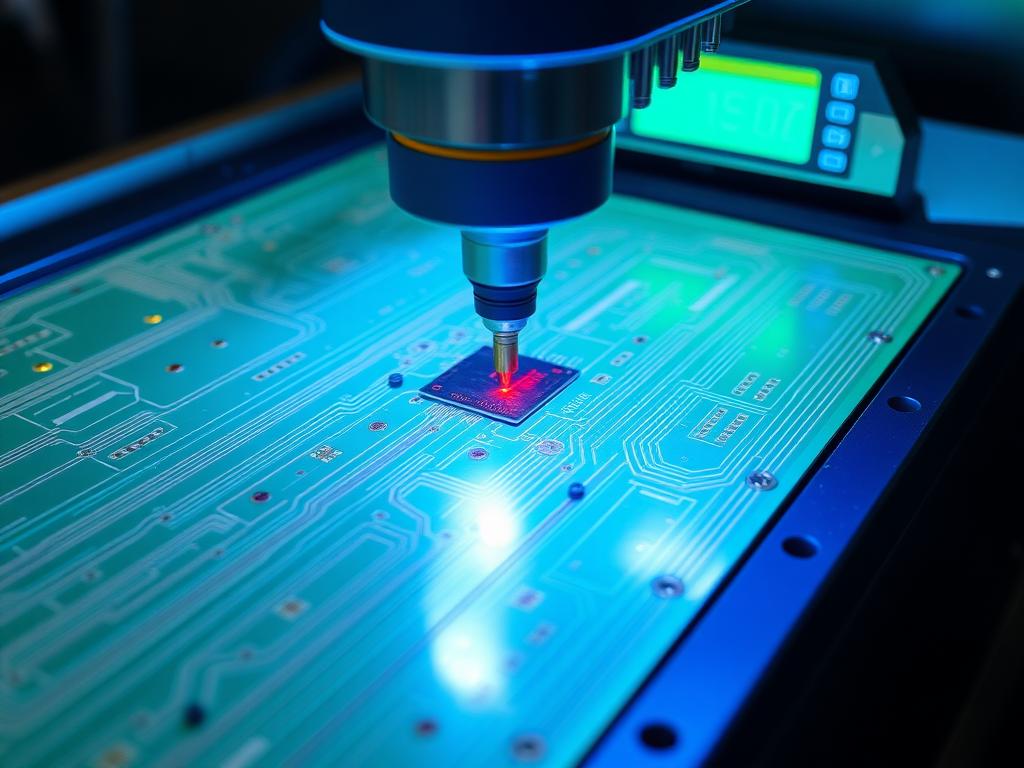
CO2 laser PCB depaneling
Choosing the Best PCB Depaneling Method: Laser vs. Router Systems
In the fast-paced world of electronics manufacturing, PCB depaneling stands as a critical step in transforming large panels into individual printed circuit boards (PCBs). This article delves into the various depaneling methods, with a spotlight on laser depaneling and router systems, to help you make an informed decision that enhances your production efficiency and product quality.
What is PCB Depaneling and Why is it Important?
PCB depaneling is the process of separating individual PCBs from a larger panel after the manufacturing process. This step is crucial for ensuring that each PCB meets quality standards before it moves on to assembly and final product integration. Efficient depaneling methods reduce mechanical stress and prevent damage to the delicate circuits, ensuring longevity and reliability of electronic products.
Laser Depaneling: An Overview
Laser depaneling utilizes precise laser beams to cut through PCBs, offering a high degree of accuracy and minimal thermal impact. This method has gained popularity due to its ability to handle complex designs and tight tolerances. By employing a CO2 laser or UV laser, manufacturers can achieve clean cuts with minimal debris, enhancing the overall quality of the final product.
How Does Laser PCB Depaneling Work?
The laser PCB depaneling process begins with the alignment of the PCB panel in the depaneling machine. A controlled laser beam is then directed along the predefined cut lines, effectively singulating the individual boards. Advanced machine vision systems ensure precision by continuously monitoring the cutting path, adjusting in real-time to maintain accuracy and consistency across each board.
Key Components:
- Laser Source: Typically a CO2 laser for its efficiency in cutting non-metallic materials like PCBs.
- Motion System: An XY motion system allows for precise movement of the laser across the panel.
- Cooling System: An air-cooled CO2 laser prevents overheating, ensuring stable operation during prolonged use.
Advantages of Laser Depaneling Over Traditional Methods
Laser depaneling offers several benefits compared to conventional mechanical methods such as routing or V-scoring:
- Precision Cutting: Achieves close tolerances and minimal debris, reducing the need for post-processing.
- Speed: Faster cutting speeds enhance throughput, allowing for higher production volumes.
- Flexibility: Capable of handling complex circuit designs, including curves and sharp corners.
- Reduced Mechanical Stress: Minimizes the risk of mechanical stress on the PCB, enhancing board integrity.
Depaneling Method | Precision | Speed | Mechanical Stress | Debris |
---|---|---|---|---|
Laser Depaneling | High | Fast | Low | Minimal |
Routing | Medium | Moderate | High | Significant |
V-Groove Scoring | Low | Slow | High | Moderate |
What is V-Groove Depaneling?
V-Groove depaneling involves scoring the PCB along the desired cut lines using a router to create V-shaped grooves. These grooves weaken the PCB, allowing for manual or mechanical snapping to separate individual boards. While cost-effective, this method is less precise and can introduce mechanical stress, potentially leading to damaged circuits.
PCB/FPC Punching Machines: When to Use Them?
PCB/FPC punching machines are ideal for applications requiring the removal of specific sections or creating custom patterns on PCBs. Unlike full panel depaneling, punching allows for selective cutting, making it suitable for specialized manufacturing needs. This method complements laser depaneling by offering versatility in handling various PCB designs.
Comparing CO2 and UV Lasers in PCB Depaneling
When choosing a laser depaneling system, the type of laser used plays a significant role:
- CO2 Lasers:
- Advantages: Efficient for cutting non-metallic materials, cost-effective, and widely available.
- Applications: Ideal for standard PCB materials and large-scale production.
- UV Lasers:
- Advantages: Higher precision with minimal thermal impact, suitable for sensitive circuits.
- Applications: Best for high-density interconnects and fine-pitch components.
Choosing between CO2 and UV lasers depends on the specific requirements of your PCB designs and the level of precision needed.
How Machine Vision Enhances PCB Cutting Precision
Integrating machine vision into the depaneling process elevates the precision and reliability of PCB cutting. Machine vision systems use high-resolution cameras and sensors to monitor the cutting process, ensuring alignment and detecting any deviations in real-time. This technology reduces errors, minimizes waste, and maintains consistent quality across all boards.
Benefits of Machine Vision:
- Real-Time Monitoring: Detects and corrects misalignments instantly.
- Quality Assurance: Ensures each PCB meets stringent quality standards.
- Automation: Streamlines the depaneling process, reducing manual intervention.
Selecting the Right Depaneling Machine for Your Manufacturing Process
Choosing the appropriate depaneling machine involves assessing your production needs, PCB designs, and desired throughput. Consider the following factors:
- Cutting Precision: Opt for laser depaneling machines if your PCBs have intricate designs.
- Production Volume: High-volume manufacturers may benefit from the speed of laser systems.
- Material Compatibility: Ensure the machine can handle the specific materials and thicknesses of your PCBs.
- Integration Capabilities: Look for systems that can seamlessly integrate with your existing SMT whole line equipment.
By evaluating these factors, you can select a depaneling machine that aligns with your manufacturing goals and enhances overall efficiency.
The Future of PCB Depaneling: Trends and Innovations
The PCB depaneling landscape is evolving with advancements in laser technology and automation:
- Enhanced Laser Systems: Development of more powerful and precise lasers like the CMS laser is set to improve cutting accuracy.
- Automation Integration: Combining depaneling machines with robotic arms and sorting systems for fully automated production lines.
- Sustainability: Innovations aimed at reducing energy consumption and minimizing waste in the depaneling process.
- Smart Manufacturing: Incorporating IoT and AI for predictive maintenance and optimized operation of depaneling systems.
Staying abreast of these trends ensures that your manufacturing process remains competitive and efficient.
Frequently Asked Questions
What is the main advantage of laser depaneling over routing?
Laser depaneling offers higher precision, faster cutting speeds, and minimal mechanical stress, resulting in higher quality PCBs with fewer defects.
Can laser depaneling handle complex PCB designs?
Yes, laser depaneling is highly effective for intricate and fine-pitch PCB designs, including curves and sharp corners.
What type of laser is best for high-density PCBs?
UV lasers are preferred for high-density PCBs due to their higher precision and minimal thermal impact.
How does machine vision improve the depaneling process?
Machine vision provides real-time monitoring and alignment, ensuring consistent cutting accuracy and reducing errors during depaneling.
Is laser depaneling cost-effective for small-scale production?
While the initial investment may be higher, laser depaneling offers long-term benefits in quality and efficiency that can be cost-effective even for small-scale production.
Key Takeaways
- Laser depaneling provides superior precision and speed compared to traditional methods like routing and V-groove scoring.
- CO2 and UV lasers each have unique advantages, making them suitable for different PCB depaneling needs.
- Machine vision integration enhances cutting accuracy and quality assurance in the depaneling process.
- Selecting the right depaneling machine involves considering cutting precision, production volume, material compatibility, and integration capabilities.
- The future of PCB depaneling lies in advanced laser systems, increased automation, and smart manufacturing technologies.
For more information on advanced depaneling solutions, explore our DirectLaser H5 PCB-FPC Laser Cutting Machine and DirectLaser H3 PCB & FPC Laser Cutting Machine No Waste. Discover how our PCB depaneling machines can revolutionize your manufacturing process with precision and efficiency.