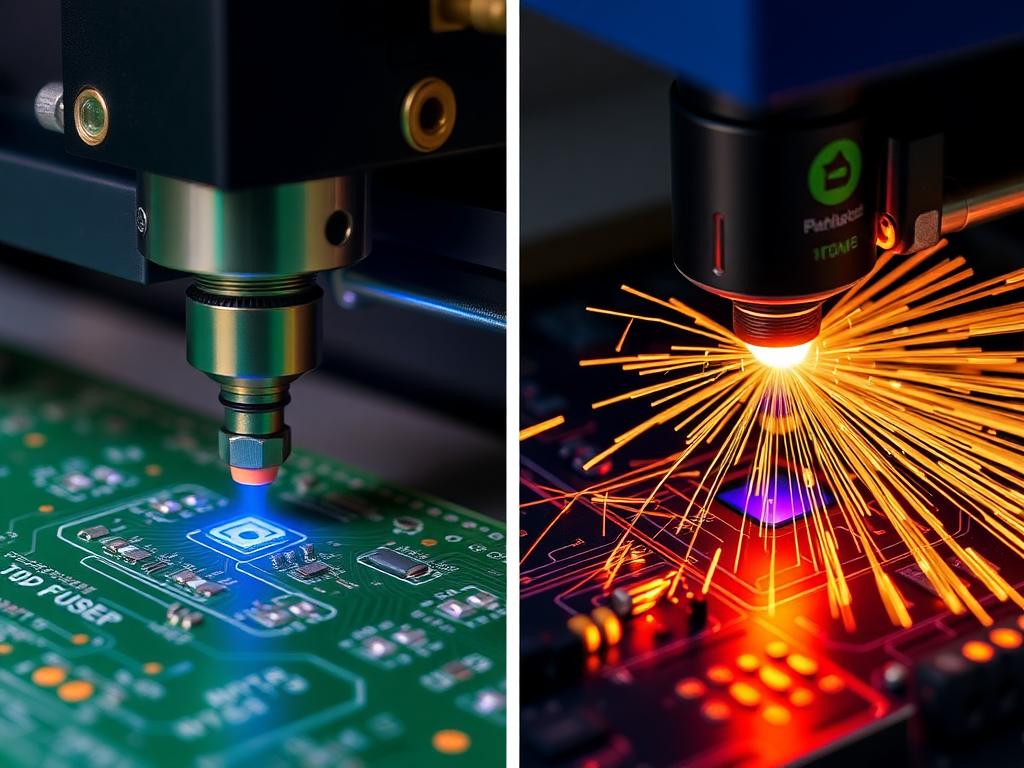
PCBパンチングとレーザーカット
PCB デパネリングの究極ガイド: 現代の電子機器製造のための高度なソリューション
今日の電子機器製造では、すべてのステップで精度、効率、信頼性が求められます。特に PCB デパネル化に関してはそうです。この総合ガイドでは、業界を変革する最先端の PCB デパネル化技術、方法、ベスト プラクティスについて説明します。大規模な電子機器製造施設を管理している場合でも、小規模な PCB アセンブリ操作を実行している場合でも、この記事は PCB 分離プロセスについて十分な情報に基づいた決定を下すのに役立ちます。
PCB デパネル化とは何ですか? また、電子機器製造にとってなぜ重要なのですか?
PCB デパネル化は、個々のプリント回路基板を大きなパネルから分離する重要なプロセスです。このプロセスの品質は、次の点に直接影響します。
- 最終製品の信頼性
- 製造効率
- 生産コスト
- コンポーネントの整合性
現代のPCBデパネルは大きく進化しており、 高度なレーザーデパネルシステム そして 自動ルーターマシン イノベーションの推進をリードします。
さまざまな PCB デパネル方法を理解する
主要なパネル分割技術の比較表
方法精度速度コスト最適な用途レーザーデパネリング最高中高高精度で繊細な部品ルーターマシン高高中大量生産V 溝中最高低単純な直線カット手動切断低低最低プロトタイプ、少量生産
大手メーカーがレーザーデパネリングに切り替える理由
の DirectLaser H3 レーザーオンラインマシン 最先端の PCB 分離技術です。主な利点は次のとおりです。
- 非接触処理
- 熱ストレスが最小限
- 超精密カット
- 機械的ストレスなし
- クリーンでゴミのない操作
生産ラインに適した PCB デパネルソリューションの選択
以下の重要な要素を考慮してください。
- 生産量要件
- ボードの複雑さ
- コンポーネントの感度
- 予算の制約
- 空き状況
PCB のデパネル化プロセスを最適化する方法
効率を最大限に高めるベストプラクティス:
- 定期的なメンテナンススケジュール
- 適切なオペレータトレーニング
- 品質管理プロトコル
- プロセスのドキュメント化
- 環境制御
現代の PCB デパネルにおける自動化の役割
インライン自動PCBデパネルソリューション オファー:
- スループットの向上
- 一貫した品質
- 人件費の削減
- トレーサビリティの向上
- 安全性の向上
PCB デパネル化における一般的な課題とその克服方法
主な課題:
- 部品の損傷
- エッジ品質の問題
- 生産のボトルネック
- 材料廃棄物
- 設備メンテナンス
最新のPCBデパネル装置の高度な機能
現代のシステムのような GAM 380AT PCB 底部パネル剥離機 含む:
- 自動ツールパス生成
- リアルタイムプロセス監視
- 品質検証システム
- MESシステムとの統合
- リモート診断
コスト分析: さまざまなパネル分割ソリューションの ROI
ソリューションの種類初期投資運用コストメンテナンス一般的な ROI 期間基本手動 $1,000-5,000高低 3-6 か月半自動ルーター $15,000-30,000中中 6-12 か月レーザー システム $50,000-150,000低中 12-24 か月インライン自動 $100,000-300,000最低高 18-36 か月
よくある質問
レーザーと機械式デパネルのどちらを選択すればよいですか?
生産量、基板の複雑さ、コンポーネントの感度を考慮してください。レーザーは高精度のニーズに最適ですが、機械的な方法は大量生産に適しています。
デパネル装置にはどのようなメンテナンスが必要ですか?
定期的な清掃、ツールの交換、アライメント チェック、およびキャリブレーションは不可欠です。具体的な要件は機器の種類によって異なります。
すべての PCB 材料をレーザーデパネル化で処理できますか?
一般的な PCB 材料のほとんどは互換性がありますが、一部の複合材料では特定のレーザー パラメータまたは代替方法が必要になる場合があります。
自動デパネルシステムの典型的なスループットはどれくらいですか?
最新のシステムでは、ボードのサイズと複雑さに応じて、1 時間あたり 300 ~ 1200 枚のボードを処理できます。
重要なポイント
- 特定の生産ニーズに基づいてデパネル技術を選択してください
- 初期投資だけでなく総所有コストを考慮する
- 繊細な部品の品質と精度を優先する
- 適切なメンテナンスとトレーニングプログラムを実施する
- 最新の技術開発情報を常に把握
- 経験豊富な機器プロバイダーと提携
覚えておいてください: 適切な PCB デパネル ソリューションは、製造効率と製品品質に大きな影響を与える可能性があります。業界の専門家に連絡して、特定の要件について話し合い、生産ニーズに最適なソリューションを見つけてください。