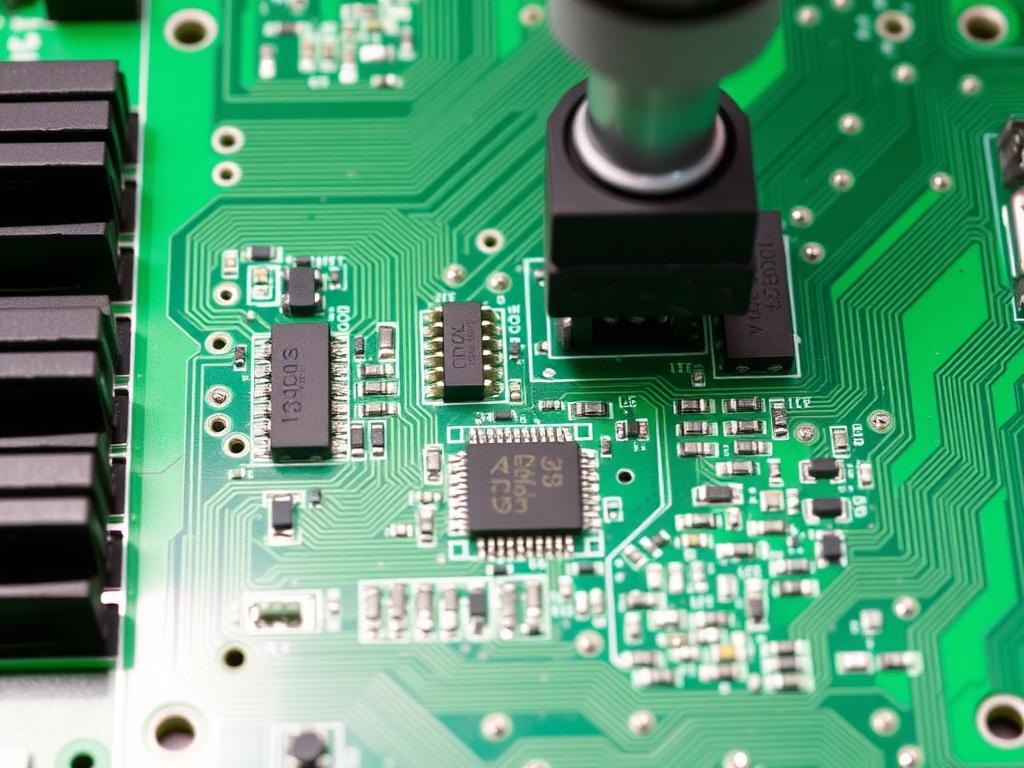
PCB depaneling for robotics
PCB Depaneling: From Manual Separation to Laser Precision – A 20-Year Journey
In the dynamic world of electronics manufacturing, the process of separating individual printed circuit boards (PCBs) from a larger panel, known as PCB depanelleme, is critical. For two decades, I’ve been immersed in this process, witnessing its evolution from basic hand breaking to the sophisticated laser technology of today. This article explores the various methods of PCB depaneling, their advantages, disadvantages, and the future direction of this crucial manufacturing step. If you’re involved in electronics technology, large-scale PCB processing, or even as an individual PCB enthusiast, you’ll find valuable insights to enhance your understanding and potentially improve your processes.
1. What is PCB Depaneling and Why is it Important?
Let’s start with the basics. In the PCB imalatı process, multiple PCB'ler are often fabricated on a single panel to maximize efficiency and reduce production costs. Once the components are mounted using yüzeye montaj teknolojisi ve lehim joints are complete, these individual devre kartları need to be separated. This process of separating the bireysel PCB'ler from the larger panel is known as PCB depanelleme, also sometimes referred to as singulation. It is a pivotal step in the entire PCB montajı line. Why is it so important? Because poorly executed depaneling can lead to damaged boards, compromised lehim joints, and ultimately, faulty electronic devices. The demand for PCB'ler continues to rise, fueled by the internet of things (iot) and the ever-increasing number of electronic devices, making the depaneling işlemi not just a final step, but a critical link in the production chain.
For years, we have seen the pcb manufacturing industry rely on various depaneling yöntemleri, from simple hand breaking to sophisticated yönlendirici Ve lazer depaneling sistemleri. Each approach comes with its own set of benefits and challenges. Over my two decades in the industry, I’ve learned firsthand that the right method can significantly boost production line speed and reduce costs while ensuring the quality of the final product. Conversely, a poor choice can result in significant waste and delays.
2. What are the Different Depaneling Methods Used in PCB Üretimi?
Over the years, I’ve seen several PCB depaneling yöntemleri used, each with its own nuances and applications. It’s not a one-size-fits-all situation. The best method depends on the type of PCB, the complexity of the design, the materials used, and the volume of production. Here’s a breakdown of the most common depaneling yöntemleri:
- Manual Depaneling: This is the simplest form, often done by hand using a specialized tool or even just bending and snapping along pre-scored lines. While it’s the most cost-effective option for very low volumes, it’s not suitable for large scale production due to the risk of mekanik stres and inconsistencies.
- V-Groove Depaneling: This involves scoring the PCB panel along the separation lines with a V-shaped groove, allowing the boards to be easily snapped apart. It is a common method for simpler devre kartları and is faster than manual separation, but it still carries the risk of mekanik stres.
- Punch Depaneling: Here, a mechanical die with a shape matching the individual circuits is used to yumruk the boards panelden delinmiş. This is suitable for high volume production of similar boards, but the tooling cost and inflexibility can be drawbacks.
- PCB Router Depaneling: A yönlendirici machine uses a high-speed rotating cutter to precisely cut the PCB'ler from the panel. It is more versatile than punching or V-scoring, capable of handling complex shapes, curves, and sharp corners. It also creates less stress on the components.
- Lazer Depaneling: This advanced method uses a precise lazer kesim beam to separate PCB'ler from the panel. It is particularly suitable for very small PCB'ler, complex shapes, and sensitive materials, as it minimizes part induced stress and provides a precise cut kerf width.
Each of these methods has found its place in the industry, and the choice depends heavily on the specific needs and volume of production. Over time I’ve seen a shift from manual and simple mechanical methods to more automated and precision-based techniques.
3. How Does the PCB Yönlendirici Machine Work and Where is it Best Used?
The PCB yönlendirici has become a workhorse in PCB depanelleme. From my experience, I’ve seen it bridge the gap between simple V-scoring and the precision of lazer depaneling. So, how does it work? A PCB yönlendirme machine uses a high-speed rotating milling bit, guided by a computer-controlled process, to accurately separate PCB'ler birinden daha büyük panel. PCB panel is often held in place by a fikstür, ensuring the yönlendirme process is precise and consistent. This tool is used to create clean and accurate edges on the devre kartları.
A key advantage of a yönlendirici is its versatility. Unlike yumruk depaneling, which requires a special fixture for each design, a yönlendirici can handle a variety of shapes and sizes. The machine follows a programmed path, enabling it to cut curves and sharp corners with ease. This is particularly important when dealing with complex PCB designs that have intricate outlines. For rigid flex pcbs, A yönlendirici machine is also the best choice.
We’ve supplied many of our PCB Yönlendirici Makinesi to major electronics manufacturers like TP-LINK, Canon, BYD, Flex, TCL, Xiaomi, Lenovo, OPPO, HONOR, and Foxconn. They have found it to be reliable for a wide range of PCB depanelleme needs, whether it’s bireysel PCB'ler or multiple individual circuits. One of the core advantages of routing is that it minimizes stress on components during the ayırmak process, unlike manual methods that can introduce significant mekanik stres.
4. What are the Advantages and Disadvantages of Mechanical PCB Routing?
As I’ve witnessed over the years, mechanical PCB yönlendirme offers a solid balance of versatility and efficiency, but it isn’t without its limitations. The advantage of speed and flexibility that yönlendirme provides makes it a great fit for many production environments, but it’s important to understand the potential drawbacks. Here’s what I’ve learned:
Avantajları:
- Çok yönlülük: As mentioned before, yönlendirme can handle various shapes, sizes, and materials. This makes it ideal for PCB'ler with complex designs, curves and sharp corners, as well as boards with multiple individual circuits bir daha büyük panel.
- Azaltılmış Mekanik Stres: Unlike hand breaking, and v-cut methods, yönlendirme minimizes the part induced stress Açık PCB'ler, reducing the risk of damage to sensitive components, particularly those especially those close için edge of the board.
- Kesinlik: The computer controlled process ile ilgili yönlendirme ensures accuracy in cutting, resulting in cleaner edges. This is critical for subsequent assembly processes.
- Cost Effective: While the initial investment might be higher than simpler methods, the long-term operational costs of yönlendirme are very reasonable and suitable for medium to large volumes.
- Suitable for Flex Circuit: Unlike mechanical dies or yumruk method, yönlendirici machine is suitable for various type of material including esneklik material.
Disadvantages:
- Tool Wear: The milling bits used for yönlendirme wear out over time and require replacement. However, this can be mitigated by choosing suitable quality milling cutters like our Milling Cutter.
- Cutting Oils: The use of cutting oils can add additional steps to the process.
- Dust and Debris: Yönlendirme generates dust and debris, requiring proper ventilation and cleaning systems to maintain a clean working environment.
- Slower Than Punching: For very large volumes of identical PCB'ler, yumruk depaneling might be a slightly faster method.
We have developed several routing machines, from the GAM 380AT PCB Alt Panel Açma Makinası, to the GAM 330AT Hat İçi Otomatik PCB Yönlendirici Makinesi. These are designed to mitigate the drawbacks, focusing on efficiency and cleanliness. Over the past years, I’ve seen the technology behind these machines become more advanced, allowing the process to be much more precise and cost-effective.
5. How Does Lazer Depaneling Compare to Traditional Methods and is it Better?
Lazer depaneling has emerged as a game-changer in the PCB depanelleme world. As someone who has seen the industry shift manual to laser, I can say it offers unprecedented precision, speed, and flexibility, but it comes at a cost. Let’s discuss how lazer depaneling compares to more traditional methods.
Traditional methods like manual snapping, or v-kesim methods often rely on creating a weaker line that can be easily broken. While cost effective, they often introduce unwanted stress into the board. Lazer depaneling, on the other hand, is a non-contact process. Instead of a mechanical force, a lazer yönlendirme beam is used to precisely ablate the material along the separation line. This reduces the part induced stress and eliminates the risk of physical damage from tooling, making it perfect for very sensitive PCB'ler veya esneklik substratlar.
Lazer Depaneling'in Avantajları:
- Yüksek Hassasiyet: Lazer depaneling provides a very high degree of accuracy, with a cut kerf width ile ilgili less than 20 microns.
- Minimum Stres: The non-contact lazer kesim process significantly reduces mekanik stres, making it ideal for delicate PCB'ler Ve esneklik devreler.
- Esneklik: Lazer depaneling is capable of cutting complex shapes, eğriler ve keskin köşeler with extreme accuracy.
- Clean Cut: It produces very clean and smooth edges with no burrs or debris, reducing the risk of dust and contamination.
- Suitable for Small PCBs: When dealing with daha küçük PCB'ler used in complex electronic devices, lazer yönlendirme offers great precision where other methods might fail.
Disadvantages of Laser Depaneling:
- Higher Initial Cost: The equipment for lazer depaneling is significantly more expensive compared to traditional mechanical methods.
- Noticeable Heat Effect: Although minimal, there is some heat generated during lazer depaneling, which can have an effect on certain materials.
- Slower Than Some Methods: While fast, lazer depaneling can be slower than yumruk depaneling for very high volumes of identical boards.
Our experience shows that while the initial investment in lazer depaneling is higher, the benefits of reduced stress, increased accuracy, and overall quality often outweigh the cost, especially for high-value PCB'ler ve karmaşık esnek devre designs. We’ve seen a growing adoption of lazer depaneling in the industry. Our DirectLaser H5 PCB-FPC Lazer Kesim Makinesi Ve DirectLaser H3 Lazer Çevrimiçi Makinesi are testaments to the effectiveness and advancement of the technology.
6. When is Yumruk Depaneling the Right Choice for PCB'ler?
Yumruk depaneling, while not as versatile as yönlendirici veya lazer depaneling, still holds its ground as a valuable method in specific scenarios. In my two decades in this industry, I’ve seen its strength in high-volume production of identical PCB'ler where the design is relatively simple and well-defined.
Süreci yumruk depaneling involves using a mechanical die, customized to the specific shape of the individual circuits. This die is pressed onto the PCB panel, and the boards are broken out of the panel. It is a fast and relatively efficient method for high production quantities.
Advantages of Punch Depaneling:
- Yüksek Hız: For large volumes of identical PCB'ler, yumruk depaneling can be significantly faster than routing or laser. The advantage of speed makes it an attractive option for high-volume manufacturers.
- Lower Operational Cost: Once the tooling is created, the operational cost per board is lower.
- Consistent Results: The process is very repeatable, ensuring consistent results across all the boards on the panel.
Disadvantages of Punch Depaneling:
- High Tooling Cost: The initial tooling cost is high, as you need to manufacture a custom die for each PCB design. This can be prohibitive for smaller production runs.
- Lack of Flexibility: Unlike routing, punch depaneling is not suitable for complex shapes, curves or sharp corners. Each PCB design requires a different die.
- Mechanical Stress: It can also introduce more mekanik stres on the components compared to yönlendirici veya lazer depaneling, which can damage sensitive parts, particularly if they are near the separation line.
- Not suitable for flex: Yumruk depaneling is not suitable for esneklik material.
In our experience, we’ve seen yumruk depaneling favored by manufacturers producing large quantities of identical, simpler boards, where tooling cost is amortized over a high production volume. For instance, in the production of basic electronics like consumer gadgets. However, its inflexibility and limitations make it less suitable for complex devre kartları and prototypes, and it definitely doesn’t come anywhere near the precision of lazer depaneling. Bizim ZM10T & 15T PCB & FPC Delme Kesme Makinesi are examples of our commitment to this method, offering robust and reliable performance.
7. What is V-Cut Depaneling and How Does it Impact Manufacturing?
V-cut depaneling is another method I’ve seen frequently used in the industry. It’s a process that involves creating a V-shaped groove (v-puanı) on the top and bottom surfaces of the PCB panel along the intended separation line, allowing the boards to be snapped apart relatively easily. In essence, it pre-weakens the material so that the bireysel PCB'ler can be broken out of the panel with minimal force.
İçinde v-kesim depaneling, the panel are scored using a specialized tool. The depth of the v-puanı needs to be carefully controlled, ensuring that it’s deep enough to facilitate easy separation but not so deep that it weakens the alt tabaka too much. The method relies on manual or machine-assisted separation after the v-puanı is complete.
Advantages of V-Cut Depaneling:
- Maliyet Etkin: It’s a relatively inexpensive method, particularly for high volumes of simple designs.
- Fast and Efficient: Süreci panel are scored is quick and efficient, making it suitable for large scale production.
- Simple Process: It doesn’t require complex machinery or specialized skills.
Disadvantages of V-Cut Depaneling:
- Mechanical Stress: The snapping process can induce mekanik stres, particularly on lehim joints and components that are close to the separation line. This can lead to board damage and failures.
- Limited Design Flexibility: It is not suitable for PCB'ler with complex shapes, eğriler ve keskin köşeler, or those that require a precise separation path. It works best for straight line separation.
- Less Precise than other methods: The breaking step can create an uneven and rough board edges.
- Not Suitable for Flexible Materials: When it comes to flexible materials such as esneklik, v-scoring isn’t the best solution. The esneklik material can get damaged when broken out of the panel, and it doesn’t guarantee a clean ayırmak astar.
We understand the trade-offs involved with v-kesim depaneling, and our range of V-Oluklu Panel Açma makineler, örneğin ZM30-ASV Tam Otomatik testere tipi V-oluklu PCB panel çıkarma Ve ZM30-P PCB Giyotin Ayırıcı, aim to maximize the benefits of this method while mitigating its inherent limitations. While this method is commonly used in the industry, it’s important to carefully consider its drawbacks, particularly when dealing with higher value or complex devre kartları.
8. Why is Precision and Minimal Mekanik Stres so Crucial in Circuit Board Panelden ayırma?
Precision and minimal mekanik stres are non-negotiable requirements in modern devre kartı depaneling. Over the years, I’ve seen firsthand the repercussions of poor separation techniques. The impact on the quality and reliability of the final product is enormous, which is why we have strived to develop solutions that minimize both.
Why is this so crucial? First, devre kartları are packed with delicate components and intricate traces. These components, especially those using yüzeye montaj teknolojisi, are extremely sensitive to physical forces. Applying too much mekanik stres sırasında depaneling işlemi can cause cracks in the lehim bağlantıları, component damage, or even delamination of the board itself. These damages are not always immediately apparent but can lead to premature failure in the field.
Second, modern electronics have become incredibly complex, often involving multiple layers and intricate devre layouts. Any deviations from the intended separation path can sever traces or other delicate features, rendering the board unusable. This is especially true when dealing with daha küçük PCB'ler and tight spaces. This is where precise lazer kesim shines.
Finally, quality and reliability are crucial factors in the competitiveness of products, especially in high-stakes sectors like aerospace, medical devices, and automotive. The cost of failure is far higher than the cost of investment in good equipment.
Achieving precision and minimal stress requires using the right depaneling sistemleri, whether that’s a carefully programmed router cutting machine or a lazer yönlendirme system. Proper demirbaşlar, precise alignment, and controlled forces are also crucial to maintaining the integrity of every board. For us, it’s not just about bireyi ayırmak boards, it’s about ensuring that each board is ready to perform its intended function reliably for a long time. Our commitment to precision is evident in every one of our products, from our automated solutions to our precision cutting tools.
9. How Can Automation Improve the Depaneling Process Ve Increase Production Line Speed?
Automation has dramatically transformed the PCB depanelleme landscape, and for the better. In the past, much of the process was done manually, which was slow, inconsistent, and prone to errors. In today’s üretim süreci world, automation plays a key role in ensuring a high level of production line output and reducing waste.
Automation brings many advantages to the depaneling işlemi. First and foremost, it increases speed. Automated machines can process many boards per hour compared to manual operations. The increase in production line speed directly translates into reduced production times and lower operational costs. Also, automation ensures consistency, a critical factor in high volume production, especially when working with devre kartları that require high precision.
Moreover, automated systems reduce the need for manual labor, minimizing the risk of human error and workplace injuries. When coupled with vision systems and advanced software, automated depaneling machines can detect and rectify any misalignment or issues immediately, guaranteeing that each board is separated correctly. This is something we, at pcbdepaneling.com, focus on a lot.
We have developed a variety of automated solutions, including Automatic Plate Palletizing Machines Ve Automatic Sorting and Palletizing Machines, designed to work seamlessly within your systems that increase production line. These machines integrate smoothly with existing production lines and reduce the need for manual intervention. The use of automation not only improves the depaneling işlemi but also increases the efficiency and profitability of the entire production line. Our experience shows that investing in automated systems is a step towards increased efficiency, reduced waste, and improved product quality.
10. How Do I Choose the Best Depaneling Sistemi for My PCB'ler?
Doğruyu seçmek depaneling sistemi senin için PCB'ler can make all the difference in the efficiency, quality, and cost-effectiveness of your production. The best system is dependent on several factors, and there’s no “one-size-fits-all” solution, it’s very important to assess all relevant factors. Here are some factors that should play a role in your decision.
- Üretim Hacmi: If you are processing a high volume of identical boards, a yumruk depaneling system might be suitable, if design constraints allow for it. If you produce small quantities of boards with complex shapes and eğriler ve keskin köşeler, then a yönlendirici veya lazer depaneling system might be a better choice.
- PCB Design Complexity: Complex designs with tight components require a precise and low-stress method, making lazer depaneling or precision yönlendirme your preferred option. Simple designs with straight separation lines are fine with a v-cut or yumruk method.
- Material Sensitivity: If you have sensitive components that are close to the separation line, lazer depaneling should be considered due to its minimal mekanik stres. Esneklik materials will also need a more careful approach, and yönlendirici veya lazer depaneling are the best choice in that case.
- Bütçe: The initial cost of lazer depaneling is high, so if you are operating within a limited budget, then a yönlendirici machine would be a better choice, as it provides an excellent balance between accuracy and cost.
- Required Line Speed: If your production line needs to be really fast, a yumruk method is still valid for certain types of circuit boards, but is not as flexible as yönlendirici veya lazer sistemleri.
- Long Term Costs: Consider not only the initial cost but also the operational costs, including tool replacement, energy consumption, and waste disposal. While lazer depaneling has a higher initial cost, it might provide long term cost benefits due to it’s precision, low stress, and clean cuts.
For a lot of our clients, the role in the manufacturing process of depaneling machines is critical. When choosing your depaneling sistemleri, you should always look for a reliable supplier that can provide not only top quality machines, but also technical support and parts when you need them. We have the necessary experience to help you choose the right system.
Sıkça Sorulan Sorular
What is the difference between PCB depaneling and PCB singulation?
There is virtually no difference between PCB depaneling and singulation. Both terms refer to the ayırma süreci bireysel PCB'ler daha büyük bir panelden.
Can I depanel PCBs with components on them?
Evet, PCB depanelleme is usually done after the components are mounted, but it should always be done with appropriate care to avoid damage to the components or lehim bağlantıları.
What method should I use for my flex PCBs?
İçin flex pcb depaneling plays a pivotal role. Given the sensitive nature of flexible materials, the best options for esneklik circuits are either yönlendirici veya lazer depaneling. Both of these methods provide the necessary precision and low stress needed to prevent material damage.
Is Laser depaneling really worth the high cost?
It really depends on your specific situation. While the initial investment is higher, the benefits of precision, minimal stress, and the ability to handle complex designs may offset the higher cost, especially for high-value boards.
What kind of maintenance do PCB depaneling machines require?
The maintenance requirements vary. A yönlendirici machine will require regular bit replacement and cleaning. Lazer depaneling machines will require cleaning of the lazer kesim head and optical components. All machines will require regular maintenance, which can be done by qualified technicians.
Önemli Noktalar
- PCB depanelleme bireysel bireylerin ayrılması sürecidir PCB'ler from a larger panel, essential in PCB montajı.
- Several methods exist, including manual separation, v-kesim, yumruk, yönlendirici, Ve lazer depaneling.
- Yönlendirici machines are versatile, suitable for complex shapes, and minimize part induced stress, but they require regular maintenance.
- Lazer depaneling provides high precision and minimal stress, ideal for small, delicate PCB'ler Ve esneklik materials, though with a higher initial investment.
- Yumruk depaneling is ideal for high-volume production of identical, simple boards, but is inflexible and has high tooling costs.
- V-cut depaneling is cost effective for straight lines, but may introduce mekanik stres ile lehim bağlantıları.
- Automation enhances speed, consistency, and reduces errors in the depaneling işlemi.
- Choosing the correct depaneling sistemi depends on your production volume, design complexity, budget, and desired quality.
As a veteran in the industry, I’ve dedicated my career to understanding and improving the depaneling işlemi. My goal is to provide solutions that are both innovative and practical, helping you achieve your manufacturing goals. If you’re looking to improve your own process, we invite you to explore our range of products on our website, or contact us for more detailed assistance. You can learn more about our PCB Yönlendirici Makinesi, explore our V-Oluklu Panel Açma, check out our PCB / FPC Delme Makinesi, discover our Otomatik Ekipman, find the perfect Aksesuarlar, and explore our SMT tüm hat ekipmanı as well as PCB Lazer Panel Açma çözümler.