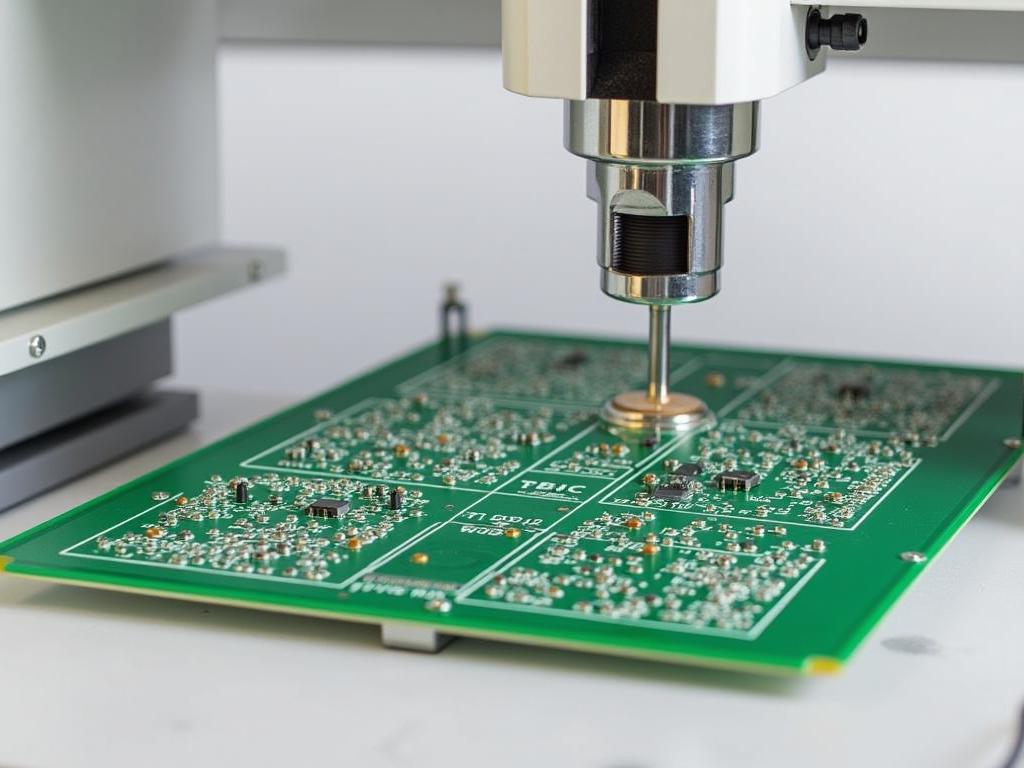
정밀 PCB 디패널링 장비
고정밀 PCB 분리 장비: 회로 기판 분리 공정 혁신
안녕하세요! 20년 넘게 PCB 제조 업계에 깊이 관여해 온 저는 효율적이고 정밀한 디패널링이 전체 공정에서 얼마나 중요한지 직접 경험했습니다. 이 글에서는 다양한 PCB 디패널링 방법과 이를 구동하는 기술, 그리고 적절한 장비 선택이 생산 효율성과 최종 제품 품질을 어떻게 획기적으로 향상시킬 수 있는지 자세히 살펴보겠습니다. 대규모 전자 제조 공장이든 개별 PCB 업체든, 이 종합 가이드는 공정 최적화에 필요한 귀중한 통찰력을 제공할 것입니다. 자, 시작해 볼까요!
PCB 디패널링이란 무엇이고 왜 필수적인가요?
전자 제조의 역동적인 세계에서 인쇄 회로 기판(PCB) 거의 모든 전자 장치의 근간을 이루는 기본 요소입니다. PCB에 부품을 조립한 후 패널, 그 분리 개인의 무대 또는 회로 기판 중요한 것입니다 프로세스 ~로 알려진 디패널링. 이것 프로세스 사소한 일이 아닙니다. 손상을 방지하기 위해 정확하고 안정적으로 수행해야 합니다. 판자 아니면 그 섬세한 구성 요소. 수년 동안 패널 제거에 대한 전통적인 접근 방식은 수동이었습니다. 연산자 각각을 처리하다 패널 그리고 분리하다 무대 핸드헬드를 사용하여 커터그러나 이 방법은 느리고 오류가 발생하기 쉬우며 정도 현대에 필요한 전자제품. 오늘날의 경쟁적이고 끊임없이 변화하는 세상에서는 다음과 같은 필요성이 있습니다. 고정밀 디패널링 그 어느 때보다 더 중요합니다 보장하다 그만큼 신뢰할 수 있음 그리고 고품질 완제품의.
의 필요성 PCB 디패널링 ~에서 유래하다 조작 프로세스 그 자체. 향상시키려면 생산 효율성, 다중 회로 기판 일반적으로 단일로 생산됩니다 패널. 그 디패널링 단계는 이 개인들이 있는 곳입니다. 무대 신중하게 분리됩니다. 이 분리는 각각의 무결성을 유지하는 방식으로 수행되어야 합니다. 판자, 생성하지 않고 보드에 스트레스, 영향을 미치는 땜납 관절이나 어떤 부위에 손상을 입히는 경우 요소 또는 코팅. 그것은 단순한 절단 작업이 아니라 깨끗하고 일관되며 손상 없는 것을 만드는 것입니다. 무대. 이는 매우 중요합니다. 사소한 불일치조차도 기능적 문제를 야기하여 해결에 많은 비용이 발생할 수 있기 때문입니다. 프로세스 최종 제품의 품질을 위한 토대를 마련합니다. 따라서 적절한 디패널링 단순히 속도가 중요한 것이 아니라, 정확성, 일관성, 그리고 회사에 큰 비용이 될 수 있는 잠재적 결함을 예방하는 것이 중요합니다.
PCB 디패널링에 레이저 기술을 선택하는 이유는 무엇입니까?
기술이 발전함에 따라 전자제품을 제조하는 방법도 함께 발전합니다. 레이저 디패널링 최첨단이 되었습니다 해결책 이상적인 혼합을 제공합니다 정도 그리고 효율성. 전통적인 것과는 달리 기계적인 유도할 수 있는 방법 스트레스 에 판자, 아 레이저 시스템 집중된 광선을 사용합니다 분리된 그만큼 PCBs는. 이 비접촉 방식은 특히 다음을 처리할 때 손상 위험을 최소화합니다. 민감한 구성 요소. 전통적인 방법은 다음과 같습니다. 커터, 예를 들어 라우터, 먼지와 버가 발생할 수 있으므로 추가 세척 단계가 필요합니다. 그러나 레이저 커팅, 최소한의 영향으로 깨끗하고 정확한 절단이 달성됩니다. 판자. 또한, 레이저 디패널링 비교할 수 없는 것을 제공합니다 유연성. 간단한 정사각형이든 판자 복잡한 윤곽이 있는 제품이든 레이저는 다양한 모양과 크기에 적응할 수 있어 디자인 변경에 쉽게 대응할 수 있습니다.
속도를 고려할 때 생산, 아 레이저 디패널링 시스템 눈에 띕니다. 훨씬 더 빠른 속도를 제공합니다. 디패널링 프로세스 에 비해 수동 방법 또는 전통적인 기계적인 시스템. 예전에는 시간이 오래 걸렸던 것이 연산자 이제 해야 할 일을 훨씬 짧은 시간 안에 완료할 수 있습니다. 오토메이션, 전체 속도를 높입니다 생산 사이클. 레이저 디패널링 공정 또한 기준 인식과 같은 기능의 통합도 가능합니다. 즉, 기계가 자동으로 위치를 감지할 수 있습니다. 무대 에 패널 그리고 조정하다 절단 이에 따라 경로가 증가합니다. 정확성 절단의. 레이저를 사용하면 높은 수준의 신뢰할 수 있음 전반적인 제조 작업에서 일관성을 높이고 오류를 최소화할 수 있습니다. 올바른 기술을 선택하는 것은 성공과 실패를 좌우할 수 있습니다. 제조 공정, 원자 램프 기술은 가장 현대적이고 안정적이며 정밀한 당신의 일을 수행하는 방법 pcb 디패널링.
레이저 디패널링은 어떻게 고정밀 절단을 보장하는가?
그 뒤에 숨은 마법 레이저 디패널링 매우 집중된 광선을 사용하여 절단하거나 분리된 그만큼 인쇄 회로 기판 에서 패널 극단적으로 정확성. 달리 기계적인 물리적 힘을 사용하는 방법, 레이저 커팅 재료를 기화시키거나 제거하여 분리합니다. 이를 통해 최소한의 손상으로 깨끗한 절단이 가능합니다. 영 기계적 응력 에 판자. 외과의사의 메스라고 생각하시면 됩니다. 다만 빛을 사용합니다. 레이저 디패널링 고성능의 사용에 크게 기인합니다. 레이저 시스템 및 고급 제어 소프트웨어. 이러한 레이저 시스템, 이든 UV 레이저, 이산화탄소또는 파이버 레이저는 다양한 기능을 제공합니다. 사양 각 범위는 특정 유형의 소재와 두께에 맞게 최적화되어 있습니다. 빔 자체가 매우 작아 가장 복잡한 형상도 정밀하게 절단할 수 있습니다.
고급 제어 소프트웨어는 정확성을 보장하는 데 중요한 역할을 합니다. 레이저 디패널링. 이러한 시스템에는 최적화할 수 있는 알고리즘이 있습니다. 절단 경로, 속도 및 전력 원자 램프 최상의 결과를 얻기 위해. 기준 인식과 같은 기능을 사용하면 원자 램프 자동으로 위치를 찾는 시스템 무대 에 패널 그리고 절단 과정에 필요한 조정을 합니다. 이 모든 것이 각각의 회로기판 정확하게 절단됩니다 사양. 게다가, 레이저 디패널링 비접촉식이다 프로세스, 도구의 마모를 없애고 자주 교체할 필요성을 줄입니다. 커터 교체 및 유지 보수가 필요합니다. 이는 궁극적으로 운영 비용 절감 및 효율성 향상으로 이어집니다. 원자 램프 우리가 할 수 있는 기술 보장하다 가장 높은 수준의 정확성 그리고 최종 제품에 필수적인 일관성 신뢰할 수 있음.
자동 디패널링 시스템의 장점은 무엇입니까?
끊임없이 변화하는 세상에서 전자 제조, 오토메이션 경쟁력을 유지하려면 필수입니다. 자동화 디패널링 시스템은 다양한 기능을 제공합니다 장점, 우리가 접근하는 방식을 크게 바꾸다 인쇄 회로 기판 (PCB) 분리아마도 가장 매력적인 이점 중 하나는 증가일 것입니다. 처리량. 와 함께 자동화된 체계, 무대 될 수 있습니다 분리된 빠르고 일관되게, 어떤 속도보다 훨씬 뛰어납니다. 수동 작업입니다. 즉, 더 많은 작업을 처리할 수 있습니다. 패널 더 짧은 시간 안에 당신의 능력을 크게 향상시킵니다. 생산 효율성과 리드타임 단축을 실현합니다. 또한, 오토메이션 인적 오류의 위험을 줄입니다. 수동 프로세스, 한 연산자 실수를 할 수 있으며 이로 인해 손상이 발생할 수 있습니다. 무대 그리고 폐기물 발생률이 증가했습니다. 자동화됨 기계가 수행하다 디패널링 프로세스 지속적으로 높은 수준으로 정확성 그리고 언제나 신뢰성이 보장됩니다.
속도와 정확성 그 이상으로, 오토메이션 인건비가 절감됩니다. 기계에 대한 초기 투자가 필요하지만, 운영자 그리고 재작업과 폐기물의 감소는 곧 상당한 결과를 가져올 것입니다. 저금이를 통해 회사는 자원을 비즈니스의 다른 영역으로 재분배할 수 있습니다. 자동화된 기계, 당신은 또한 훨씬 더 큰 유연성. 자동화됨 시스템은 다양한 것을 처리하도록 설계되었습니다. 판자 크기와 모양. 오토메이션 기술을 사용하면 최소한의 비용으로 새로운 디자인에 빠르게 적응할 수 있습니다. 전환 times. 오토메이션 also comes with a high level of predictability. Once the system is set up and configured, it will consistently produce results at the desired quality level, giving you consistent results. In short, automated depaneling offers a powerful combination of higher 처리량, reduced costs, greater 신뢰할 수 있음, 그리고 유연성, which is very hard to achieve any other way.
Which Depaneling Method is Best for Sensitive Components?
When we are working with PCBs는 ~와 함께 민감한 구성 요소, the method of 디패널링 we choose matters more than ever. Mechanical methods that involve cutting or punching with a 커터 can create 스트레스 and vibrations that can potentially damage or dislodge these delicate parts. 레이저 디패널링, on the other hand, offers a gentle approach by using a precise beam of light to 분리된 그만큼 무대, making it the preferred method for 인쇄 회로 기판 with sensitive parts. The non-contact nature of the 레이저 공정 means there is no physical contact with the 판자 itself, therefore minimizing the risk of damage to sensitive components. Also, the focused beam generates minimal heat, which reduces the likelihood of thermal damage to temperature-sensitive parts.
하는 동안 레이저 디패널링 is widely recognized for its gentleness, it is also important to understand the specific 레이저 시스템 that’s used and its parameters. UV 레이저 systems, for example, are ideal for materials that are sensitive to heat, as they produce a very small heat-affected zone. However, for thicker 무대, 이산화탄소 or fiber 레이저 시스템 might be a more suitable choice. In choosing the method that’s right for your pcb 디패널링 needs, you must look at the type of 구성 요소 and the specific requirements of the job. We can equip you with the technology to make sure you are handling sensitive parts with the best and most precise method to help 보장하다 high-quality results. You no longer need to worry about any damage to 민감한 구성 요소, by choosing the right 레이저 디패널링 시스템.
What are the Key Differences Between Manual and Automated Depaneling?
As we’ve mentioned already, the world of pcb 디패널링 has evolved tremendously over time, moving from primarily 수동 methods to a more high-tech automated approach. Understanding the key differences between the two methods is vital for deciding which suits your 생산 requirements. The first, and perhaps most obvious, difference is the speed and efficiency. Manual depaneling, where an 연산자 separates the 무대 using hand tools, is very slow, and time consuming. It’s also not consistent because human error is unavoidable. On the other hand, 자동화된 machines can perform 디패널링 operations significantly faster and with greater consistency. This is crucial for handling high-volume 생산 runs, where even minor improvements in efficiency can lead to huge 저금.
Moreover, the level of 정도 differs considerably. 수동 methods depend on the operator’s skill, which can lead to variability in the quality of 분리. 자동화됨 systems, particularly those using 원자 램프 technology, offer a far higher degree of 정도, with minimal chance of error. Additionally, manual depaneling can be very labor-intensive, and require a lot of 연산자 interaction, which, in the end, will lead to higher costs. 자동화됨 machines require less human input, which reduces costs for both labor and material waste due to errors. Also, when it comes to 유연성, 수동 methods may seem adaptable for a variety of 판자 shapes and sizes, 자동화된 systems, especially those with 원자 램프, can also handle a multitude of different designs with easy 전환. The key takeaway is that while manual depaneling is still practical for small scale projects or prototyping, automated depaneling offers greater efficiency, consistency, 정도, and lower costs for larger 생산 runs.
Considering an Innovative Solution for High-Volume PCB Production?
For companies that are constantly dealing with high-volume PCB 생산, finding a dependable and efficient 디패널링 해결책 is paramount. In today’s fast-paced 전자 산업, it is more important than ever for a manufacturer to ensure that their processes are optimized to meet demand while maintaining high quality. Innovative 디패널링 시스템, particularly those using 원자 램프 technology, offer a robust and scalable 해결책 to meet these very demanding needs. The high speed of 레이저 디패널링 allows you to quickly handle large quantities of 인쇄 회로 기판, dramatically improving 처리량 and reducing turnaround times. This quick turnaround will help you to meet tight deadlines and stay ahead in your very competitive marketplace.
Moreover, these innovative systems are not just about speed, but also 유연성 and adaptability. Modern 레이저 디패널링 machines can quickly adjust to different 판자 sizes and designs, making them suitable for a wide variety of 생산 needs. This 유연성 is very valuable because it allows you to rapidly adapt to changes in product designs without having to invest in new 장비. By integrating features such as fiducial recognition and automated material handling, these systems can also operate seamlessly in a fully automated 생산 environment, further decreasing the need for manual intervention. 레이저 디패널링 시스템 offer not just an innovative solution for high-volume PCB 생산 but also a path to more efficient, reliable, and high-quality 조작.
Can We Provide a Solution That Meets Your Specific Depaneling Requirements?
With so many different pcb 디패널링 technologies and methods available, it’s essential to choose a 해결책 that precisely fits your specific 요구 사항. We understand that every 제조 공정 is unique, with varying demands for speed, 정도, material, and budget. That’s why we offer a vast range of 디패널링 장비, from the most advanced 레이저 시스템 to more traditional 기계적인 methods, all designed to meet a variety of different needs. Whether you need to handle 유연한 printed circuit boards (FPC), very thick PCBs는, or have 민감한 구성 요소, we have the right 장비 for you. Our team of experts is ready to help you through the selection 프로세스, making sure you choose the 디패널링 시스템 that perfectly matches your specific needs.
We don’t just provide 장비, but also tailored solutions that integrate seamlessly into your existing 생산 line. We work closely with you, taking into consideration your specific requirements, whether it’s the 오토메이션 level, the required 처리량, or the type of material you are working with. Our goal is to deliver a 디패널링 system that not only meets but exceeds your expectations in terms of efficiency, 정확성, 그리고 신뢰할 수 있음. From 인라인 오토메이션 to stand-alone machines, our range is designed to meet different production volumes and layouts. If you’re unsure where to start, get in touch. We are more than ready to help you navigate the complexity and create a bespoke solution that meets your very specific requirements. Let us help you find the perfect 해결책 당신을 위해 디패널링 요구사항.
How Can You Achieve Lower Cost and Higher Throughput in Your Depaneling Process?
In the 전자 제조 world, the dual goals of lowering costs and improving 처리량 are always at the top of the priority list. Optimizing your 디패널링 프로세스 is a key step in achieving both of these goals. Upgrading from a 수동 or semi-automatic approach to a fully 자동화된 디패널링 시스템 can lead to significant cost 저금. While the initial investment might appear high, the long term benefits, including lower labor costs, reduced material waste, and higher 처리량 all lead to very quick return on the investment. An automated system will consistently deliver high-quality results with minimal need for rework. When we improve 처리량 we can get more done in less time.
올바른 것을 선택하다 기술 can also contribute significantly to cost reduction and improved 처리량. 레이저 디패널링, for instance, provides a non-contact method, which results in fewer damaged 무대 and a reduction in material waste. The higher speed of 레이저 커팅 and minimal need for 커터 replacement also decreases operational costs. If you combine the 레이저 시스템 와 함께 컨베이어, you will further 자동화하다 그만큼 디패널링 프로세스, thus increasing efficiency and ensuring a continuous work flow. Choosing the correct 디패널링 시스템, we can tailor a 해결책 that meets your 사양, maximizes 처리량, and drives down your overall production costs.
Ready to Optimize Your PCB Separation Process? Contact Us Today for a Quote!
After going through the various technologies and methods for pcb 디패널링, I hope you have a clearer understanding of how the correct 장비 당신의 변형이 가능합니다 제조 공정. Whether you are dealing with flexible boards, 민감한 구성 요소, or high-volume 생산 runs, our team is ready to assist you in finding the ideal 해결책 for your needs. From the precision of 레이저 디패널링 to the reliability of 자동화된 시스템, we have the expertise and 장비 to optimize your 인쇄 회로 기판 분리 프로세스. Don’t allow 수동 and outdated methods to slow down your operations or compromise your product quality, let us help you find the perfect fit for your business and bring your 생산 to a whole new level!
Click here to explore our range of 고정밀 디패널링 장비 and discover how we can create a custom 해결책 that improves your manufacturing 프로세스 and drives down your operating costs. Reach out to us today! Let’s discuss your needs, answer any questions, and offer a personalized 인용하다 to equip your factory with the best pcb 디패널링 머신 on the market. We are very confident we can help your company with your 인쇄 회로 필요. 문의하기 now! Let’s begin your journey to more efficient, reliable, and high-quality pcb 디패널링!
자주 묻는 질문
What is the difference between V-groove and router depaneling? V-groove 디패널링 uses a wheel or blade to cut along a pre-scored line (V-score or V컷) on the 패널, which is ideal for straight line 분리. 라우팅 uses a rotating 커터 to cut out shapes, it is much more suitable for complex curves and non-linear shapes.
레이저 디패널링은 기계식 디패널링과 어떻게 다릅니까? 레이저 디패널링 offers greater 정도 and minimizes 기계적 응력 에 판자, 이상적입니다 민감한 구성 요소. Mechanical 디패널링, which involves methods like routing or punching, can be quicker but may induce 스트레스 and vibrations.
What type of laser is best for PCB depaneling? The right 원자 램프 depends on the type of material and application. UV 레이저 are ideal for sensitive materials and thin 무대 due to their small heat affected zone. 이산화탄소 and fiber lasers are suitable for thicker 무대 그리고 더 높은 처리량 생산.
Can I automate my PCB depaneling process? Absolutely! We offer a range of automated depaneling systems, including in-line machines with 컨베이어 belts, which can greatly increase 처리량, improve consistency, and reduce human error in your 제조 공정.
What are the advantages of in-line automation? 인라인 오토메이션 allows for a continuous workflow, integrating 디패널링 with other steps in your 생산 line, leading to improved efficiency, reduced material handling, and lower overall 생산 소송 비용.
주요 내용:
- PCB 디패널링 is a critical process for 분리하다 개인 회로 기판 after assembly on a 패널.
- 레이저 디패널링 이다 고정밀, low-stress method suitable for 민감한 구성 요소.
- Automated depaneling systems offer higher 처리량, reduced labor costs, and improved consistency.
- 올바른 것을 선택하다 디패널링 장비 최적화에 중요합니다 제조 공정.
- 우리는 다양한 제품을 제공합니다 solutions to meet the diverse 요구 사항 의 전자 산업.
- We work with big brands like TP-LINK, Canon, BYD, Flex, TCL, Xiaomi, Lenovo, OPPO, HONOR, Foxconn and many more!
- 문의하기 today for a tailored 인용하다 그리고 당신의 생산 to the next level!
내부 링크:
- 당사의 다양한 제품을 살펴보세요 PCB 라우터 기계 옵션.
- 우리에 대해 더 알아보세요 V-홈 디패널링 솔루션.
- 우리의 것을 발견하세요 PCB/FPC 펀칭기 장비.
- 우리의 것을 확인하세요 자동장비 간소화된 생산을 위해.
- Find the right 부속품 to support your machines.
- 우리의 탐색 SMT 전체 라인 장비 제물.