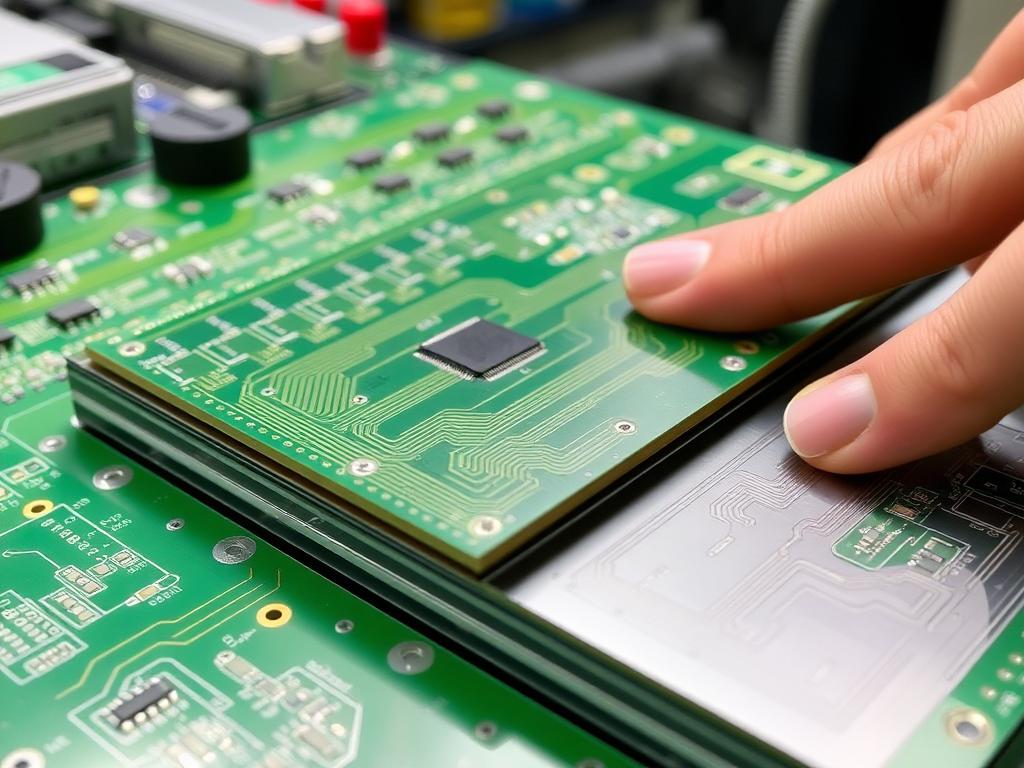
Multi-layer PCB depaneling
Precision PCB Depaneling: Mastering Multilayer PCB Separation for Flawless Circuit Boards
As someone who’s spent the last 20 years deeply immersed in the world of PCB manufacturing, I’ve seen firsthand how critical the depaneling process is. It’s the final step in transforming a large, multi-unit panel into individual, functional circuit boards. In this article, I’ll be sharing my expertise on the different methods of PCB depanel, with a special focus on the complexities of multilayer pcbs. We will explore various techniques, tools, and best practices to ensure you’re getting the best results for your valuable circuits. Whether you’re a seasoned professional or new to the industry, this guide is packed with insights that can help you optimize your pcb manufacturing process.
PCB Depaneling ແມ່ນຫຍັງແລະເປັນຫຍັງມັນຈຶ່ງສໍາຄັນ?
PCB depanel ແມ່ນຂະບວນການແຍກບຸກຄົນ pcbs ຈາກກະດານຂະຫນາດໃຫຍ່ຫຼັງຈາກ ການຜະລິດ pcb is complete. Think of it like breaking apart a chocolate bar into individual squares; you start with one big piece and then divide it into smaller pieces, ready to use. This step is crucial because during the pcb fabrication process, it’s much more efficient to produce many circuits on a single ຈານ. Once the ອົງປະກອບເອເລັກໂຕຣນິກ are placed and solder is applied, the ກະດານຂະຫນາດໃຫຍ່ needs to be broken down into those pcbs ສ່ວນບຸກຄົນ. The precision of this process directly impacts the quality and reliability of the final product. Poor depaneling can lead to ຄວາມກົດດັນກົນຈັກ, damaging sensitive ວົງຈອນ and rendering your precious boards useless. For example, excessive force in a manual separation process may lead to small cracks and shorts. We have seen this happen in some of the smaller companies, especially.
We are very meticulous about this stage in the process. As a leader in pcb depaneling solutions, we’ve provided our machines to industry giants like TP-LINK, Canon, BYD, Flex, TCL, Xiaomi, Lenovo, OPPO, HONOR, and Foxconn. These companies rely on precision and efficiency, and we deliver that. We have helped many to achieve consistent separation. These giants require an automated, high-precision solution, which is what our machines are designed to do. We have found that with automation, ຄວາມກົດດັນກົນຈັກ is greatly reduced.
What are the common depaneling methods used in the industry?
Over my 20 years in this business, I’ve witnessed several methods for pcb depaneling. Each comes with its own set of advantages and disadvantages, depending on the type of pcb being produced. Here are a few common approaches:
- Manual Depaneling: This is the most basic method, using hand tools like a ເຄື່ອງຕັດ pizza or pliers. It’s suitable for low-volume production or prototyping, but its accuracy is limited, and it often leads to ຄວາມກົດດັນກົນຈັກ on the board. This method is fine for prototyping and can be considered a good option for very small volumes of production.
- Scoring or V-Groove Depaneling: This involves creating a V-shaped groove along the separation lines of the ແຜ່ນວົງຈອນພິມ, allowing the boards to be snapped apart with controlled force. This method is cost-effective and efficient but may not be suitable for all board designs, especially those with components near the edges.
- ກຳນົດເສັ້ນທາງ: This involves using a ເຣົາເຕີ to precisely cut along the outline of the pcbs. ກຳນົດເສັ້ນທາງ offers high accuracy, making it suitable for complex shapes and sensitive components. It also leads to a smooth edge quality. We offer a range of ເຣົາເຕີ machines for different needs.
- ເຈາະ: This method uses a die and press to separate the pcbs. This is a fast option for high-volume production, but it requires custom tooling and is best suited for specific board shapes. It is very precise if you have the correct equipment.
- Laser Depaneling: This is the most advanced method, using a focused ເລເຊີ ຕັດຜ່ານ ແຜ່ນວົງຈອນພິມ. ເລເຊີ depaneling is highly accurate, minimizes stress, and offers greater design flexibility. We have invested heavily in advanced ເລເຊີ technology to deliver the best results.
Why is laser depaneling gaining popularity?
ເລເຊີ depaneling has rapidly gained traction in recent years, and for good reason. The ability to use a very thin and precise ເລເຊີ to separate the pcbs is revolutionizing the ຂະບວນການ depaneling. One of the key advantages is its minimal ຄວາມກົດດັນກົນຈັກ. Unlike other methods that can exert significant pressure on the boards, laser depaneling ensures that the delicate ອົງປະກອບເອເລັກໂຕຣນິກ are not damaged. This is especially vital for multilayer pcbs, where the internal ວົງຈອນ is more susceptible to damage.
ການຕັດເລເຊີ is also highly adaptable. It can easily handle complex shapes and contours that would be difficult or impossible to achieve with other methods. This flexibility is a boon for designers pushing the boundaries of ການອອກແບບ pcb ສໍາລັບ ອຸປະກອນເອເລັກໂຕຣນິກ ແລະ smartphones. Furthermore, laser depaneling eliminates the need for tooling, making it ideal for small to medium-sized production runs. This offers pcb manufacturers the flexibility that is needed in today’s market. At PCB Depaneling, we have seen firsthand the benefits our customers get from using our laser depaneling equipment. We believe this is the future of depaneling, and are happy to help customers move into this high-precision method.
How does multilayer PCB depaneling differ from single-layer boards?
Multilayer pcbs are a marvel of modern engineering. They consist of multiple layers of ຊັ້ນ conductive, separated by insulating ຜ້າປູພື້ນ. These layers allow for more complex ວົງຈອນ in a smaller form factor. While single-layer boards have connections placed on the top, multilayer printed circuit boards have several copper foil layers ກັບ electrical connections formed throughout the board. This complexity also brings challenges, especially when it comes to ການຍົກເລີກ. The increased number of inner layers makes these boards more fragile, increasing the risk of damage during separation. This risk is multiplied when using older methods. This fragility makes the ຂະບວນການແຍກ a complex procedure.
Standard mechanical ວິທີການ depaneling can introduce too much ຄວາມກົດດັນກົນຈັກ, potentially causing delamination, where the layers begin to separate. Therefore, precise methods are essential to maintain the structural integrity and reliability of multilayer boards. ເລເຊີ depaneling is often the method of choice for multilayer pcbs due to its non-contact nature, which minimizes ຄວາມກົດດັນກົນຈັກ and reduces the possibility of damage. We have found that the additional cost is justified, as it reduces the number of scrap boards and improves overall reliability of the product.
What are the challenges associated with multilayer pcb manufacturing?
Multilayer pcb manufacturing is a delicate art form. The process involves bonding multiple layers ຂອງ ການປະພຶດ ແລະ insulate materials together, creating a complex stack-up of circuits. The most significant challenge in manufacturing these complex boards is maintaining precise alignment of the layers. Any misalignment can affect the function of the board and lead to defects. The lamination process, during which the layers are bonded together, requires meticulous control of temperature, pressure, and vacuum. Any deviations in these parameters can result in imperfections such as voids and delamination. We have helped to optimize these processes for many of our customers.
Another major challenge is ensuring good signal integrity. In multilayer pcbs, signals can interfere with each other, especially at high frequencies. Careful ການອອກແບບ pcb and precise fabrication techniques are essential to minimize EMI and signal loss. Moreover, the higher the number of layers, the more complex the manufacturing becomes, leading to longer production times and higher costs. That is why choosing the right ລະບົບ depaneling is very important, as it is critical to the overall success of the manufacturing process. We have spent many years designing solutions to help customers overcome these problems.
What are the different types of PCB depaneling machines available?
Over the years, the advancement of technology has led to the introduction of several types of pcb depaneling machines to meet varied demands and production scales. Here’s a brief look at some of the machines we offer:
- Automatic Router Machines: These machines utilize a high-speed spindle to separate the pcbs ໂດຍ ເສັ້ນທາງ along a pre-determined path. They are precise, versatile, and suitable for complex board shapes. Our GAM 330AT In-Line Automatic PCB Router Machine is an excellent example. GAM 330AT In-Line Automatic PCB Router Machine
- Automatic V-Groove Separator: These machines utilize a blade to separate pcbs along a v-groove. They are ideal for high-volume production where the v-groove method is suitable. Our ZM30-ASV ການຕັດແຜ່ນ PCB ປະເພດ V-groove ອັດຕະໂນມັດຢ່າງເຕັມສ່ວນ is the right choice for many clients. ZM30-ASV ການຕັດແຜ່ນ PCB ປະເພດ V-groove ອັດຕະໂນມັດຢ່າງເຕັມສ່ວນ
- Automatic Laser Depaneling Machines: These machines use a focused ເລເຊີ to cut through the material, offering high precision and minimal stress. The DirectLaser H5 is our recommended choice for laser depaneling. ເຄື່ອງຕັດເລເຊີ DirectLaser H5 PCB-FPC
- Automatic Punching Machines: These machines use a punch to cut through the material, and are typically faster than milling. We offer the ZM10T & 15T PCB & FPC Punching ເຄື່ອງຕັດ for our customers. ZM10T & 15T PCB & FPC Punching ເຄື່ອງຕັດ
The right machine will depend on your production volume, board complexity, budget, and required precision. We’ve found that many smaller manufacturers grow with our ເຣົາເຕີ and then move into our laser depaneling offerings. We are always available to help our customers find the best solution for their needs.
What is the role of V-groove depaneling?
V-groove depaneling is a common method used in the pcb manufacturing process, particularly for boards that are designed with a predefined snap-off line. During the fabrication stage, a V-shaped cut is made into the ຜ້າປູພື້ນ material along the edges of the pcbs that need to be separated. The v-groove acts as a guide, allowing the boards to be easily separated through controlled breaking. The biggest advantage of v-groove depaneling is its speed and efficiency. It’s a cost-effective ວິທີການຕັດ, which is why it’s widely used for high-volume production of rigid pcbs, such as standard electrical boards. For example, it works well when producing pcbs ສໍາລັບ consumer electronics.
However, this ວິທີການໃນການປະຕິບັດ has limitations. The quality of the break can vary and may result in some ຄວາມກົດດັນກົນຈັກ on the board, especially if not performed correctly. It’s not suitable for complex shapes and boards with components that are placed close to the separation line. While v-groove depaneling is not as versatile as ຕັດເລເຊີ, it remains a practical solution for many applications where these constraints aren’t an issue. We offer several V-groove depaneling machines, including the ZM30-P PCB Guillotine Separator for high volume applications. ZM30-P PCB Guillotine Separator
How do PCB/FPC punching machines contribute to the separation process?
ເຄື່ອງເຈາະ PCB/FPC are another efficient solution for pcb depaneling, particularly for high-volume manufacturing. These machines employ a custom-made die and press to cut out the pcbs from the panel. This ຂະບວນການຕັດ is typically faster than ເສັ້ນທາງ and can be used with a wide variety of board shapes and sizes. The main benefit of using ເຄື່ອງເຈາະ PCB/FPC lies in their speed and accuracy. Once the tooling is set up, the ຂະບວນການແຍກ is quick and consistent, allowing for large quantities of pcbs to be processed quickly. They’re often used in the ຂະບວນການຜະລິດ of smartphones and wearables due to their high throughput capacity.
However, setting up the tooling for each different board design can be time-consuming and expensive. Therefore, these machines are best suited for situations where the volume of pcbs is high enough to justify the initial cost. Another limitation is the type of materials that can be processed. Thicker pcbs may require more powerful machines and special tooling. Despite these limitations, our customers see tremendous benefits in the right environment. The ZM10T & 15T PCB & FPC Punching ເຄື່ອງຕັດ is a versatile option. ZM10T & 15T PCB & FPC Punching ເຄື່ອງຕັດ
Why is precision so important when depaneling circuits?
Precision in ການຍົກເລີກ is paramount, especially with the increased use of multilayer pcbs and miniaturized ອົງປະກອບເອເລັກໂຕຣນິກ. Inaccurate ການຍົກເລີກ can cause various issues that can compromise the reliability and performance of the final product. Damage to delicate surface-mount ອົງປະກອບເອເລັກໂຕຣນິກ ແລະ through-holes are some of the common issues related to the ຂະບວນການຕັດ. ບໍ່ຖືກຕ້ອງ ວິທີການຕັດ can cause stress fractures in the ຜ້າປູພື້ນ material, leading to premature failure. This is especially important in critical applications such as ອຸປະກອນການແພດ ແລະ aerospace ອຸປະກອນ.
Another often overlooked issue is the risk of delamination in multilayer pcbs. Incorrect separation can cause the layers to separate, causing damage to the ວົງຈອນ within. When it comes to multilayer printed circuit boards, maintaining precision is vital, as these boards have layers and more complexity compared to double-layer pcbs. Precise separation eliminates the need for subsequent cleaning, thus reducing manufacturing costs and ensuring high-quality individual printed circuit boards. This is why we put so much focus on high precision technology. When you purchase our pcb depaneling machinery, we provide the best result.
How do I choose the right depaneling method for my pcbs?
ການເລືອກທີ່ຖືກຕ້ອງ ວິທີການ depaneling depends on many factors, including the type of pcb, production volume, budget, and the complexity of the design. Here’s a simple guide to help you make an informed decision:
- For prototyping and low-volume production: Manual methods like scoring or hand tools may suffice if you don’t need a large number of pcbs. However, keep in mind that this can be inefficient.
- For medium-volume production of simple boards: V-groove depaneling may be suitable if the design allows.
- For complex shapes and designs: ກຳນົດເສັ້ນທາງ offers versatility and precision.
- For high-volume production with regular shapes: ເຈາະ is a fast and efficient option, provided that the number of pcbs is large enough.
- For high-precision and sensitive applications (especially multilayer pcbs): ເລເຊີ depaneling is the ideal choice due to minimal ຄວາມກົດດັນກົນຈັກ and high adaptability.
We at PCB Depaneling, with our 20 years of experience, understand that there is no one-size-fits-all solution, and will help to analyze your specific needs to recommend the best solution. ຕິດຕໍ່ພວກເຮົາ today to discuss your needs, and let us be your guide.
FAQs:
What is the difference between routing and laser depaneling? Routing uses a rotating tool to cut the pcb, ໃນຂະນະທີ່ laser depaneling ໃຊ້ຈຸດສຸມ ເລເຊີ. ໄດ້ ເລເຊີ method is more precise, and reduces ຄວາມກົດດັນກົນຈັກ. We have seen that it is preferred in advanced manufacturing.
Can laser depaneling be used for all types of PCBs? ເລເຊີ depaneling can be used on a wide range of materials, but it is particularly advantageous for multilayer pcbs and those with intricate designs, because of reduced stress and high precision.
How can I reduce mechanical stress during depaneling? The best way to minimize ຄວາມກົດດັນກົນຈັກ is to use precise ວິທີການ depaneling such as ຕັດເລເຊີ or high-quality ເສັ້ນທາງ machines. Proper maintenance of the ລະບົບ depaneling can also play a part.
What are the key considerations for multilayer PCB depaneling? When dealing with multilayer pcbs, it is important to choose a method that minimizes stress on the board. ເລເຊີ depaneling is often favored due to its non-contact approach, which reduces the risk of delamination and damage.
What level of production volume is appropriate for a punching machine? Punching is ideal for high-volume productions because the setup cost and time are higher than ເລເຊີ ແລະ ເຣົາເຕີ machines. It’s crucial that you have enough throughput to justify the initial investment.
- ສະຫຼຸບ:
- PCB depanel ເປັນສ່ວນຫນຶ່ງທີ່ສໍາຄັນຂອງ pcb manufacturing process, separating pcbs ສ່ວນບຸກຄົນ ຈາກ ກ panel consisting ຂອງ multiple layers.
- There are different ວິທີການ depaneling, including manual, v-groove, ເສັ້ນທາງ, ເຈາະ, ແລະ laser depaneling.
- ເລເຊີ depaneling is gaining popularity due to its precision, minimal ຄວາມກົດດັນກົນຈັກ, and versatility with different types of pcbs.
- Multilayer pcbs require extra caution during ການຍົກເລີກ due to their complex structure and sensitivity to damage, and require a high level of precision and advanced techniques.
- ການເລືອກທີ່ຖືກຕ້ອງ ວິທີການ depaneling depends on several factors, such as complexity of the design, and production volume.
- Our 20 years of expertise have made us a leader in pcb depaneling, trusted by leading companies such as TP-LINK, Canon, BYD, Flex, TCL, Xiaomi, Lenovo, OPPO, HONOR, and Foxconn.
- ຕິດຕໍ່ພວກເຮົາ today to discuss your pcb depaneling needs and let us provide you with an optimized solution.