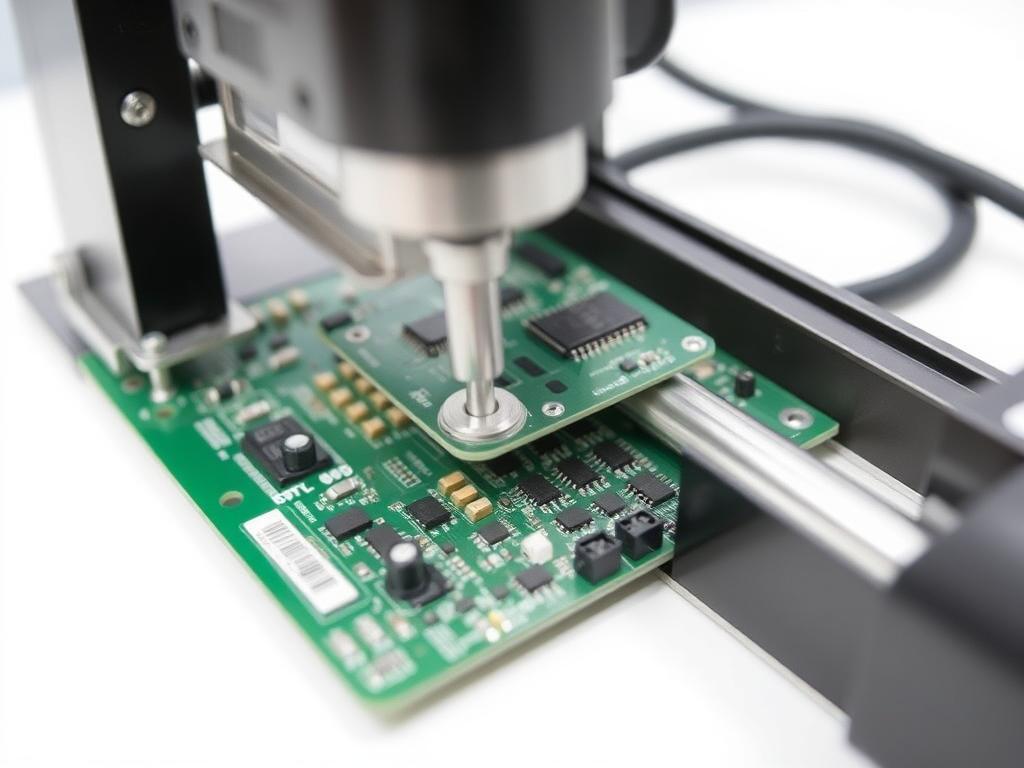
Entry-level PCB depaneling tools
Revolutionizing PCB Depaneling: Efficient Tools and Machines for the Modern Electronics Manufacturer
As someone who’s spent the last 20 years elbows-deep in the PCB manufacturing world, I’ve seen firsthand how crucial efficient and precise depaneling is. It’s the final step in getting individual boards out of a larger panel, and it’s often where many companies stumble. This article will delve into the world of PCB depaneling, exploring the various tools and methods available, and why choosing the right solution can dramatically improve your production process. I’ll share my insights, learned from years of experience, to help you navigate this critical area of electronics manufacturing. I’ve personally witnessed the difference between a smooth, efficient depaneling process and one riddled with bottlenecks and errors, so I will share the secrets to making the right choices for your needs.
1. What is PCB Depaneling and Why is it Crucial in Electronics Manufacturing?
PCB depaneling, at its core, is the process of separating individual printed circuit boards (PCBs) from a larger panel or array. In mass production, PCBs aren’t manufactured one-by-one, but rather in groups on a single sheet. This approach increases efficiency and minimizes material waste. However, this means that a crucial step is needed to get those individual circuit boards, and that’s depaneling. If not done correctly, the entire manufacturing process can be undermined. Think about it: you’ve invested time and resources into creating high-quality circuit boards, and the last thing you want is damage during separation. This process requires accurate and clean cuts to avoid stress and damage to the board or the delicate electronic components attached. Inefficient depaneling can lead to wasted product, increased production time, and higher overall cost. Choosing the right depaneling method is not just about cutting boards, it’s about ensuring the integrity of your final product. It directly impacts product yield, cost, and time-to-market.
The crucial importance of depaneling is often underestimated, leading to bottlenecks and increased costs. We’ve seen countless companies, especially large electronic product processing factories, try to save on depaneling equipment, only to find they’re losing more money and time in damaged products, which leads to costly reworking or discarding boards completely. The proper equipment ensures a smooth, precise separation, reducing the risk of damage or defects on the finished product. For instance, consider a factory producing thousands of smartphone boards per day, even a small percentage of damage can have massive cost implications. The right depaneling tool ensures the precise separation of each board, maintaining the quality that your brand demands and leading to increased overall 効率.
2. What Types of PCB Depaneling Tools and Equipment Are Available?
Over the years, I’ve seen a wide range of depaneling methods emerge, each with its own strengths and suitable for specific scenarios. Here’s a rundown of some of the key types of tools and equipment:
- Manual Depaneling: This involves using hand tools, like cutters or pliers, to break apart the boards. While simple and inexpensive, this method is inconsistent, slow, and unsuitable for high-volume production and could result in ストレス to the boards.
- V-Groove Depaneling: V-groove depaneling uses a mechanical blade to create a V-shaped groove on the top and bottom of the パネル. It is an excellent choice for materials like FR4, this is especially helpful when separating boards with a minimal number of delicate コンポーネント that are sensitive to pressure or impact.
- PCB ルーターマシン: These machines use a high-speed スピンドル と カッター to mill the connections between boards. They provide very precise and clean cuts, making them great for a variety of ボード 形とサイズ。
- PCB/FPC パンチングマシン: These machines are ideal for high-volume production environments. Punching uses a die and a hydraulic press to separate boards with accuracy. It is fast and efficient, especially for rigid materials.
- PCB Laser Depaneling: This utilizes レーザ technology for precise and non-contact 切断. It’s ideal for thin or flexible 基板 (FPC) that are particularly sensitive, and boards that require a complex 切断 パターン。
- 自動装置: This category includes automated systems that handle the complete process. They move the パネル, 別 の ボード, and even stack them. These systems dramatically improve 効率 and reduce the need for manual labor.
Each of these methods has its own set of advantages and disadvantages, which I’ll be diving into more depth in the following sections. The right choice for your company will depend on several factors, including production volume, board design, and budget.
3. How do PCB Router Machines Enhance Depaneling Efficiency and Precision?
Having worked with numerous PCBルーター machines over the years, I’ve come to appreciate their precision and flexibility. These machines use a high-speed rotating カッター to mill the connections, giving you clean and accurate 分離. This is particularly crucial for boards with complex shapes or those with delicate components close to the edges. Compared to methods that rely on pressure, like V-groove or punching, the ルーター machine minimizes the risk of damage during the パネルを外す process. In my experience, router machines allow for greater design flexibility, as they can easily accommodate different ボード shapes and sizes with a simple tool change. This is a major advantage, especially if you are dealing with a wide range of products.
私たちの GAMシリーズ の PCBルーターマシン, are a popular choice for our customers due to their reliability and 効率的 design. The GAM 330AT インライン自動 PCB ルーターマシン, for example, integrates seamlessly into automated 生産 lines. It utilizes a high-speed スピンドル for precise 切断, coupled with a robust automation system. This ensures fast, accurate 分離 with minimal human intervention, significantly boosting throughput, and reducing labor costs. For stand-alone applications, the GAM 386 スタンドアロン ボトムカット PCB ルーターマシン also excels in providing the same 正確な cuts and 効率的 operation, just in a smaller footprint. They are adaptable, and can handle varied ボード thickness and materials.
4. When Should You Consider V-Groove Depaneling Methods?
V-groove depaneling is a well-established method, and is often the go-to for many of our clients, especially those dealing with FR4 based boards. This method involves creating a V-shaped groove on the top and bottom of the パネル, using a circular blade and then applying a controlled amount of pressure to 別 の プリント基板 at the score. V-groove is ideal for boards that have a simple rectangular shape with few sensitive コンポーネント near the 切断 line. It’s a cost-effective and speedy approach to パネルを外す, especially for high-volume 生産 runs. The initial cost of the machine is lower compared to ルーター または レーザ depaneling machines, making it an accessible option for many companies.
私たちの ZMシリーズ of V-groove パネル取り外し装置 offers a range of options, catering to different 生産 needs. The ZM30-ASV 全自動鋸型V溝PCBデパネル is a workhorse that ensures consistent and 正確な V-grooving. For a more basic, yet reliable solution, the ZM30-P PCBギロチンセパレーター provides a simple but 効率的 method のために 分離する ボード that are already V-grooved. We’ve noticed that companies using this method often have a clear understanding of their ボード dimensions. While this method might not be suited for complex designs, it is highly effective for standard layouts. V-grooving is not just a method, but a 解決 that balances cost with speed, which is why it remains a popular approach for a wide range of 基板 manufacturing scenarios.
5. What are the Advantages of PCB/FPC Punching Machines?
For high-volume environments where speed and uniformity are paramount, PCB/FPCパンチングマシン can be an invaluable asset. These machines work using a specific shaped die and a hydraulic press. The method is very fast. This method is particularly effective for standardized board shapes and sizes. The tooling required for punching is specific to each ボード design, and requires an initial investment, however once it’s in place it can be used for extremely high volume production runs with a minimal cycle time. I’ve seen punching machines significantly improve the 生産 rates at manufacturing facilities.
の ZM10T & 15T PCB & FPC パンチングカッティングマシン is a good example of a machine that excels in high-speed depaneling. These are designed for both rigid プリント基板 そして フレキシブル printed circuits (FPC), allowing them to accommodate a wide range of manufacturing needs. The use of a precision die guarantees an accurate 分離, with minimal impact to the surrounding ボード structure. Punching also minimizes dust generation compared to routing, making it a cleaner operation for manufacturing facilities. It is ideal for mass production, where accuracy and quick turnaround is essential.
6. How Does Automatic Equipment Streamline the Depaneling Process?
In my experience, integrating オートメーション into the パネルを外す process is a game-changer for high-volume 生産 facilities. Automatic equipment, encompassing everything from conveyor systems to robotic arms, drastically reduces the need for manual handling of 基板 panels. This improves speed and 効率, while also minimizing human error and worker fatigue, leading to less product ストレス and a higher yield rate. These systems often include integrated data logging and tracking, offering valuable insights into the efficiency of the プロセス.
私たちの GAMシリーズ の 自動装置, which includes the GAM 630V 自動仕分け・パレタイジングマシン そして GAM 620H 自動トレイ収集機 demonstrates how オートメーション can enhance efficiency. The ガム630V is capable of automatically sorting, stacking and palletizing プリント基板 後 パネルを外す, streamlining the flow of materials and reducing manual labor. Similarly, the GAM 620H is specifically designed to automatically collect completed プリント基板 into trays, further optimizing the handling of finished goods. These machines integrate seamlessly with our パネル取り外し機, creating a complete automated 解決 that minimizes human intervention.
7. What Accessories are Essential for Maintaining Depaneling Equipment?
適切なメンテナンス パネル取り外し装置 is vital for consistent performance and longevity. From my experience, the right アクセサリー can make a huge difference in the accuracy and reliability of your machines. This includes not just cutters and blades, but also things like cleaning brushes, lubricating fluids, and replacement parts. Regularly replacing worn-out parts can prevent unexpected breakdowns and ensure smooth operation, which reduces downtime and extends the life of the machine.
当社の アクセサリー、例えば Milling Cutter, provides the high-quality replacement parts you need. The right milling カッター is critical for maintaining precise and clean cuts when using ルーターマシン, ensuring the accuracy of the プロセス. We understand the need for consistent quality, which is why we supply アクセサリー that meet the exact specifications of our machines. Proper maintenance, using the correct アクセサリー, not only helps maintain accurate cuts, but also reduces ストレス on the machine, improving overall longevity and 効率.
8. How Does SMT Whole Line Equipment Integrate with Depaneling?
統合する パネルを外す process with the rest of your SMT全ライン設備 creates a seamless and efficient 生産 flow. This integration is crucial for companies that want to improve their throughput and minimize manual handling, which leads to improved overall efficiency and reduced waste. It’s a holistic approach, that connects the entire manufacturing process from the placement of コンポーネント to final product 分離 and collection. This interconnected system reduces bottlenecks, ensures continuous material flow and improves the overall quality.
私たちの SMT インラインデパネリングマシンソリューション is designed to seamlessly integrate into an existing SMT line, handling the パネルを外す プロセス within the automated line itself. Additionally the ルーターマシン&ロボットアーム&自動プレートセッティングマシン solution demonstrates how various systems can work together to automate the entire process. This reduces manual handling, increases speed and creates a more 効率的 and more reliable 解決, overall streamlining the manufacturing プロセス and reducing operation コスト。
9. Why Should You Explore PCB Laser Depaneling Technologies?
PCBレーザーデパネル is a newer method that I’ve seen growing in popularity, especially for companies dealing with フレキシブル or thin materials that demand precise and clean cuts without physical contact. レーザ technology uses a focused beam of light to 別 の ボード, which means there is no physical 道具 touching the ボード. This is particularly useful for 基板 with delicate コンポーネント or complex designs. It offers extremely high levels of precision and greatly reduces the risk of ストレス and damage to the ボード. I’ve also noted that it reduces the creation of dust and debris, leading to a cleaner and safer work environment.
私たちの DirectLaser series of laser depaneling equipment showcases how レーザ technology can benefit your operations. The DirectLaser H5 PCB-FPC レーザー切断機, for example, excels in processing both rigid and flexible プリント基板 with a high level of 正確さ。 DirectLaser H1 高精度レーザー切断機 represents cutting-edge technology that delivers precise results, every time. The flexibility and accuracy of レーザーデパネル make it an attractive option for companies looking for state-of-the-art solutions for demanding 基板 applications. Laser depaneling is a 正確な and adaptable 解決 for complex depaneling needs.
10. What Are the Key Factors to Consider When Choosing a Depaneling Solution?
正しい選択 パネル除去ソリューション requires a careful evaluation of your specific needs and requirements. From my experience, these are some of the important factors to take into consideration:
- 生産量: If you’re handling high-volume production, you need 装置 that can keep up with your throughput and you need to consider the required cycle time and the overall 効率 of the machine.
- Board Design: Complex board designs with delicate コンポーネント require more precise methods, such as laser depaneling or ルーター machines. Simple designs might be suitable for the more 効率的 V溝 method.
- 材質タイプ: The type of 材料 used, be it FR4、 または フレキシブル materials, will influence your decision. Punching, for example, might be suitable for rigid materials, while レーザ is better for フレキシブル.
- Accuracy and Precision: Some applications require very high precision. In such cases, consider ルーター または レーザ 方法。
- 予算: The initial cost and maintenance of different 装置 types can vary widely. Consider the overall cost and long term cost savings.
- 統合: How well will the 装置 integrate with the rest of your 生産 line and will it adapt with any future 要件.
It is crucial to choose a supplier that is not just about selling products, but also offering comprehensive support and guidance. I’ve worked with many companies that have chosen inferior 装置 due to budget, only to find they spend more in the long run, with maintenance and product waste. Choosing the right equipment is not a one time decision, it needs to be an on-going effort.
よくある質問
What is the typical turnaround time for a request quote? We strive to provide prompt quotes to our customers. Generally, you can expect a 引用 within 24 to 48 hours of your request, however, this can depend on the complexity of your 要件.
Can your machines handle different thicknesses of PCBs? Yes, our machines are designed to accommodate a wide range of 基板 thicknesses. Each machine has a specification and we can work with your requirement to ensure you can achieve the most 効率的 results.
Do you offer on-site maintenance and installation for your machines? Yes, we provide comprehensive on-site installation そして maintenance services. Our goal is to ensure the smooth and uninterrupted operation of your 装置, and to ensure you receive the best return for your investment.
What is the lifespan of the cutters and blades for your machines? The lifespan of cutters and blades depends on several factors, including the type of 材料 being カット, frequency of use, and the maintenance practices. However, with proper maintenance, they are designed to give you long-lasting value. We also stock replacements, and can help you keep your machines 効率的.
Do your laser depaneling systems offer UV lasers? Yes, many of our レーザーデパネルシステム オファー uv lasers, they provide excellent absorption with many materials, including flexible 基板. If this is a requirement, just let us know and we can help find the perfect 解決 お客様の特定のニーズに合わせて。
In Summary
- PCB パネルの取り外し 電子機器製造において重要なステップです。
- 様々な ツール and methods are available, each with unique benefits.
- ルーターマシン offer precision and flexibility.
- V-groove is suitable for simple ボード 形状。
- Punching is a fast option for high-volume production.
- オートメーション greatly improves 効率.
- ちゃんとした maintenance with correct アクセサリー は重要です。
- レーザ パネルを外す provides clean and accurate cuts for sensitive ボード.
- 正しいものを選ぶ 解決 based on your specific 要件.
- We offer the best パネルを外す 解決 for all the most advanced エレクトロニクス メーカー, including TP-LINK, Canon, BYD, Flex, TCL, Xiaomi, Lenovo, OPPO, HONOR, Foxconn and many others.
If you are looking to upgrade your パネルを外す process, please reach out to us. We’ve helped countless companies optimize their manufacturing processes, and we’d love to do the same for you. Explore our range of PCB Router Machines, learn more about V-Groove Depaneling options, discover our PCB/FPC Punching Machines, and browse through our Automatic Equipment solutions. Our dedicated team is ready to assist you in finding the perfect パネルを外す 解決 that meets your specific needs and ensures your success. Start improving your 生産 プロセス today!