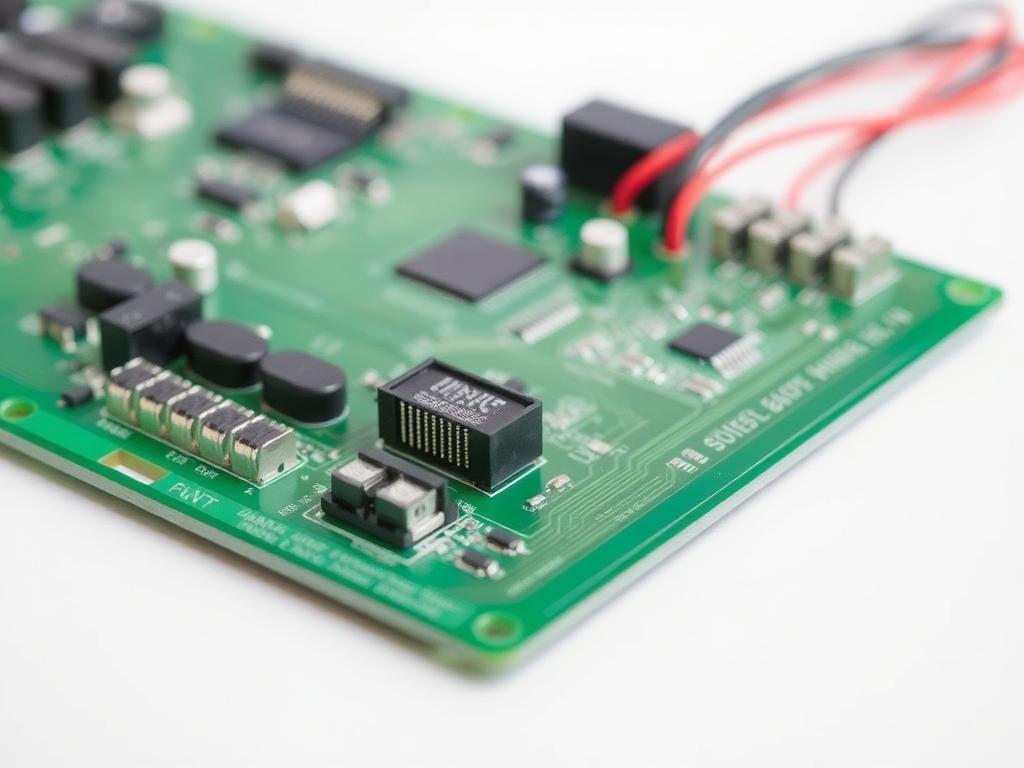
Best PCB depaneling methods
Choosing the Right PCB Depaneling Method: A 20-Year Expert’s Guide to Seamless PCB Separation
For two decades, I’ve been immersed in the world of PCB manufacturing, witnessing firsthand the evolution of depaneling methods. From the initial design to the final product, separating individual pcbs from their larger panels is a critical step. Choosing the right depaneling method isn’t just about cutting boards; it’s about ensuring quality, minimizing stress, and optimizing your manufacturing process. This article delves into the various methods of pcb depaneling, offering insights gleaned from years of experience, helping you make informed decisions that impact your production efficiency and product integrity. If you’re looking to streamline your pcb separation and ensure the integrity of your circuit boards, this guide is for you.
Navigating the World of PCB Depaneling: Key Questions for Optimal Separation
Understanding the landscape of pcb depaneling is crucial for any electronics manufacturer. Let’s explore some key questions to guide you through the selection process, ensuring you choose the right depaneling method for your specific needs.
What Exactly is PCB Depaneling and Why Does the Method Matter?
In essence, pcb depaneling is the process of separating individual pcbs from a larger pcb panel after the assembly process. Think of it like cutting cookies from a sheet of dough. However, unlike cookies, circuit boards are delicate and require precision. The chosen depaneling method directly impacts the mechanical stress applied to the pcb, potentially damaging sensitive components or solder joints. Over my 20 years, I’ve seen firsthand how the wrong approach can lead to micro-cracks, reduced reliability, and ultimately, increased costs. Whether you’re dealing with high-volume production or intricate designs, the depaneling process needs careful consideration. We, at pcbdepaneling.com, understand this intimately, as we provide a range of solutions from PCB Router Machine options to advanced PCB Laser Depaneling systems.
What are the Traditional PCB Depaneling Methods Like V-Groove and Punch?
Historically, methods like v-scoring and punch depaneling were common. V-scoring involves creating a V-shaped groove along the intended separation lines on the pcb panels. The individual pcbs are then separated by applying pressure along this score line – sometimes manually, which can be a manual alternative to breaking the web. While simple, v-scoring can introduce a slight degree of stress on the board. The punching method is the process of using a die to physically stamp out the singular pcbs being punched from the panel. This is often suitable for high-throughput environments but may not be ideal for boards with components close to the edge due to the inherent force involved. While these methods have their place, particularly for simpler pcb designs, they often lack the finesse required for modern, densely populated boards. Our history includes providing robust V-Groove Depaneling solutions for companies like TP-LINK who valued the efficiency for certain product lines.
When is Laser Depaneling the Optimal Choice for PCBs?
Laser depaneling, using a precise laser beam, has emerged as a superior method for many applications. In my experience, laser depaneling shines when dealing with complex pcb shapes, sensitive components, or when minimal mechanical stress is paramount. The focused energy of the laser precisely cuts through the pcb material, leaving clean, smooth pcb edges without physical contact. This is especially crucial for flexible printed circuits (FPCs) and boards with delicate surface mount components. Our PCB Laser Depaneling machines are favored by companies like Canon for their high-precision requirements. The ability of our laser systems to handle intricate contours and tight tolerances makes it an invaluable asset in modern electronics manufacturing processes.
How Do PCB Router Machines Offer Flexibility in Depaneling?
PCB Router Machine solutions offer a versatile approach to pcb depaneling. Similar to a CNC machine, a router utilizes a rotating cutter to precisely cut around the pre-routed outlines of the individual pcbs. This depaneling method provides excellent flexibility in handling various pcb shapes and sizes. Router depaneling minimizes stress on the board compared to snap-off methods, making it suitable for boards with components near the edges. We’ve seen great success with our PCB Router Machine offerings, particularly with customers like BYD and Flex who require adaptability for diverse product lines. Using a router allows for complex profiles and intricate designs, making it a go-to solution for many pcb manufacturing needs.
What Role Does PCB Panelization Play in Choosing a Depaneling Method?
PCB panelization is the process of arranging multiple pcb designs on a single larger panel for efficient pcb manufacturing. The pcb panelization guidelines directly influence the choice of depaneling techniques. Factors like the spacing between boards (tab routing or v-score), the presence of breakaway tabs, and the overall layout of the pcb panels dictate which method for depaneling is most suitable. For instance, pcbs are routed leaving small tab connections that are later broken or cut. Understanding the panelization strategy upfront is crucial for choosing the right depaneling method. Our expertise extends to advising on optimal panelization strategies to complement our depaneling equipment.
How Does Throughput Influence the Selection of a Depaneling System?
Throughput, or the number of pcbs that can be separated in a given time, is a critical factor, especially for high-volume production. While laser depaneling offers unparalleled precision, PCB Router Machine options and even advanced V-Groove Depaneling systems can provide higher throughput for certain designs. The decision often involves a trade-off between speed and precision. For companies like TCL and Xiaomi, who demand high volumes, our Automatic Equipment options, often integrated with router or v-score systems, provide the necessary speed and efficiency. Understanding your production volume requirements is paramount when selecting the right depaneling method.
Are There Hybrid Depaneling Methods or Combinations to Consider?
In some cases, a combination of depaneling methods might be the most effective approach. For example, pcbs might be initially separated using v-scoring, with critical or sensitive areas then refined using laser cutting. This hybrid approach leverages the strengths of different technologies. Another common scenario involves using a router to cut most of the pcb along the edges, leaving small tab connections that are then carefully broken. This can balance speed and stress reduction. We often work with manufacturers like Lenovo and OPPO to design custom solutions that integrate different depaneling techniques for optimal results.
What Factors Determine the Right Depaneling Method for My PCBs?
Choosing the right depaneling method involves considering several key factors. The complexity of your pcb design includes the shape, size, and density of components. The materials used (pcb material) and the presence of sensitive components are also critical. Budget constraints and desired throughput will further influence your decision. For instance, flexible pcbs often necessitate laser depaneling due to their delicate nature. We, at pcbdepaneling.com, guide our clients through this evaluation process, ensuring they select the suitable depaneling method for their specific pcb manufacturing needs.
Can Automation Enhance the Efficiency of My Depaneling Process?
Absolutely. Automatic Equipment for pcb depaneling significantly enhances efficiency and reduces manual labor. Automated systems can handle pcb panels, load and unload boards, and even integrate with other SMT whole line equipment. This not only increases throughput but also improves consistency and reduces the risk of human error. Our Automatic Equipment, such as our sorting and palletizing machines favored by HONOR, plays a vital role in streamlining the entire pcb processing workflow. Integrating automation into your depaneling process is a key step towards optimizing your pcb manufacturing line.
What Kind of Support and Accessories Are Available for Depaneling Machines?
Beyond the core depaneling machines, having access to reliable support and accessories is crucial. This includes things like replacement cutters for routers, fixtures for holding pcb panels securely, and software updates for laser systems. Proper maintenance and timely replacement of consumables are essential for maintaining the performance and longevity of your equipment. We offer a comprehensive range of Accessories, including milling cutters and spare parts, ensuring our customers have the support they need to keep their production lines running smoothly.
Conclusion: Making the Right Cut for Your PCBs
Selecting the optimal method for your pcbs is a multifaceted decision. From the precision of laser depaneling to the flexibility of a PCB Router Machine and the efficiency of V-Groove Depaneling, each approach offers unique advantages. My 20 years in this industry have taught me that understanding your specific needs, from the intricacies of your pcb design to your desired throughput, is paramount. Don’t hesitate to explore the various options and consider hybrid solutions for optimal results.
Key Takeaways:
- PCB depaneling is a critical step impacting product quality and reliability.
- Laser depaneling offers high precision and minimal stress, ideal for sensitive components.
- PCB Router Machine solutions provide flexibility for various board shapes and sizes.
- V-Groove Depaneling is a cost-effective option for simpler designs and high volumes.
- Automation can significantly enhance the efficiency of your depaneling process.
- Consider your pcb panelization guidelines when selecting a method.
- Proper support and accessories are essential for maintaining your equipment.
Ready to discuss the best depaneling solution for your needs? Explore our range of PCB Router Machines, PCB Laser Depaneling systems, and V-Groove Depaneling machines. Don’t forget to check out our PCB/FPC Punching Machine options and our Automatic Equipment to streamline your entire production line. We also offer a variety of Accessories to keep your operations running smoothly. For those looking for comprehensive solutions, explore our SMT whole line equipment. Let our experience guide you to the perfect cut.
Frequently Asked Questions about PCB Depaneling
What is the main advantage of laser depaneling?
Laser depaneling offers the significant advantage of being a non-contact process, resulting in minimal mechanical stress or damage to the pcb. This is crucial for delicate boards with sensitive components. The precise cuts achieved by laser technology also make it ideal for complex shapes and tight tolerances.
Is a router machine suitable for all types of PCBs?
While using a router is versatile, it’s best suited for pcbs where the component placement allows for a safe cutting path. For boards with components very close to the edge, or those requiring intricate internal cuts, laser depaneling might be a better option.
How does V-groove depaneling compare to laser depaneling in terms of cost?
Generally, v-scoring is a more cost-effective depaneling method, especially for high-volume production of simpler pcb designs. Laser depaneling, while offering superior precision and reduced stress, typically involves a higher initial investment.
What factors should I consider when choosing between different depaneling methods?
Key factors include the complexity of your pcb design, the sensitivity of the components, your desired throughput, budget constraints, and the level of automation you require. Understanding these factors will help you determine the suitable depaneling method.
Can depaneling be integrated into a fully automated SMT line?
Yes, automatic equipment for pcb depaneling can be seamlessly integrated into a Surface Mount Technology (SMT) line. This automation streamlines the entire assembly process, increasing efficiency and reducing manual handling.