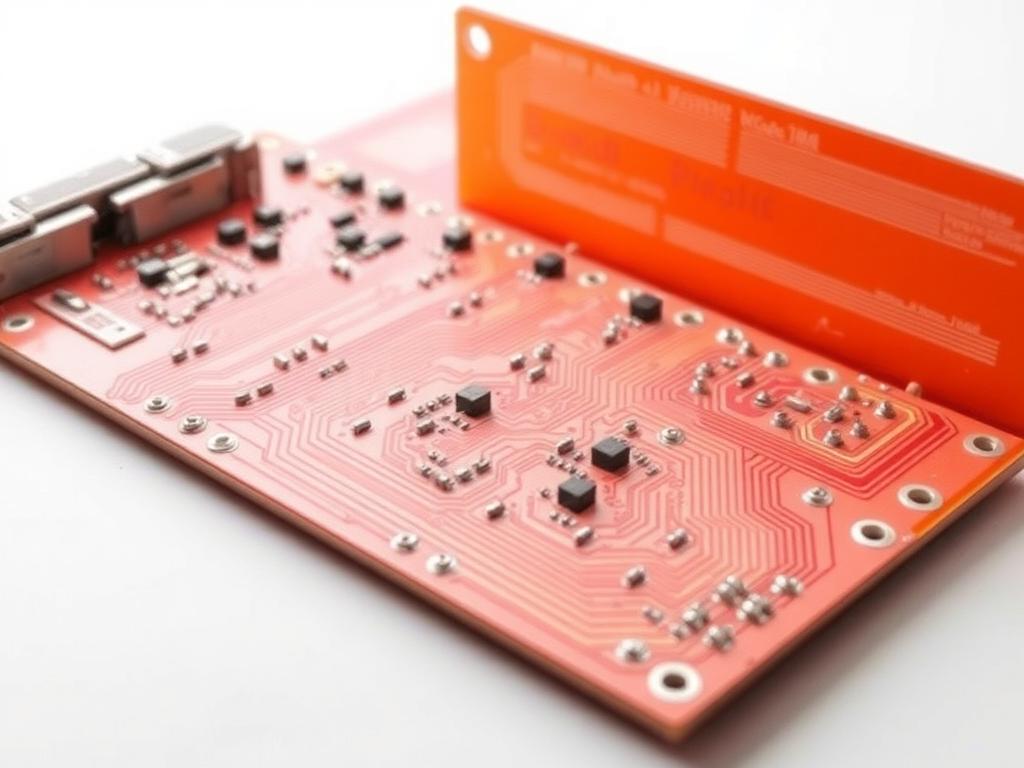
PCBパネル化とはボードを分離することです
PCB パネル化の完全ガイド: 回路基板製造の最適化
PCB パネル化は、プリント回路基板の大量生産方法を変革する重要な製造技術です。この包括的なガイドでは、パネル化によって PCB 製造の生産効率が向上し、コストが削減され、品質が確保される仕組みについて説明します。電子機器メーカー、PCB 設計者、技術専門家のいずれであっても、パネル化を理解することは、生産プロセスを最適化するために不可欠です。
PCB パネル化とは何ですか? なぜ重要ですか?
PCBパネル化は、複数の個別の回路基板を1つの大きなパネルとして配置して製造する製造技術です。このアプローチにより、生産効率が大幅に向上し、処理コストが削減されます。このプロセスは、大量の電子機器アセンブリ生産にとって特に重要です。
製造時間とリソースの最適化が不可欠な分野です。主な利点は次のとおりです。
- 生産コストの削減
- 処理効率の向上
- 品質管理の向上
- 強化された組立工程の自動化
- 製造中のボードエッジの保護
PCBパネル化技術の種類
さまざまなパネル化方法が用意されており、それぞれ異なる要件に適しています。
- V溝パネル化
- PCBパネルにあらかじめ刻まれた線
- ストレートエッジボードに最適
- 簡単な手動分離
- V溝デパネリングソリューションの詳細
- タブルーティングパネル化
- 小さなタブを使用してボードを固定します
- 複雑なボード形状に適しています
- 分離には特殊な装置が必要
- ソリッドタブパネル化
- ボード間の接続を強化
- 重い部品に最適
- PCBルーターマシンのオプションをご覧ください
適切なパネルサイズを選択するには?
最適なパネル サイズの選択は、いくつかの要因によって決まります。
- 製造設備の制限
- コンポーネント配置要件
- 組立ライン仕様
- 材料費の考慮
- 取り扱い要件
「適切なパネルサイズを選択すると、製造コストを最大 30% 削減でき、歩留まり率も大幅に向上します。」 – 業界の専門家
PCBパネル化の設計上の考慮事項
必須のデザイン要素:
- 位置合わせのための基準マーク
- 工具穴
- ブレークルーティングパス
- パネルボーダー仕様
デザイン要素 | 目的 | 要件 |
---|---|---|
基準マーク | アセンブリの配置 | パネルあたり最低3個 |
工具穴 | 製造登録 | 直径2~4mm |
ブレークルート | 取締役会の分離 | 幅0.5~2.5mm |
PCBパネル化における一般的な課題
- コンポーネントクリアランスの問題
- 分離時のPCBにかかるストレス
- ボードの端が不均一
- 登録精度
- パネルの反り
当社の高度なPCBデパネルマシンソリューションをご覧ください これらの課題に対処するためです。
PCBアレイ設計のベストプラクティス
- ボード間の間隔を一定に保つ
- コンポーネントの高さ制限を考慮する
- 適切なブレークルーティングを計画する
- テストポイントと参照指定子を含める
- 自動PCBルーターマシンのオプションをご覧ください
製造プロセスの最適化
生産プロセスは次のように合理化できます。
- 自動処理システムの導入
- 高度なパネル分割装置の使用
- パネルレイアウトの最適化
- 品質管理措置の維持
よくある質問
パネル内の PCB 間に必要な最小間隔はどれくらいですか?
通常、2 ~ 3 mm の間隔が推奨されますが、パネル化方法と製造要件によって異なる場合があります。
PCB に最適なパネル サイズを決定するにはどうすればよいですか?
製造設備の能力、コンポーネントの配置要件、生産量のニーズを考慮してください。標準的なパネル サイズは、多くの場合 18 インチ x 24 インチ以下です。
フレキシブル PCB に最適なパネル化方法はどれですか?
タブ ルーティングは、精度が高く、材料にかかるストレスが最小限であるため、一般的にフレキシブル PCB に適しています。 FPCパンチングソリューションの詳細
パネルの反りの最も一般的な原因は何ですか?
材料の不均一な分布、処理中の熱応力、不適切な保管条件などが一般的な原因です。
コストの考慮とROI
コスト要因:
- 材料利用
- 生産量
- 機器要件
- 人件費
- 品質管理措置
重要なポイント
- PCBパネル化は効率的な製造に不可欠
- 特定のニーズに基づいて適切なパネル化方法を選択してください
- 設計要件を慎重に検討する
- 適切な品質管理措置を実施する
- 適切なパネル取り外し装置を使用する
- コスト効率のためにパネルサイズを最適化
- 設計と製造に関する業界のベストプラクティスに従う
お問い合わせ 当社の高度な PCB デパネルソリューションが製造プロセスを最適化する方法をご確認ください。