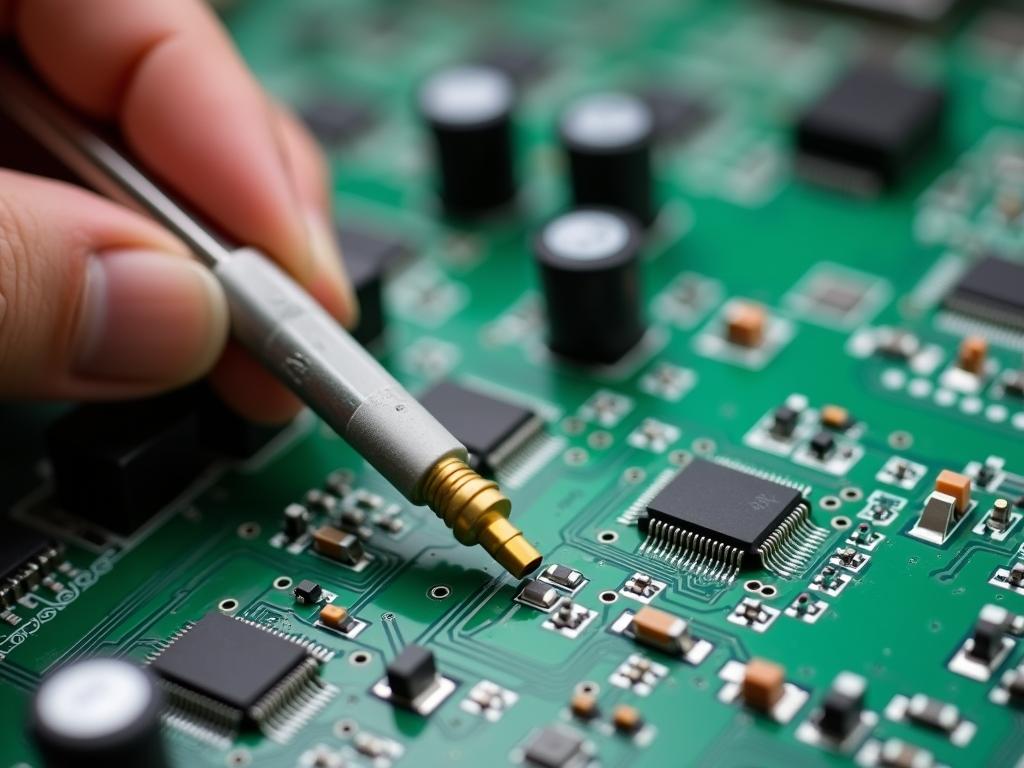
High-speed PCB depaneling machines
High-Precision PCB Depaneling Machine: Revolutionizing Your PCB Production
For over two decades, I’ve been immersed in the world of printed circuit boards (PCBs), witnessing firsthand the evolution of manufacturing processes. One critical stage that can make or break the final product is パネルを外す – the separation of individual circuit boards from a larger panel. Today, I want to share my insights and expertise on how advanced PCB depaneling machines are transforming the electronics industry. If you’re looking to enhance your PCB production, reduce stress on your boards, and boost your overall efficiency, this article is definitely for you.
Why is Precision Depaneling Crucial for High-Quality PCBs?
Having spent years on the manufacturing floor, I can tell you that 精度 in depaneling is paramount. A poorly executed depaneling process can lead to micro-fractures, component damage, and even functional failures of your 回路基板. Think about it: these tiny, intricate 回路基板 are the brain of your electronics. You need to separate them carefully and delicately. For high-quality PCB(プリント基板)、 パネルを外す must be a low-stress process that ensures each ボード is perfect. We’ve seen how even small imperfections in the パネル除去プロセス can result in significant performance and quality issues.
We work with some of the biggest names in electronics like TP-LINK, Canon, BYD, Flex, TCL, Xiaomi, Lenovo, OPPO, HONOR, and Foxconn. They demand the best, and we deliver with our 高精度 パネルを外す solutions. This is not just about cutting apart boards; it is about ensuring each component functions optimally. Precise depaneling ensures that the structural integrity of the プリント基板 is maintained. This means no broken traces, no stressed components, and a perfect product every time. It’s about minimizing the risk of defects in the final product.
What are the Different Types of PCB Depaneling Machines Available?
Over the years, I’ve seen a variety of パネル取り外し機, each designed for specific needs. We have three main product categories: PCBルーターマシン, V溝デパネルマシン、 そして PCB/FPCパンチングマシン, as well as solutions for レーザーデパネル. Each type utilizes a different method to separate the individual 回路基板. Let’s dive in to learn what’s right for your needs.
ルーターマシン are versatile and can handle complex shapes and intricate designs. They use a ルータービット カットする ボード along a programmed path, which provides a flexible approach for different shapes and sizes. V-groove パネルを外す uses a blade or a series of blades to push the ボード along pre-scored Vカット. Punching machines are designed for high-volume production with simple rectangular or circular designs. All these 機械 are incredibly effective, but they each have an ideal situation, and a less ideal situation.
How Does a PCB Router Machine Work and What Are Its Benefits?
As a veteran in the field, I’ve seen the rise of PCBルーターマシン and they are indeed a game-changer. These 機械 使用する スピンドル to hold a high-speed ルータービット that cuts through the ボード. This approach is incredibly flexible, allowing for complex contour shapes and intricate designs. The ルーター can navigate any shape on your パネル, whereas a v-cut system is limited to straight lines.
One of the main benefits is the low-stress approach to PCB パネルの取り外し. Unlike some other methods that can introduce stress to the 回路基板、 ルーターマシン gently removes the material. Additionally, many modern routers, like our GAMシリーズ, integrate features such as ccd camera alignment and dust collection systems. This allows for 高精度 and a cleaner work environment. They’re great for フレキシブル production lines too as they can cut a variety of shapes, making them ideal for companies that need to adapt quickly to product changes.
When Should You Consider a V-Groove Depaneling Machine?
V溝 パネルを外す is a method I have come to appreciate for its efficiency and simplicity, especially for separating pre-scored PCB panels. This method employs blades or rotary tools to push and 別 の ボード along v-cuts that are precisely milled into the パネル. V-groove machines are fast and cost-effective for high-volume production of straight-line separations and are often used when the 回路 design allows.
Many facilities often used V-cut machines for projects with simple board outlines that can be 分離された with straight cuts. The advantage is they allow for 高速 and are ideal for a mass production. It is a very コスト効率が良い solution for simple designs. However, they may not be suitable for more intricate designs or when there is no vスコア. They are typically inline, and a fast method of separating many PCB(プリント基板) efficiently.
What Are the Advantages of Using a PCB/FPC Punching Machine?
In my experience, a PCB/FPCパンチングマシン is the ideal solution for applications where speed and uniformity are paramount. These 機械 use a specially designed die to punch out PCB(プリント基板) から パネル. They are excellent for high-volume production of simple shapes. In the PCB パネルの取り外し process, a punching machine creates clean, defined edges for 回路基板 that have a simple shape, such as a circle or a rectangle, where high スループット is the priority.
パンチング 機械 are also known for their ability to handle flexible circuit boards, hence the name FPC, which stands for Flexible Printed Circuit. They are often used in applications where ストレスフリー separation is crucial. While it’s true they have a limited use case (they can only work with very simple outlines), for mass production of simple boards, a punching 機械 is ideal. They ensure consistency of separation for higher 生産性.
Why is Automation Essential in Modern Depaneling Processes?
Looking back on my career, I can see that the move towards オートメーション で パネルを外す is what has enabled manufacturing to improve. Manual パネルを外す, with an オペレーター, can be inconsistent, slow, and prone to errors. Automated systems, on the other hand, are fast, precise, and can work consistently for longer. Modern パネルを外す systems are often 列をなして, allowing for seamless integration into a 生産ライン.
We’ve seen our customers achieve significant improvements in their 生産効率 by incorporating 自動PCB handling and 積み込みと積み下ろし. It minimizes the need for manual handling, which leads to reduced errors and higher スループットこのレベルの オートメーション not only boosts 生産性 but also frees up personnel to focus on other crucial tasks.
How Can the Right Accessories Improve Your Depaneling Results?
Just like a good chef needs the right tools, the same is true for depaneling. The right accessories can significantly improve your results. For a ルーターマシン、 ルータービット is key. We offer a variety of milling cutters, each designed for specific materials and applications. A sharp, high-quality ルータービット is crucial to ensure a clean and smooth cut, and a good スピンドル helps reduce vibration.
さらに、 備品 that holds the ボード in place needs to be designed to securely grip the パネル without introducing stress to the 回路基板. A good 真空システム is essential to keep the work area clean, and we offer those as well. Don’t underestimate the value of a good accessory when depaneling your ボード.
What is the Role of SMT Whole Line Equipment in Depaneling?
The electronics manufacturing industry has changed since I started working in the field. Today the スマトラ (表面実装技術) whole line equipment is at the heart of modern manufacturing processes. デパネリング is just one part of the process, but is necessary when the board is created in a パネル. When the PCB パネルの取り外し is inline with the rest of the スマトラ line, 生産効率 is increased.
スマトラ lines have 自動 equipment to load, assemble, and then unload the final 回路基板. When the パネルを外す step is integrated as part of this 生産ライン, 生産性 is streamlined. The 列をなして flow leads to a faster and more efficient operation. It makes optimization possible and minimizes manual handling. With our experience we can help you 統合する depaneling in an existing スマトラ ライン。
How Does Laser Depaneling Technology Enhance PCB Separation?
レーザーデパネル is another marvel of modern technology that I have seen firsthand. This method uses a focused レーザ beam, often a 紫外線レーザー, to cut through the ボード. レーザー切断 offers incredibly precise and clean cuts, making it perfect for complex shapes and sensitive components. It also offers low stress, which is an advantage.
レーザーデパネル is particularly suited for thin and フレキシブル materials, often used in applications that require high precision. Our レーザーデパネル machines, like the DirectLaser series, include features like ccd camera alignment and are optimized for various materials. One of the greatest advantages with laser technology is that it can cut any shape required, and it only has to be programmed once.
How Can You Choose the Best Depaneling Solution for Your Specific Needs?
Throughout my career, I’ve seen companies struggle to choose the right パネルを外す solution. The decision should always be based on a few factors. First, consider your 回路基板, complexity, and quantity you need. If you are working with complex designs and varying board shapes, a ルーターマシン might be the best choice. If you are in mass production for simple straight-line cuts, then the v-groove may be ideal. For high-volume of simple shapes then a punching 機械 is the right direction.
You’ll also want to consider the 生産効率 and your 生産ライン. If you have a high throughput, 列をなして system, automation is a must. Finally, don’t forget to factor in the budget, and the overall goal. We have an experienced team who can help you find the best solution for your business and we will personalize the setup to meet your unique 生産 要件。
よくある質問
What is the difference between a PCB router and a v-groove separator? あ PCBルーター uses a rotating ルータービット to cut out the 回路基板, allowing for complex shapes and designs while the v-groove separator uses a blade to push the ボード along pre-scored lines, limiting it to straight cuts.
レーザーデパネリングはあらゆるタイプの PCB に適していますか? レーザーデパネル is best suited for complex, high-precision applications and thinner, フレキシブル materials. While versatile, it may not always be the most コスト効率が良い for high-volume production of very simple shapes.
What are the key benefits of automated depaneling systems? 自動化 パネルを外す システムは増加した スループット、より高い 精度, less human error, reduced manual handling, and better integration with the rest of your 生産ライン.
How do I minimize stress on my circuit boards during depaneling? To minimize stress, use low-stress methods like ルーター または レーザーデパネル. Be sure that your 機械 is properly calibrated and that the 備品 is designed to hold the ボード without excess pressure.
Can I customize a depaneling system for my specific needs? Yes, we can カスタマイズ 私たちの パネルを外す systems to meet your specific requirements and personalize it for your unique 生産 ニーズ。
In Summary
- 精度 で パネルを外す is essential for high-quality PCB(プリント基板).
- PCBルーターマシン offer flexibility for complex shapes.
- V溝 パネルを外す is efficient for straight-line cuts.
- Punching machines are ideal for high-volume production of simple shapes.
- オートメーション is key to increasing スループット そして 生産性.
- レーザーデパネル provides extremely precise cuts for complex or delicate designs.
- The right accessories can make a big difference in your results.
- 列をなして パネルを外す can integrate into a modern スマトラ ライン。
- Choosing the best パネルを外す solution depends on your specific needs and 回路基板.
- Our team is here to help you find the perfect solution and カスタマイズ it for your company.
If you’re looking to elevate your PCB パネルの取り外し process, I encourage you to explore our range of machines and contact us today. Let’s work together to optimize your manufacturing process and improve the quality of your プリント基板. You can also explore our other pages for more information. See our products like the GAM 380AT PCB 底部パネル剥離機、 ZM30-ASV 全自動鋸型V溝PCBデパネル, and our PCB/FPCパンチングカッティングマシン and learn more about each of these product categories. Let’s improve your PCB パネルの取り外し 今日!
© 2024 PCB Depaneling. All rights reserved. プライバシーポリシー.