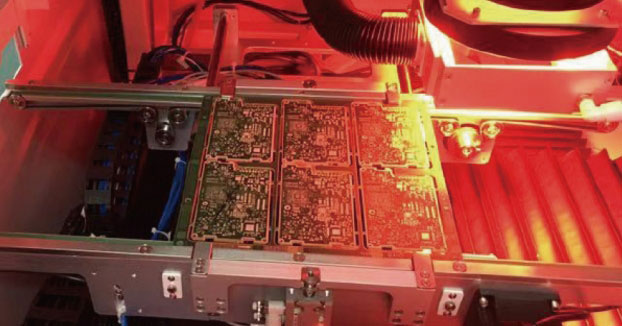
レーザー切断 PCB 基板機械製造、生産能力を 30% 増加
導入
進化し続ける電子機器製造の世界では、精度、効率、カスタマイズが極めて重要です。これらの要素が集約される領域のひとつが、レーザー切断 PCB ボードの使用です。業界が小型化と複雑性の限界を押し広げるにつれ、PCB のパネル分割の従来の方法は、比類のない精度と汎用性を提供するレーザー技術に徐々に取って代わられてきました。この記事では、レーザー切断 PCB の複雑さを詳しく調べ、その用途、利点、そしてそれが PCB の試作と製造の分野にどのような革命をもたらしているかを探ります。
目次
PCB製造におけるレーザー切断の台頭
レーザー切断は、PCB 製造プロセスに革命をもたらすものとして登場しました。ルーティングやパンチングなどの機械的な方法とは異なり、レーザー切断では、集束した光線を使用して材料を切断または彫刻します。この方法により、部品への熱ストレスを最小限に抑えながら極めて正確な切断が可能になり、繊細な回路の完全性が確保されます。
レーザー切断 PCB は、試作段階で特に役立ちます。カスタム PCB 試作の需要が高まるにつれて、メーカーは迅速かつ正確な生産を可能にする方法を必要としています。コストと時間のかかるツールの変更を必要とせずに、設計を迅速に反復できることは、レーザー技術の大きな利点です。
たとえば、プロトタイピング レーザー カッターは、あるデザインから別のデザインにシームレスに移行できるため、短期間の生産や、デザインを完成させるために複数の反復が必要な場合に最適です。この柔軟性が、レーザー切断がカスタム PCB プロトタイピングの推奨方法となった主な理由です。
PCBにレーザー切断を使用する利点
- 精度と正確さ
レーザー カッターは、±0.01 mm という狭い許容誤差で切断できるため、複雑な PCB 設計に最適です。このレベルの精度は、スペースが貴重で、わずかなずれでも故障の原因となる高密度相互接続 (HDI) PCB を扱う場合に特に役立ちます。 - 熱ストレスの軽減
従来の切断方法では、熱が発生することが多く、敏感な部品に損傷を与えたり、反りを引き起こしたりする可能性があります。レーザー切断では、熱を小さな領域に集中させることでこのリスクを最小限に抑え、熱変形の可能性を減らします。 - 汎用性
リジッド PCB、フレキシブル PCB、リジッドフレックス PCB のいずれを扱う場合でも、レーザー切断は幅広い材料と厚さに対応できます。この汎用性により、レーザー切断は現代の電子機器の製造において非常に貴重なツールとなっています。 - スピードと効率
レーザー切断は、正確であるだけでなく、高速でもあります。複雑な形状や複数の層を 1 回のパスで切断できるため、製造時間が大幅に短縮され、試作と大規模製造の両方に効率的な選択肢となります。 - ツールは不要
レーザー切断の最も重要な利点の 1 つは、物理的なツールが不要になることです。これによりコストが削減されるだけでなく、異なるデザイン間の移行が高速化され、生産効率がさらに向上します。
PCBプロトタイピングにおけるアプリケーション
PCB プロトタイプの分野では、レーザー切断は非常に重要です。プロトタイプ用レーザー カッターを使用すると、基板を迅速に製造できるため、設計者は設計を迅速にテストして繰り返し修正することができます。この機能は、迅速な開発サイクルによってイノベーションが推進される航空宇宙、自動車、家電などの業界で特に役立ちます。
カスタム PCB のプロトタイピングでは、多くの場合、設計をすばやく調整する機能が必要です。レーザー カッティングを使用すると、新しいツールや長いセットアップ時間なしで、これらの変更を即座に行うことができます。この柔軟性により、開発プロセスが高速化されるだけでなく、コストも削減されるため、エンジニアや設計者の間で人気のある選択肢となっています。
レーザー切断と従来のパネル分割方法
ルーティング、パンチング、V 溝加工などの従来の方法にはそれぞれ利点がありますが、レーザー切断には見逃せない明確な利点があります。
- ルーティング: ルーティングは効果的ですが、PCB に機械的なストレスを与え、損傷につながる可能性があります。一方、レーザー切断は非接触プロセスであるため、物理的損傷のリスクがありません。
- パンチング: パンチングは高速ですが、複雑なデザインに必要な精度が足りません。レーザー切断は、今日の複雑な PCB レイアウトに必要な精度を提供します。
- V溝加工この方法は直線カットに限定されますが、レーザーカットはあらゆる形状やパターンに対応できるため、はるかに汎用性があります。
この比較により、レーザー切断は単なる代替手段ではなく、多くの PCB デパネル化のニーズに対する優れたオプションであることが明確にわかります。
レーザー切断の環境への影響
レーザー切断は、技術的な利点に加えて、従来の方法に比べて環境に優しいという利点もあります。物理的な接触が不要なため、摩耗した工具や壊れたドリルビットなどの廃棄物は発生しません。さらに、レーザー切断の精度により材料の無駄が減り、より持続可能な製造プロセスに貢献します。
二酸化炭素排出量の削減に取り組む製造業者にとって、レーザー切断は環境に配慮した選択であり、より環境に優しい生産方法を求める世界的な傾向と一致しています。
PCBプロトタイピングに適したレーザーカッターの選択
適切なプロトタイピング レーザー カッターを選択することは、PCB 製造で望ましい結果を得るために重要です。考慮すべき要素には、レーザーの種類 (CO2 またはファイバー)、出力、切断速度、さまざまな PCB 材料との互換性などがあります。たとえば、ファイバー レーザーは一般に金属の切断に適していますが、CO2 レーザーは PCB で使用される基板などの非金属の切断に優れています。
メーカーは、レーザー カッターに付属するソフトウェアも考慮する必要があります。高度なソフトウェアは、自動ネスティングなどの機能を提供して材料の無駄を最小限に抑え、切断プロセスの精度と効率を大幅に向上させることができます。
結論
レーザー切断は PCB 製造の未来を表しています。その精度、汎用性、効率性により、レーザー切断は試作と製造の両方で欠かせないツールとなっています。より複雑で小型化された電子機器の需要が高まり続けるにつれて、レーザー切断技術の採用はますます増加し、現代の電子機器製造の礎としての地位を固めていくでしょう。
PCBデパネルの詳細と最新のレーザー切断技術については、当社の PCBパネル剥離機 ページまたは詳細をご覧ください PCB レーザーによるパネル剥離 当社のウェブサイトで。
よくある質問
- PCB にレーザーカッターを使用する主な利点は何ですか?
主な利点は、高精度とコンポーネントへの熱ストレスの最小化により、複雑な回路の完全性が保証されることです。 - レーザー切断はリジッド PCB とフレキシブル PCB の両方に使用できますか?
はい、レーザー切断は汎用性が高く、リジッド PCB、フレキシブル PCB、リジッドフレックス PCB など、さまざまな材料に使用できます。 - レーザー切断は従来の方法よりも環境に優しいのでしょうか?
はい、レーザー切断は従来の方法に比べて廃棄物が少なく、エネルギー消費も少ないため、より持続可能な選択肢となります。 - PCB 切断に最適なレーザーの種類は何ですか?
CO2 レーザーは通常、PCB 基板などの非金属の切断に最適ですが、ファイバー レーザーは金属に適しています。 - レーザー切断は他のパネル切断方法と比べてどうですか?
レーザー切断は、ルーティング、パンチング、V 溝加工に比べて、優れた精度、低い熱応力、および優れた汎用性を備えています。
まとめ
レーザー切断は、比類のない精度と効率性を提供し、PCB 製造に革命をもたらしています。迅速な反復とカスタム設計が不可欠な試作段階では特に有益です。業界が進化し続けるにつれて、高品質で複雑な PCB の製造におけるレーザー切断の役割は拡大し、現代の電子機器製造に欠かせないツールになります。