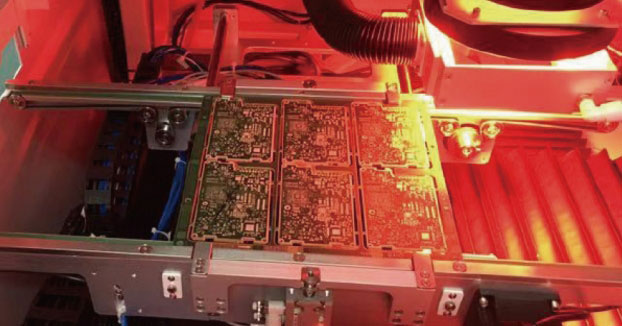
Herstellung von Maschinen zum Laserschneiden von Leiterplatten steigert die Produktionskapazität um 30 %
Einführung
In der sich ständig weiterentwickelnden Welt der Elektronikfertigung sind Präzision, Effizienz und Anpassung von entscheidender Bedeutung. Ein Bereich, in dem diese Elemente zusammenlaufen, ist die Verwendung von Laserschneiden von Leiterplatten. Da die Branche die Grenzen der Miniaturisierung und Komplexität erweitert, wurden traditionelle Methoden des PCB-Depanelings nach und nach durch die Lasertechnologie ersetzt, die unübertroffene Präzision und Vielseitigkeit bietet. Dieser Artikel befasst sich mit den Feinheiten des Laserschneidens von Leiterplatten, untersucht seine Anwendungen, Vorteile und wie es die PCB-Prototyping- und Produktionslandschaft revolutioniert.
Inhaltsverzeichnis
Der Aufstieg des Laserschneidens in der Leiterplattenherstellung
Das Laserschneiden hat den Herstellungsprozess von Leiterplatten grundlegend verändert. Im Gegensatz zu mechanischen Methoden wie Fräsen oder Stanzen wird beim Laserschneiden ein fokussierter Lichtstrahl zum Schneiden oder Gravieren von Materialien verwendet. Diese Methode ermöglicht äußerst präzise Schnitte mit minimaler thermischer Belastung der Komponenten und gewährleistet so die Integrität empfindlicher Schaltkreise.
Das Laserschneiden von Leiterplatten ist besonders in der Prototyping-Phase von Vorteil. Angesichts der steigenden Nachfrage nach kundenspezifischem PCB-Prototyping benötigen Hersteller eine Methode, die eine schnelle und genaue Produktion ermöglicht. Die Möglichkeit, Designs schnell zu iterieren, ohne dass teure und zeitaufwändige Werkzeugwechsel erforderlich sind, ist ein wesentlicher Vorteil der Lasertechnologie.
Beispielsweise kann ein Prototyping-Laserschneider nahtlos von einem Design zum anderen wechseln, was ihn ideal für kurze Produktionsläufe macht oder wenn mehrere Iterationen erforderlich sind, um ein Design zu perfektionieren. Diese Flexibilität ist ein Hauptgrund dafür, warum Laserschneiden zur bevorzugten Methode für kundenspezifisches PCB-Prototyping geworden ist.
Vorteile des Laserschneidens für Leiterplatten
- Präzision und Genauigkeit
Laserschneider können Schnitte mit Toleranzen von bis zu ±0,01 mm erzielen, was sie ideal für komplizierte Leiterplattendesigns macht. Diese Präzision ist besonders wertvoll bei der Arbeit mit High-Density-Interconnect-Leiterplatten (HDI), bei denen der Platz knapp ist und selbst die kleinste Fehlausrichtung zu einer Fehlfunktion führen kann. - Reduzierte thermische Belastung
Bei herkömmlichen Schneideverfahren entsteht häufig Hitze, die empfindliche Bauteile beschädigen oder Verformungen verursachen kann. Beim Laserschneiden wird dieses Risiko minimiert, indem die Hitze auf einen kleinen Bereich konzentriert wird, wodurch die Wahrscheinlichkeit einer thermischen Verformung verringert wird. - Vielseitigkeit
Ob Sie mit starren, flexiblen oder starr-flexiblen Leiterplatten arbeiten, das Laserschneiden kann eine große Bandbreite an Materialien und Stärken verarbeiten. Diese Vielseitigkeit macht es zu einem unverzichtbaren Werkzeug bei der Herstellung moderner elektronischer Geräte. - Geschwindigkeit und Effizienz
Laserschneiden ist nicht nur präzise, sondern auch schnell. Die Fähigkeit, komplexe Formen und mehrere Schichten in einem einzigen Durchgang zu schneiden, reduziert die Produktionszeit erheblich und macht es zu einer effizienten Wahl sowohl für die Prototypenentwicklung als auch für die Fertigung im großen Maßstab. - Kein Werkzeugbedarf
Einer der größten Vorteile des Laserschneidens besteht darin, dass keine physischen Werkzeuge mehr erforderlich sind. Dies senkt nicht nur die Kosten, sondern ermöglicht auch schnellere Übergänge zwischen verschiedenen Designs, was die Produktionseffizienz weiter steigert.
Anwendungen im PCB-Prototyping
Im Bereich des PCB-Prototypings ist das Laserschneiden von unschätzbarem Wert. Der Prototyping-Laserschneider ermöglicht eine schnelle Produktion von Platinen, sodass Designer ihre Designs schnell testen und wiederholen können. Diese Fähigkeit ist besonders in Branchen wie der Luft- und Raumfahrt, der Automobilindustrie und der Unterhaltungselektronik nützlich, in denen Innovationen durch schnelle Entwicklungszyklen vorangetrieben werden.
Beim kundenspezifischen PCB-Prototyping ist häufig die Möglichkeit erforderlich, schnelle Anpassungen am Design vorzunehmen. Beim Laserschneiden können diese Änderungen im Handumdrehen vorgenommen werden, ohne dass neue Werkzeuge oder lange Rüstzeiten erforderlich sind. Diese Flexibilität beschleunigt nicht nur den Entwicklungsprozess, sondern senkt auch die Kosten, weshalb diese Methode bei Ingenieuren und Designern beliebt ist.
Laserschneiden vs. traditionelle Depaneling-Methoden
Während traditionelle Methoden wie Fräsen, Stanzen und V-Nuten ihre Vorzüge haben, bietet das Laserschneiden deutliche Vorteile, die kaum zu übersehen sind.
- Routenplanung: Das Fräsen ist zwar effektiv, kann jedoch mechanische Belastungen auf der Leiterplatte verursachen und möglicherweise zu Schäden führen. Das Laserschneiden hingegen ist ein berührungsloser Prozess, bei dem das Risiko physischer Schäden ausgeschlossen ist.
- Stanzen: Stanzen ist zwar schnell, bietet aber nicht die Präzision, die für komplexe Designs erforderlich ist. Laserschneiden bietet die Genauigkeit, die für die komplexen PCB-Layouts von heute erforderlich ist.
- V-Nuten: Diese Methode ist auf geradlinige Schnitte beschränkt, während beim Laserschneiden beliebige Formen und Muster möglich sind, was es vielseitiger macht.
Der Vergleich zeigt deutlich, dass das Laserschneiden für viele PCB-Depaneling-Anforderungen nicht nur eine Alternative, sondern eine bessere Option ist.
Umweltauswirkungen des Laserschneidens
Neben den technischen Vorteilen ist das Laserschneiden im Vergleich zu herkömmlichen Methoden auch umweltfreundlicher. Da kein physischer Kontakt erforderlich ist, entsteht kein Abfall in Form von abgenutzten Werkzeugen oder abgebrochenen Bohrern. Darüber hinaus reduziert die Präzision des Laserschneidens den Materialabfall und trägt zu einem nachhaltigeren Herstellungsprozess bei.
Für Hersteller, die ihren CO2-Fußabdruck reduzieren möchten, ist das Laserschneiden eine umweltfreundliche Lösung, die im Einklang mit dem globalen Trend zu umweltfreundlicheren Produktionsverfahren steht.
Auswahl des richtigen Laserschneiders für das PCB-Prototyping
Die Auswahl des richtigen Prototyp-Laserschneiders ist entscheidend, um die gewünschten Ergebnisse bei der Leiterplattenproduktion zu erzielen. Zu berücksichtigende Faktoren sind unter anderem der Lasertyp (CO2 oder Faser), die Leistungsabgabe, die Schnittgeschwindigkeit und die Kompatibilität mit verschiedenen Leiterplattenmaterialien. Beispielsweise werden Faserlaser im Allgemeinen bevorzugt zum Schneiden von Metallen verwendet, während CO2-Laser sich hervorragend zum Schneiden von Nichtmetallen wie den in Leiterplatten verwendeten Substraten eignen.
Hersteller müssen auch die mit dem Laserschneider mitgelieferte Software berücksichtigen. Moderne Software kann die Präzision und Effizienz des Schneideprozesses deutlich steigern und bietet Funktionen wie automatisches Verschachteln, um Materialverschwendung zu minimieren.
Abschluss
Laserschneiden ist die Zukunft der Leiterplattenherstellung. Seine Präzision, Vielseitigkeit und Effizienz machen es zu einem unverzichtbaren Werkzeug sowohl für die Prototypenentwicklung als auch für die Produktion. Da die Nachfrage nach komplexeren und miniaturisierteren elektronischen Bauteilen weiter steigt, wird die Einführung der Laserschneidtechnologie nur noch weiter zunehmen und ihren Platz als Eckpfeiler der modernen Elektronikfertigung festigen.
Weitere Informationen zum PCB-Depaneling und zur neuesten Laserschneidtechnologie finden Sie auf unserer Leiterplattentrennmaschine Seite oder erfahren Sie mehr über PCB-Laser-Nutzentrennen auf unserer Website.
FAQs
- Was ist der Hauptvorteil der Verwendung eines Laserschneiders für Leiterplatten?
Der Hauptvorteil liegt in der hohen Präzision und der minimalen thermischen Belastung der Komponenten, wodurch die Integrität komplexer Schaltkreise gewährleistet wird. - Kann das Laserschneiden sowohl für starre als auch für flexible Leiterplatten verwendet werden?
Ja, das Laserschneiden ist vielseitig und kann auf verschiedenen Materialien verwendet werden, darunter starre, flexible und starr-flexible Leiterplatten. - Ist das Laserschneiden umweltfreundlicher als herkömmliche Methoden?
Ja, beim Laserschneiden entsteht im Vergleich zu herkömmlichen Methoden weniger Abfall und es wird weniger Energie verbraucht, sodass es die nachhaltigere Wahl ist. - Welcher Lasertyp eignet sich am besten zum Schneiden von Leiterplatten?
CO2-Laser eignen sich typischerweise am besten zum Schneiden von Nichtmetallen wie PCB-Substraten, während Faserlaser besser für Metalle geeignet sind. - Wie schneidet das Laserschneiden im Vergleich zu anderen Depaneling-Methoden ab?
Das Laserschneiden bietet im Vergleich zum Fräsen, Stanzen und V-Nuten eine höhere Präzision, eine geringere thermische Belastung und eine größere Vielseitigkeit.
Zusammenfassung
Laserschneiden revolutioniert die Leiterplattenherstellung und bietet beispiellose Präzision und Effizienz. Es ist besonders in der Prototypphase von Vorteil, in der schnelle Iterationen und kundenspezifische Designs unerlässlich sind. Da sich die Branche weiterentwickelt, wird die Rolle des Laserschneidens bei der Herstellung hochwertiger, komplexer Leiterplatten wachsen und es zu einem unverzichtbaren Werkzeug für die moderne Elektronikfertigung machen.