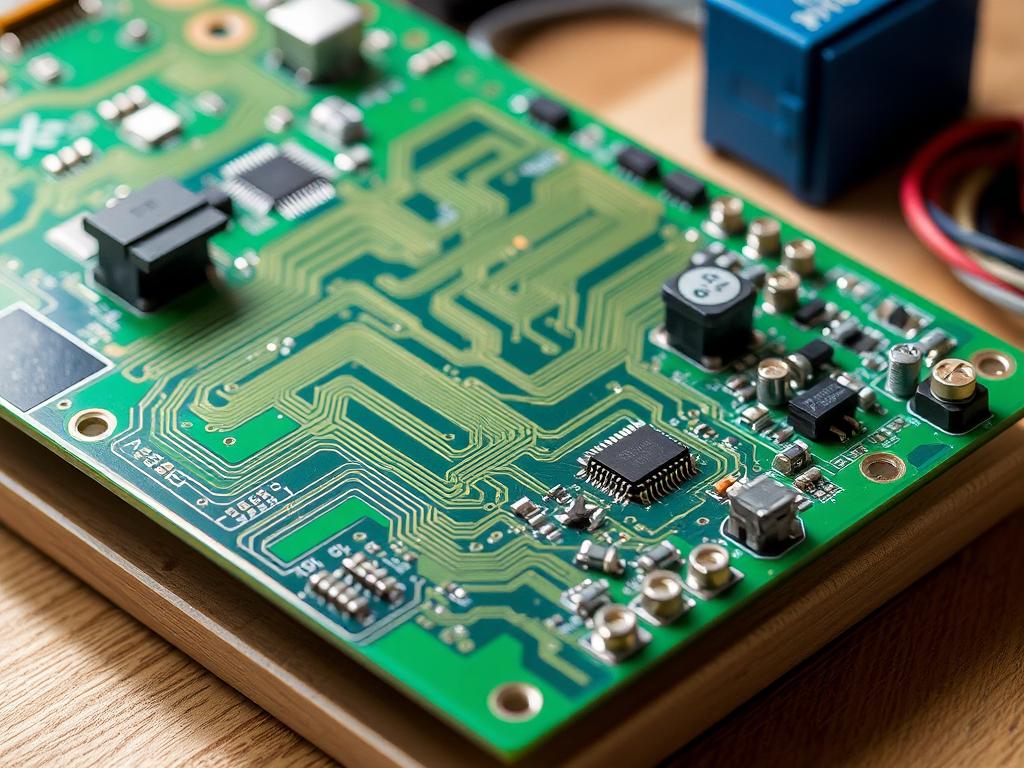
FPC depaneling machine
Precision PCB Depaneling: Mastering the Art of Circuit Separation for Flex, Rigid, and Laser Applications
For over two decades, I’ve been immersed in the intricate world of पीसीबी विनिर्माण, witnessing firsthand the evolution of डिपैनलिंग techniques. The journey from individual सर्किट बोर्ड on a large panel to separate, functional units is a critical one, and it’s where precision and efficiency truly matter. This article delves into the crucial process of पीसीबी डिपैनलिंग, exploring the different methods available, especially focusing on लेजर डिपेनलिंग, and why choosing the right solution can make or break your production goals. If you’re involved in पीसीबी विनिर्माण and looking to optimize your processes, this is a must-read. Whether you are dealing with rigid पीसीबी, flexible pcbs, or the increasingly popular flex pcbs, understanding the nuances of डिपैनलिंग is paramount. We’ll explore how advancements in technology, like लेजर तकनीक, have changed the game.
1. What is PCB Depaneling and Why is it so Critical?
In the world of पीसीबी विनिर्माण, पीसीबी are typically produced in large panels containing multiple boards. This approach is cost effective and allows for efficient handling during the पीसीबी असेंबली process. But these individual मुद्रित सर्किट बोर्ड must be separated before they become part of their respective इलेक्ट्रॉनिक उपकरणों, and that’s where डिपैनलिंग comes in. डिपैनलिंग, also called एकवचन, is the हटाने की प्रक्रिया व्यक्ति सर्किट बोर्ड from the larger panel. This पृथक्करण प्रक्रिया requires precision to ensure that the सर्किट isn’t damaged and that the final product functions perfectly. Think of it like carefully cutting out shapes from a sheet of paper—you need the right tools and technique for a clean result. Incorrect डिपैनलिंग यह हो सकता है यांत्रिक तनाव पर पीसीबी, potentially causing damage to components and traces, and ultimately leading to failure of the final product. The डिपैनलिंग प्रक्रिया is therefore a crucial step that bridges the gap between efficient panel production and functional end products.
The role of डिपैनलिंग is vital. It directly impacts the quality and reliability of the final सर्किट बोर्ड. From my 20 years of experience, I’ve seen that selecting the right डिपैनलिंग method not only ensures that the individual पीसीबी are separated without any problems, but it also contributes significantly to overall efficiency. Improper techniques can lead to several issues, such as cut edge burrs, micro-cracks, and even damage to the delicate प्रवाहकीय traces. These defects can have devastating effects on the performance of the assembled devices and can drastically increase production costs due to rework and scrapped parts. The importance of precise and reliable डिपैनलिंग cannot be overstated, making it a critical area for continuous improvement and innovation within the पीसीबी विनिर्माण प्रक्रिया।
2. What are the Main Depaneling Methods for Circuit Boards?
Over the years, I’ve seen a variety of डिपैनलिंग विधियाँ come and go, each with its own strengths and weaknesses. Among the most common pcb depaneling methods are:
- वी-ग्रूव डिपैनलिंग: This involves using a वि कट पर पीसीबी panel. Then the panel is broken along these lines. This is a cost-effective approach but is suitable only for straight lines.
- रूटर कटिंग: ए रूटर is used to cut along the separation line. This is a versatile method suitable for various shapes. It is known for its flexibility. Router cutting does create more dust and requires a स्थिरता to hold the board in place.
- पंच डिपैनलिंग: ए पंच and die are used to stamp out individual boards. This is fast but is only suitable for simple shapes and requires expensive tooling.
- लेज़र डिपेनलिंग: Utilizing लेजर तकनीक सटीक रूप से काटने के लिए पीसीबी, this method offers high precision, minimal यांत्रिक तनाव, and can handle complex shapes. It’s a more recent advancement, and one that I believe is the future of डिपैनलिंग, particularly for flexible pcbs.
Each method comes with its own set of advantages and disadvantages. The choice of the काटने की विधि depends on various factors, including the type of pcb materials used, the complexity of the board shape, and the required THROUGHPUT। उदाहरण के लिए, rigid pcbs, particularly those made of फ़्र4 with basic shapes, can be separated using वि कट or even die cutting methods. However, for intricate designs and materials, such as लचीले मुद्रित सर्किट बोर्ड made of polyimide, लेजर डिपेनलिंग emerges as the preferred choice due to its unmatched precision and minimal impact. As technology advances, the need for more precise and versatile methods is driving innovation in डिपैनलिंग.
3. Why is Laser Depaneling Gaining Popularity?
In my opinion, लेजर डिपेनलिंग represents a monumental leap forward in पीसीबी डिपैनलिंग. The main reason for its increasing popularity is its unparalleled precision. Unlike mechanical methods that can exert यांत्रिक तनाव पर पीसीबी and cause damage, लेजर डिपेनलिंग वाष्पीकृत करने के लिए प्रकाश की एक केंद्रित किरण का उपयोग करता है सब्सट्रेट, resulting in a clean, precise cut edge without physical contact. This is particularly important when dealing with delicate लचीले मुद्रित सर्किट बोर्ड that require a very precise and minimal impact approach. Furthermore, the लेज़र can handle complex shapes and intricate cuts, something that other methods struggle to achieve.
लेज़र डिपैनलिंग also allows for greater flexibility in terms of material processing. Whether you’re working with फ़्र4, polyimide, or other pcb materials, द लेज़र can be adjusted to suit the specific requirements of each material. This adaptability means that a single लेजर डिपैनलिंग सिस्टम can be used for a range of different पीसीबी types, reducing the need for multiple डिपैनलिंग मशीनें and streamlining the विनिर्माण प्रक्रिया. For instance, I’ve seen that many of our customers who have switched to लेजर डिपेनलिंग have seen a significant increase in both precision and efficiency, as well as reduced material waste. From experience, I can confirm the advantages of the laser, this advanced काटना method leads to less post-processing and improved quality, especially in high-precision applications. The laser depaneling process has truly reshaped the approach to the पृथक्करण प्रक्रिया मॉडर्न में पीसीबी विनिर्माण.
4. What are the Advantages of Using Flexible PCBs in Electronic Devices?
The advent of new technologies has dramatically transformed the field of electronics, and लचीले पीसीबी have emerged as a game-changer. Flexible printed circuit या फ्लेक्स पीसीबी, made of materials such as polyimide, offer a host of advantages over traditional rigid pcbs. I’ve witnessed the rise of flexible pcbs across a broad range of products due to their unique characteristics and capabilities. One of the main advantages of flexible boards is their ability to conform to almost any shape. They can be bent, folded, and twisted without compromising their electrical functionality, allowing for innovative designs and compact solutions in इलेक्ट्रॉनिक उपकरणों. They are also lighter and thinner, making them ideal for applications where space and weight are critical.
लचीले सर्किट बोर्ड have revolutionized the way we approach the design and manufacturing of इलेक्ट्रॉनिक उपकरणों. They play a vital role in the manufacturing process of many consumer electronics, including smartphones, wearable technology, और ऑटोमोटिव applications. The ability of लचीले मुद्रित सर्किट बोर्ड to accommodate dynamic flexing and vibration makes them incredibly robust and reliable, and this is why they have found widespread use in demanding applications. From my experience, flexible pcbs offer a much greater level of design freedom compared to rigid pcbs, making it possible to create products that are not only functional but also aesthetically pleasing and ergonomic. These characteristics have fueled the growth of flex pcbs and their adoption across diverse industries. The process of flexible board production has become increasingly efficient, and the versatility they offer is unmatched.
5. How does Laser Cutting impact Flexible PCBs?
जब यह आता है flexible pcbs, लेजर कटिंग है काटने की विधि of choice for high precision and minimal यांत्रिक तनाव. Traditional mechanical पीसीबी काटना methods often exert pressure on the delicate सब्सट्रेट, which can lead to damage or deformation of the फ्लेक्स पीसीबी. However, a लेज़र, like a fine surgical tool, precisely cuts without any physical contact, therefore लेजर कटिंग is an ideal solution for processing these delicate लचीले सर्किट बोर्ड.
The impact of लेजर तकनीक पर flexible pcbs is truly transformative. The लेज़र provides incredible precision. The laser depaneling process यह सुनिश्चित करता है कि cut edge is exceptionally clean, with no burrs or debris that might compromise the performance of the finished सर्किट. The ability of the लेज़र to handle intricate shapes and complex layouts is crucial for the design freedom that flexible pcbs offer. When comparing it to other डिपैनलिंग विधियाँ, I’ve found that लेजर कटिंग not only reduces the risk of damage but also improves the overall quality and reliability of the पीसीबी. This results in better performance and longer lifespan of इलेक्ट्रॉनिक उपकरणों. का उपयोग यूवी लेजर technology also ensures a very clean cut, minimizing contamination of the लचीला मुद्रित सर्किट panel and maintaining high technical cleanliness.
6. What are the key Considerations When Choosing a Depaneling Method?
सही का चयन डिपैनलिंग method is a crucial step that involves considering a variety of factors. When working with pcb materials पसंद फ़्र4 के लिए rigid pcbs the choice might be simpler, but for materials like polyimide में इस्तेमाल किया flexible pcbs, the considerations are more complex. First and foremost, you need to consider the material of your सर्किट बोर्ड. Some materials are more sensitive to यांत्रिक तनाव than others. The thickness of the पीसीबी and the type of components and traces present also impact which method is best. The complexity of the सर्किट बोर्ड design, including its shape and the number of individual पीसीबी on the panel, also affects the decision. The desired THROUGHPUT and the available budget are also critical factors. Methods like वि कट हैं प्रभावी लागत for simple shapes and large volumes, whereas लेज़र is more suited for complex shapes and low to medium volumes.
From my experience, selecting the best डिपैनलिंग approach involves a careful balance of performance, cost, and efficiency. It’s not always a matter of going for the most expensive or technologically advanced option. For example, a high volume of rigid pcbs might benefit from वि कट, which is a lower cost method and is fast. However, if you require high precision and need to minimize the risk of damage to flexible pcbs, then लेजर डिपेनलिंग is a better option, even if it entails a higher initial investment. Moreover, automation plays a major role in improving the डिपैनलिंग प्रक्रिया. Automating with डिपैनलिंग मशीनें not only increases the speed of production, but also reduces the risk of human error, which ensures consistent results and minimizes waste. Careful assessment of these parameters helps ensure the most efficient and reliable method for your specific पीसीबी आवश्यकताएं।
7. How Can Automation Improve the Depaneling Process and Reduce Mechanical Stress?
Automation is a vital component in modern पीसीबी विनिर्माण, enhancing the डिपैनलिंग प्रक्रिया in numerous ways. Automated डिपैनलिंग मशीनें can significantly increase THROUGHPUT while minimizing यांत्रिक तनाव. With automated systems, a लेजर डिपैनलिंग सिस्टम operates with extreme accuracy, and the risk of human error is minimized, resulting in consistent quality. In my experience, automation brings several key advantages, particularly when dealing with high volumes and complex shapes.
One of the key benefits of automation is the increased speed and efficiency of the cutting and depaneling. Automated systems can work continuously with minimal operator intervention. Automation is a powerful tool for achieving higher production rates, lower costs, and consistent results. Automation doesn’t just improve efficiency; it also helps to minimize यांत्रिक तनाव पर पीसीबी. By integrating robotic arms and other automated handling equipment, we can reduce manual handling, which reduces the risk of any unwanted damage to the सर्किट बोर्ड. The combination of लेजर तकनीक and automated systems offers the best of both worlds: high precision and high efficiency. In essence, automation transforms डिपैनलिंग from a manual process into a smooth, optimized, and reliable operation.
8. Where is the Future of PCB Depaneling Headed?
As the field of electronics continues to advance, I believe the future of पीसीबी डिपैनलिंग will be driven by several key trends. First, लेजर डिपेनलिंग will become the dominant method, especially as the demand for लचीले मुद्रित सर्किट बोर्ड and intricate designs increases. The precision and versatility of लेजर तकनीक make it ideal for processing the increasingly complex पीसीबी that are being manufactured. We will also see advancements in automation, with the integration of artificial intelligence to optimize डिपैनलिंग processes and further improve precision.
Another trend that I foresee is the move towards more environmentally friendly and sustainable practices in पीसीबी विनिर्माण. This includes developing methods that reduce waste and conserve resources. The integration of लेजर डिपेनलिंग with automated robotic systems will also continue to evolve. We’ll likely see smaller footprints, more energy-efficient operations, and the ability to process larger panels. In the long term, the trend will focus on greater flexibility, higher precision, and sustainable manufacturing processes that minimize costs while maximizing efficiency. The advent of new technologies will help manufacturers meet the demands of an ever-evolving industry.
9. How to Contact Us for PCB Manufacturing Solutions?
If you’re looking for reliable, high-precision डिपैनलिंग solutions, please don’t hesitate to हमसे संपर्क करें. We have over 20 years of experience in the पीसीबी विनिर्माण industry, and we’re confident that our solutions can meet the most demanding requirements, especially for large electronics product processing factories and individual पीसीबी players. Whether you need पीसीबी रूटर मशीन solutions, or advanced लेजर डिपैनलिंग सिस्टम के लिए flexible pcbs, we have the expertise and technology to help you succeed. As a leading पीसीबी डिपैनलिंग मशीन manufacturer, our products are trusted by world leading companies such as TP-LINK, Canon, BYD, Flex, TCL, Xiaomi, Lenovo, OPPO, HONOR, Foxconn and many other Fortune 500 companies. We can provide tailored solutions to meet your individual requirements.
हम समझते हैं कि हर पीसीबी विनिर्माण operation is unique, which is why we take a personalized approach. We focus on developing solutions that fit your specific needs and your budget. We offer a range of equipment, from stand-alone डिपैनलिंग मशीनें to integrated solutions for entire श्रीमती पूरी लाइन उपकरण production lines. For example, for companies requiring high THROUGHPUT, our fully automated लेजर डिपेनलिंग systems offer the perfect solution. We encourage you to reach out and tell us about your specific requirements, and let’s explore how our experience and technology can optimize your manufacturing process. Let us know what are your challenges in your पीसीबी डिपैनलिंग प्रक्रिया, so we can offer advice and give you a tailored solution.
10. Explore Similar Posts and the Tag Cloud for more Insights?
For additional information, insights, and resources, we invite you to explore our similar posts. You can find articles on various topics related to पीसीबी विनिर्माण, लेजर तकनीक, और स्वचालन. Our blog is a great source for learning about the latest industry trends and advancements. You can also check our tag cloud, where you will find specific tags related to your search, such as flexible pcbs, लेजर कटिंग, या डिपैनलिंग प्रक्रिया. This will give you access to a range of articles covering many different aspects of पीसीबी तकनीकी।
We try to provide you with a wealth of knowledge that can help you optimize your processes and make informed decisions. Whether you are an expert in the field or just starting out, our blog and resource center have something for everyone. Feel free to browse through the articles and discover new ideas, and share them with your colleagues and peers. We hope that these resources serve as useful aids in your pursuit of excellence in the dynamic and fast-paced world of पीसीबी विनिर्माण. Also check our products page to check our vast array of डिपैनलिंग मशीनें for your needs. You can find machines like the GAM 380AT पीसीबी बॉटम डिपेनलिंग मशीन, द GAM 360AT इन-लाइन पीसीबी सेपरेटर मशीन या GAM336AT इन-लाइन स्वचालित पीसीबी डिपेलिंग मशीन. You can also find information on our v-groove depaneling machines like the ZM30-ASV पूर्ण स्वचालित आरी-प्रकार V-नाली PCB डिपैनलिंग और ZM30-LT इन-लाइन मल्टी-नाइफ PCBA डिपेलर. If you are interested in the लेजर डिपेनलिंग solutions you can explore डायरेक्टलेजर H5 पीसीबी-एफपीसी लेजर कटिंग मशीन.
FAQs
के बीच क्या अंतर है कठोर और flexible pcbs?
Rigid pcbs are made from materials like फ़्र4 and are solid and inflexible. Flexible pcbs, on the other hand, are made from materials like polyimide and can be bent, folded, and twisted.
कौन डिपैनलिंग विधि is best for high-precision applications?
लेज़र डिपैनलिंग is generally preferred for high-precision applications because of its clean cut edge and minimal risk of damage to the सर्किट बोर्ड.
कर सकना लेजर डिपेनलिंग be used for all types of pcb materials?
हाँ, लेजर डिपेनलिंग can be adjusted to suit the specific requirements of different pcb materials, शामिल फ़्र4, polyimide, and others.
What is the role of automation in the डिपैनलिंग प्रक्रिया?
Automation improves efficiency, increases THROUGHPUT, and reduces the risk of human error during the डिपैनलिंग प्रक्रिया.
Is it possible to combine different डिपैनलिंग विधियाँ?
Yes, it is possible to combine different डिपैनलिंग विधियाँ depending on the specific requirements of the पीसीबी being processed and the overall pcb manufacturing process. This is not very common though.
Summary
- पीसीबी डिपैनलिंग में एक महत्वपूर्ण कदम है manufacturing process of flexible printed and rigid सर्किट बोर्ड, impacting the final quality and reliability of इलेक्ट्रॉनिक उपकरणों.
- Depaneling methods शामिल करना वि कट, router cutting, पंच, और लेज़र.
- लेज़र डिपैनलिंग is gaining popularity due to its high precision, minimal यांत्रिक तनाव, and ability to process complex shapes.
- लचीले मुद्रित सर्किट बोर्ड offer advantages such as flexibility, light weight, and suitability for dynamic flexing applications.
- लेजर कटिंग is particularly suitable for flexible pcbs because it minimizes यांत्रिक तनाव and ensures a clean cut edge.
- The choice of a डिपैनलिंग method depends on material type, design complexity, THROUGHPUT requirements, and budget.
- Automation plays an important role in improving the efficiency and precision of the डिपैनलिंग प्रक्रिया.
- का भविष्य डिपैनलिंग is oriented toward लेज़र and automation integration for optimal performance.
- Contact us for tailored पीसीबी विनिर्माण solutions and to optimize your production process.
- Explore our blog for resources, insights, and articles, and do not forget our tag cloud.