme mit ihnen mit detaillierten Anforderungen, die Auswertung von Angeboten und das Treffen einer fundierten Entscheidung.
Durch das Verständnis der verschiedenen Aspekte des PCB-Depanelings und die Nutzung fortschrittlicher